3D打印产业洞察和投资逻辑:变革传统工艺,市场蓝海可期
时间:2023-08-21 15:17 来源:南极熊 作者:冯驿 阅读:次
增材制造是一种快速成型技术,更容易实现复杂零件的一次成型,精度较高且设计制造周期更短。增材制造的技术路线几十种,各类技术路线在材料、成型精度、尺寸、复杂度、制造速度上各有擅长,适用于不同应用场景。未来随着激光器效率提升和面向增材制造的设计能力逐渐提升,产业应用将持续在更多场景落地。
基于和行业内上百位从业者的交流,我们形成了系统化的增材制造投资逻辑。对于增材制造行业的投资布局主要关注三方面:公司层面,关注产业链定位、是否为行业头部以及创始团队的能力。技术层面,关注公司所选技术路线的壁垒强弱、技术成熟度、技术所切入场景的唯一性。商业化层面,关注切入场景的市场容量以及下游行业的需求和起量势能(见文尾)。除此之外的研究结论包括:
一、增材制造定义
增材制造是一种快速成型技术,通过创建数字模型将材料逐渐累加的方法来制造实体零件。增材制造的基本流程和原理如下:
区别于减材制造通过切割材料毛坯来创建最终产品,增材制造通过添加零件来形成最终产品。
从原材料角度,增材制造需要采用特定原材料,材料成本往往更高,且可利用的原材料种类较少,但是原材料利用率更高;从制造工艺角度,增材制造更容易实现复杂零件的一次成型,且精度较高;从制造周期角度,增材制造设计验证的周期更短,效率更高;从制造成本角度,增材制造从低价格敏感度的航空航天和医疗领域逐渐向其他领域渗透。
二、行业发展
20世纪60年代和70年代,增材技术技术处于起步阶段,几乎完全没有商业市场,对研发的投入也很少。研究工作验证了第一批现代AM工艺,包括20世纪60年代末的光聚合技术,1972年的粉末熔融工艺,以及1979年的薄片叠层技术。
20世纪80年代和90年代初,出现了很多创新的AM技术,同时一部分增材技术被成功商业化。创新型的技术包括1989年麻省理工学院的3D打印技术,与90年代的激光束熔化工艺。成功商业化的增材制造技术包括光固化(SLA)技术、固体熔融沉积技术(FDM),以及激光烧结技术(SLS)等。增材制造相关专利和学术出版物的数量明显增多,但是受限于高成本和有限的材料选择,尺寸限制以及有限的精度,增材制造技术在工业上的发展比较缓慢,只能用于小量快速原型件或模型的制作。1986年全球第一家3D打印企业3D systems成立标志着3D打印进入产业化。
20世纪90年代和2000年代是增材制造行业的增长期。现有技术逐步得到提升和改进,同时新技术逐渐实现了商业化。产业逐渐开始开发专门应用于增材制造行业的软件。出现了AM的专用文件格式,AM的专用软件,如Materialise的Magics开发完成。设备的改进和工艺的开发使3D增材制造产品的质量得到了很大提高,开始被用于工具甚至最终零件。
2009年之后,随着欧美3D打印的底层专利在2009-2015年陆续到期,我国的增材制造开始进入发展的快车道。
2011年到2020年,增材制造的产业化进程不断推进,行业市场规模保持高速增长,海内外3D systems、stratasys、铂力特等公司不断上市,同时GE、佳能、东芝等企业纷纷涉足增材制造市场,在航空航天等多个领域持续落地增材制造应用。
未来,随着产业化的进程不断推进,行业技术的成熟度也将逐渐提高,值得关注的未来技术包括激光器、DfAM等。
激光器发展有助于显著提升打印效率
激光器效率的提升受到业界普遍关注。目前全球各家公司均在尝试不同的激光器效率突破技术路线,其中VulcanForms Inc. 发明了 100 千瓦激光 PBF 技术并将其商业化并集成到专有的数字制作系统中。Seurat Technologies 发明了一种激光 PBF 技术,该技术使用燼一种光学可寻址光阀技术来支持该公司所谓的区域印刷。该公司声称该过程比传统激光 PBF 技术快 10 倍。另一个发展是激光束热分布的优化。这样可以更精确地控制热沉积,从而最大限度地提高构建速度,提高材料质量,并最大限度地减少飞溅和烟雾。此外,初创公司 SunMetalon 也在筹集资金通过层而不是点或线的方式来加热金属,从而进一步提高金属 AM 的速度。
DfAM方法可以有效提升产品性能
DfAM指的是面向增材制造的设计,即结构设计工程师利用增材独特的工艺优势去构建产品的设计过程。在产品设计制造之初同时考虑到设计、增材工艺、增材产品认证方法、增材制造生产模式与产能等众多因素。
通过DfAM 技术对设计环节能力的提升,可以优化打印过程中和打印后处理的工艺水平,DfAM 的方法可以提高产品性能并减少材料和重量,降低制造和组装的复杂性。目前Conflux 和 GKNAdditive 等公司正在使用 DfAM 的方法开发的高效热交换器。下图显示了DfAM对于增材制造不同环节的影响:
增材制造可以大致分成金属类增材制造和非金属类增材制造。整体分类概览如下图:
1、金属增材制造
金属增材制造可以分为熔化成型和未熔化成型两类,相关的工艺有铺粉、送粉、送丝等,能量源分为激光、电子束、电弧等。其中未熔化成型不做重点介绍,该技术按照材料状态分片材、板材、粉末;按照工艺超声波焊接、搅拌摩擦焊、冷喷涂等。
熔化成型主要包括粉末床熔化(PBF)和直接能量沉积(DED)两大类。在市场份额层面,根据 AMPOWER,以营收计算,2021 年 PBF、DED 各占据 83.8%和 9.1%的市场份额。且预计到 2026 年,PBF、DED 将各占据 74%和 8.6%的市场份额。
1.1粉末床熔化(PBF)
PBF是一种铺粉工艺的增材制造技术,PBF按照不同的能量源可以分为激光熔化和电子束熔化。
其中选择性激光烧结 (SLS)、选择性激光熔化 (SLM)能量源都是激光。SLM的成型原理与SLS极为相似,不同点在于SLM的激光温度较高,会在成型过程中完全熔化所有金属粉末。因此SLM整个打印过程需要在惰性气体保护的腔体中进行,以避免金属发生氧化。这给SLM带来了更好的成型性能,相比SLS制造的金属零件的致密度更高,力学性能更好,尺寸精度更高、表面粗糙度也更高。但是SLM工艺参数复杂、制造速度偏低,尤其是面对需要大量支撑结构的复杂零件,SLM的打印成本、时长会明显提高。
适合应用于载人飞船引擎的冷却道、喷射头、节流阀等结构复杂程度非常高的结构上面。(注:SLS技术既可以应用于金属,也可以用于非金属)
电子束熔炼 (EBM)的能量源为电子束。相比于激光路线,EBM 精度略低但速度高:SLM 沉积速率通常在 0.1kg/h, 而 EBM 速度可达数倍。EBM相比于SLM在几乎所有步骤里都存在很明显的成本优势:特别是在设备运行、热处理与支撑拆除方面。此外,相比于 SLM,EBM 无需后加工处理残余应力。且EBM 的支撑能够很轻易的移除,因此其拆除成本很低。
1.2直接能量沉积(DED)
DED整体的打印效率高于PBF,但是精度逊于 PBF。按照材料状态分送粉式和送丝式,能量源包括激光、电子束、电弧等。
此外,金属增材制造技术中经历高能量输入的增材制造工艺需要后处理,后处理操作通常包括粉末清理、支撑去除、构建板分离、机加工、清洁、抛光或表面增强以及焊接等连接方式。将零件和构建板分离之前,通常需要消除应力,确保残余应力不会导致零件变形。不同工艺的去支撑、去应力、热处理等需求汇总如下:
2.1还原聚合
聚合还原是一种树脂3d打印技术,工艺过程为光线精确地指向液体塑料的特定点或区域以使其硬化。第一层固化后,构建平台将向上或向下移动(取决于打印机)少量(通常在 0.01 和 0.05 毫米之间),下一层固化并与前一层连接。聚合还原按照不同光源可以分为SLA、DLP、LCD等。
立体光刻 (SLA)使用固态激光来固化部件,是目前世界上研究最为深入、技术最为成熟、应用最为广泛的一种3D打印技术。该技术的优点是尺寸精度高、表面质量优良、系统分辨率较高,可以制作结构比较复杂的模型或零件。缺点包括零件较易弯曲和变形、设备运转及维护成本较高、材料不利于长时间保存等。
数字光处理 (DLP)使用数字光投射器(而不是激光)在一层或树脂上同时闪烁每一层的单个图像(或为较大的部件多次曝光)。每一层曝光都需要完全相同的时间,比SLA 中的点激光方法效率更高。用于生产更大的零件或更大体积的零件。
液晶显示器 (LCD)使用 LCD 屏幕而不是数字微镜设备 (DMD),也就是使用数百个单独发射器的阵列,而不是像激光二极管或 DLP 灯泡那样的单点发射光源。LCD 单元成本低,这项技术已成为低价桌面树脂打印机领域的首选技术。常见应用包括注塑模状聚合物原型和最终用途部件、珠宝铸造、牙科应用、消费品。
2.2材料挤出
熔融沉积建模 (FDM、FFF)是典型的材料挤出工艺,该工艺过程为将线轴上的一根(或一次几根)灯丝装入 3D 打印机,然后送入挤出头中的打印机喷嘴。打印机喷嘴或多个喷嘴被加热到所需温度,使灯丝软化,从而使连续的层连接起来形成一个坚固的部件。材料挤出是成本较低的 3D 打印方法,无需激光器等贵重原件,成本低、速度快。且该工艺干净、简单、易于操作且不产生垃圾。对使用环境没有限制,可以放在办公室或者家庭环境使用,维护简单、体积小无污染 。但是材料挤出的成型精度相对SLA工艺较低,成型表面光洁度不如SLA工艺。
3、其他增材制造技术
其他增材制造技术包括材料喷射、粘结剂喷射、片材层压等,这些技术既可以应用于金属,也可以应用于非金属。
3.1粘结剂喷射
粘结剂喷射的工艺过程是用重涂刀片在构建平台上涂抹一层薄薄的粉末。然后,带有喷墨喷嘴的打印头在床上方经过,选择性地沉积粘合剂液滴以将粉末颗粒粘合在一起。层完成后,构建平台向下移动,刀片重新涂覆表面。然后重复该过程,直到整个部分完成。该技术的独特之处在于打印过程中没有热量。粘合剂喷射速度快且生产率高。但是聚合物粘合剂喷射的材料选择有限,并且生产的部件结构性能较低。
3.2片材层压
片材层压的工艺过程为将非常薄的材料片堆叠和层压在一起以产生 3D 物体或堆叠,然后通过机械或激光切割以形成最终形状。材料层可以使用多种方法融合在一起,包括加热和声音,具体取决于材料,材料范围从纸张、聚合物到金属。具体包括层压物体制造 (LOM)、超声波固结 (UC)等,相关材料有纸张、聚合物和片状金属等。该技术的优点是可以快速生产,复合打印。缺点为精度低,浪费多,部分零件需要后期制作。抗拉强度和弹性差,不能制造中空件;受制于材料影响,利用 LOM 技术打印的零件易吸湿膨胀,表面有台阶纹。
3.3材料喷射
材料喷射将材料沉积到构建表面上,然后使用紫外光固化或硬化该层。逐层重复,直到对象完成。由于材料以液滴形式沉积,因此材料仅限于光敏聚合物、金属或蜡,它们在暴露于紫外线或高温时会固化或硬化。材料喷射过程需要支撑结构,通常也是在构建过程中同时使用可溶解材料来进行3D打印,然后在后处理步骤中去除支撑材料。该技术可以提供出色的细节、高精度和光滑的表面。使用材料喷射技术进行打印的主要缺点是成本高,并且紫外线活化的光敏聚合物会随着时间的推移失去力学性能并且会变脆。
不同增材制造技术的在成型尺寸、粘结性能、工作环境等方面各有差异,详细的技术比较如下图:
同时,各类技术路线的产业化进程也有所不同,具体进展如下:
全球增材制造市场空间广阔,未来仍保持高速增长:根据Wohlers Associates数据,2022年全球增材制造全球市场规模180.27亿美金,过去34年的复合增长率达到25.6%,预计2030年市场规模达到853亿美金(近6000亿人民币)。
中国增材制造市场短期有望突破500亿,渗透率仍有较大提升空间:根据中国增材制造产业联盟,2022年我国3D打印市场规模330亿,2018-2022年的复合增长率为28%。根据赛迪咨询数据,2024年中国的3D打印市场规模有望进一步提升,突破500亿元。目前增材制造在制造业渗透率不足0.1%,处于产业化的前期,长期制造业渗透率3-5%。
中国增材制造市场规模在全球领先:Wohlers Associates 的研究表明,我国工业级增材制造设备安装量全球领先。在全球安装的所有工业增材制造 (AM) 系统中有 34.9%在北美,28.4% 安装在亚太地区,30.7% 在欧洲。按照国家来看,美国、中国、德国是工业级增材制造设备安装量最多的三个国家。
增材制造行业集中度不高,市场竞争逐渐激烈:根据Wohlers Associates 研究,2022 年前 10 家最大的系统制造商贡献了整个增材制造行业约 27.21 亿美金的产值,占比15.1%。非品牌厂商的市占率呈现逐年提升趋势:服务供应商以前基本从 3D Systems、EOS 和 Stratasys 等成熟的 AM 制造商处购买系统。然而,2022 年服务供应商购买的 290 台机器中,包括了156 台非成熟制造供应商的 AM 系统(占比53.8%),连续第三年从非成熟公司购买设备呈现增长趋势。
五、产业链
3D打印上游包括材料类、核心硬件、辅助设备等。其中材料包括金属材料和非金属材料。核心硬件类涵盖激光器、振镜系统和引擎,辅助设备包括3D建模软件、扫描仪等。3D打印的中游包括3D打印设备制造商和服务商,按照材料性能分为金属类和非金属类。下游面向的应用领域包括航空航天、医疗、模具等。
上游:激光器、振镜
激光器是增材制造产业链上游的核心硬件,可以分为光纤激光器、CO2激光器等。
激光器的国产化比例不断提升:根据 Laser Focus World 数据,2020 年中国光纤激光器市场规模约为 13.8 亿美元,其中国产比例约 56%,达 7.73 亿美元。美国的光纤激光器制造商 IPG 占据了中国光纤激光器市场的最大份额(2019年42%),但是总体市场销售份额明显下降。国产品牌占比显著上升,包括来自中国的锐科激光、创鑫激光和杰普特等企业。增材制造所使用的激光器功率普遍较低,此类中低功率的光纤激光器基本完成了国产化进程。
振镜类也是增材制造上游的零部件,据《2021年中国激光产业发展报告》,2021年中国激光振镜行业市场规模约8.4亿元。目前国内振镜厂家在中低端的激光应用上占了大部分份额,但在高端应用领域,外国振镜品牌仍然牢牢的占据了主要份额。市场的参与者主要包括美国CTI、德国SCANLAB、Raylase等国外企业及大族思特、金海创、智博泰克、世纪桑尼、菲镭泰克等国内企业。国产扫描振镜在我国增材制造设备厂商中已经占据了一定的市场份额,未来有望实现国产化替代。
上游:原材料
全球和国内增材制造原材料处于快速增长阶段:根据Wohlers Associates数据,2022年全球增材制造材料产值 32.6 亿美元,同比增长了 25.5%(2021 年产值 25.98 亿美元)。其中聚合物粉末、丝材、光敏树脂、金属粉末分别占比37.9%、21%、21%、18.2%。根据中国增材制造产业联盟,2021年我国3D打印原材料产值14.7亿元,其中非金属占比63%,金属占比37%,金属原材料的产值高于世界平均水平。
增材制造原材料可以大致分为光敏树脂、高分子粉末、丝材、金属粉末等,其中光敏树脂和丝材主要用在消费级3D打印,高分子和金属主要用在工业级。金属材料包括钛合金、钴铬合金、不锈钢、铝合金材料等,其中钛合金具有强度高、耐蚀性好、耐热性高的特征,可以广泛应用于飞机发动机冷端压气机部件以及火箭、导弹和飞机的各种结构件制作。光敏树脂材料则主要用于制作高强度、耐高温、防水材料,应用于汽车、家电、电子消费品等领域。
3D打印的原材料种类有限,限制了部分场景的技术应用:区别于传统制造工艺的材料,3D打印使用的材料粉末有特殊性质要求,材料的含氧量、流动性、粒度等都有不同的要求。整体来看,由于材料的发展应用周期较长,在产业发展阶段一定程度限制了细分场景的落地和应用。
典型的增材制造厂商包括金属材料类:有研粉材(2021年产能500吨)、中航迈特(2021年产能800吨)、威拉里(2021年产能300吨)、宁波众远等,非金属材料类厂商:华曙高科(2022年产能500吨)、Polymaker(2022年产能数千吨-含消费级)、巴斯夫等。
上游:软件和扫描仪
2023年全球3D扫描仪的市场规模接近30亿美元,CAGR5=15%。海外厂商有先发优势,蔡司1970年之后就开始布局,目前齿科扫描等细分领域逐渐产生了国产替代的厂商:先临三维、思看科技等。
3D打印的软件功能涵盖拓扑优化、衍生式设计和算法建模、模型修复、模拟、切片和打印准备、打印管理和监督、MES 工具跟踪等,部分设备厂自研符合工艺流程的软件提升产品制造过程的各种性能。
中游:3D打印设备商
2021年全球工业级3D打印设备销量超过2.6万台,CAGR10=14%。其中装机量最多的国家依次为:美国、中国、日本。销量最多的公司分别为stratasys、Formlabs、3D Systems等。最主流的技术路线依次为:SLM/SLS(32%)、非金属中的FDM(15%)、SLA(15%)、DLP(14%),这几大技术路线共占据市场76%。2022年增材制造商的数量持续增加,相比于2021年一共增加20家(7.5%)。
对于国内设备厂商,2021年按照企业收入规模营收超过10亿的有面向消费级的创想三维、深圳众维等,营收2-10亿元的企业包括华曙高科、铂力特等16家企业,营收5000万-2个亿的约有60家企业,剩余还有100多家企业收入5000万以下。
中游:3D打印服务商
3D打印服务商提供预处理(即模型修复、构建方向、零件嵌套、构建准备等)、打印和后处理加工(即支撑材料去除、清洁、表面处理等)等功能,各个环节在整个打印服务中的成本占比如下:
过去十年,增材制造服务商的营收保持较高增速的增长,大部分年段服务商收入增速15%以上。
基于和行业内上百位从业者的交流,我们形成了系统化的增材制造投资逻辑。对于增材制造行业的投资布局主要关注三方面:公司层面,关注产业链定位、是否为行业头部以及创始团队的能力。技术层面,关注公司所选技术路线的壁垒强弱、技术成熟度、技术所切入场景的唯一性。商业化层面,关注切入场景的市场容量以及下游行业的需求和起量势能(见文尾)。除此之外的研究结论包括:
-
全球增材制造市场预计2030年达到近6000亿人民币,其中美国、中国、德国是主要的市场。中国增材制造市场2年内有望突破500亿,未来渗透率仍有较大提升空间。目前增材制造已经在航空航天、医疗、消费等领域得到客户的认可,未来在能源、工业模具制造等领域仍有较大发展空间,同时航空航天领域未来几年需求将保持旺盛。
-
产业链上游激光器、振镜等壁垒较高,国产化率逐步提升。原材料产值近几年处于快速增长阶段,同时材料的种类持续丰富和完善。中游设备类厂商持续迭代工艺技术,新的技术路线不断探索产业化能力和适用场景。打印服务商过去10年也保持了较高营收增速。
-
全球增材制造行业集中度不高,市场竞争逐渐激烈。领先的增材制造公司一直积极参与并购来扩张规模,其中既有单一设备制造商通过产业链整合,向系统解决方案提供商转变,也有大型用户企业直接布局增材制造领域。从海内外公司的发展情况来看,海外增材制造类上市公司2022年由于经济形势、零部件短缺、需求疲软等因素,市值普遍大幅下跌。2023年呈现明显回升趋势。国内增材制造类上市公司则最近几年营收均持续保持高速增长,市值也持续上升。
一、增材制造定义
增材制造是一种快速成型技术,通过创建数字模型将材料逐渐累加的方法来制造实体零件。增材制造的基本流程和原理如下:

图:增材制造基本流程
区别于减材制造通过切割材料毛坯来创建最终产品,增材制造通过添加零件来形成最终产品。
从原材料角度,增材制造需要采用特定原材料,材料成本往往更高,且可利用的原材料种类较少,但是原材料利用率更高;从制造工艺角度,增材制造更容易实现复杂零件的一次成型,且精度较高;从制造周期角度,增材制造设计验证的周期更短,效率更高;从制造成本角度,增材制造从低价格敏感度的航空航天和医疗领域逐渐向其他领域渗透。
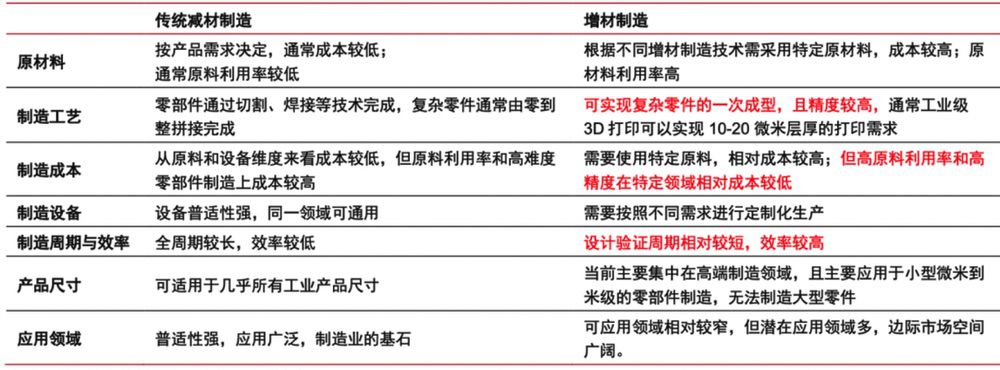
表:增材制造和传统制造模式的比较(来源:铂力特招股说明书、中信证券)
二、行业发展
20世纪60年代和70年代,增材技术技术处于起步阶段,几乎完全没有商业市场,对研发的投入也很少。研究工作验证了第一批现代AM工艺,包括20世纪60年代末的光聚合技术,1972年的粉末熔融工艺,以及1979年的薄片叠层技术。
20世纪80年代和90年代初,出现了很多创新的AM技术,同时一部分增材技术被成功商业化。创新型的技术包括1989年麻省理工学院的3D打印技术,与90年代的激光束熔化工艺。成功商业化的增材制造技术包括光固化(SLA)技术、固体熔融沉积技术(FDM),以及激光烧结技术(SLS)等。增材制造相关专利和学术出版物的数量明显增多,但是受限于高成本和有限的材料选择,尺寸限制以及有限的精度,增材制造技术在工业上的发展比较缓慢,只能用于小量快速原型件或模型的制作。1986年全球第一家3D打印企业3D systems成立标志着3D打印进入产业化。
20世纪90年代和2000年代是增材制造行业的增长期。现有技术逐步得到提升和改进,同时新技术逐渐实现了商业化。产业逐渐开始开发专门应用于增材制造行业的软件。出现了AM的专用文件格式,AM的专用软件,如Materialise的Magics开发完成。设备的改进和工艺的开发使3D增材制造产品的质量得到了很大提高,开始被用于工具甚至最终零件。
2009年之后,随着欧美3D打印的底层专利在2009-2015年陆续到期,我国的增材制造开始进入发展的快车道。
2011年到2020年,增材制造的产业化进程不断推进,行业市场规模保持高速增长,海内外3D systems、stratasys、铂力特等公司不断上市,同时GE、佳能、东芝等企业纷纷涉足增材制造市场,在航空航天等多个领域持续落地增材制造应用。
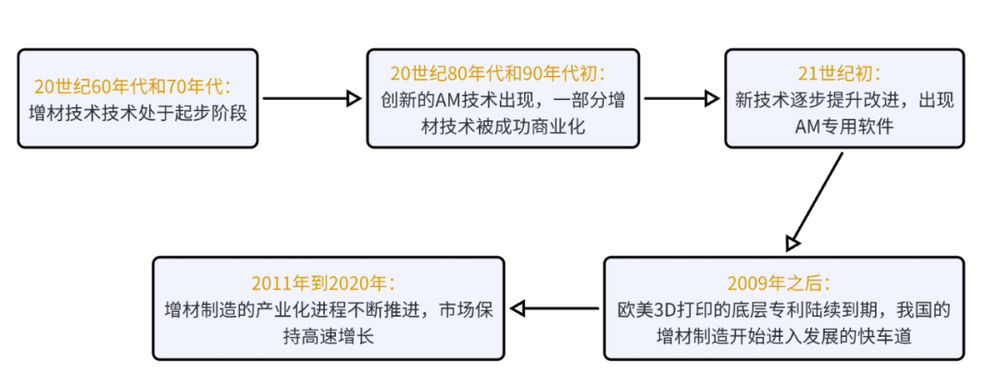
图:增材制造产业发展
未来,随着产业化的进程不断推进,行业技术的成熟度也将逐渐提高,值得关注的未来技术包括激光器、DfAM等。
激光器发展有助于显著提升打印效率
激光器效率的提升受到业界普遍关注。目前全球各家公司均在尝试不同的激光器效率突破技术路线,其中VulcanForms Inc. 发明了 100 千瓦激光 PBF 技术并将其商业化并集成到专有的数字制作系统中。Seurat Technologies 发明了一种激光 PBF 技术,该技术使用燼一种光学可寻址光阀技术来支持该公司所谓的区域印刷。该公司声称该过程比传统激光 PBF 技术快 10 倍。另一个发展是激光束热分布的优化。这样可以更精确地控制热沉积,从而最大限度地提高构建速度,提高材料质量,并最大限度地减少飞溅和烟雾。此外,初创公司 SunMetalon 也在筹集资金通过层而不是点或线的方式来加热金属,从而进一步提高金属 AM 的速度。
DfAM方法可以有效提升产品性能
DfAM指的是面向增材制造的设计,即结构设计工程师利用增材独特的工艺优势去构建产品的设计过程。在产品设计制造之初同时考虑到设计、增材工艺、增材产品认证方法、增材制造生产模式与产能等众多因素。
通过DfAM 技术对设计环节能力的提升,可以优化打印过程中和打印后处理的工艺水平,DfAM 的方法可以提高产品性能并减少材料和重量,降低制造和组装的复杂性。目前Conflux 和 GKNAdditive 等公司正在使用 DfAM 的方法开发的高效热交换器。下图显示了DfAM对于增材制造不同环节的影响:
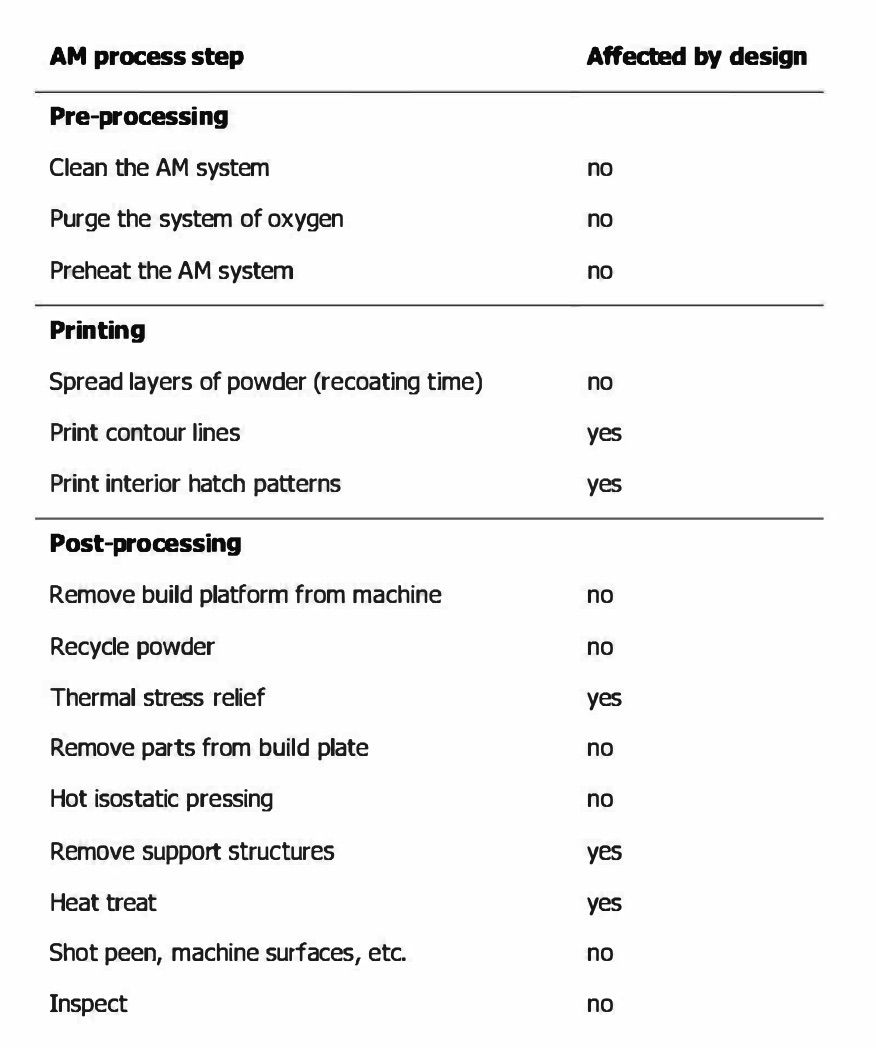
表:增材制造智能设计对不同环节的成本影响
三、技术路线增材制造可以大致分成金属类增材制造和非金属类增材制造。整体分类概览如下图:
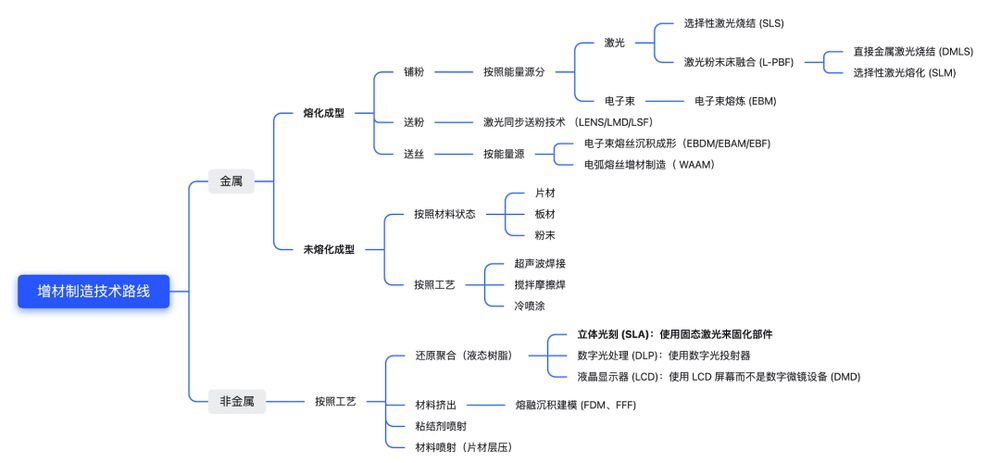
图:增材制造不同技术路线分类
1、金属增材制造
金属增材制造可以分为熔化成型和未熔化成型两类,相关的工艺有铺粉、送粉、送丝等,能量源分为激光、电子束、电弧等。其中未熔化成型不做重点介绍,该技术按照材料状态分片材、板材、粉末;按照工艺超声波焊接、搅拌摩擦焊、冷喷涂等。
熔化成型主要包括粉末床熔化(PBF)和直接能量沉积(DED)两大类。在市场份额层面,根据 AMPOWER,以营收计算,2021 年 PBF、DED 各占据 83.8%和 9.1%的市场份额。且预计到 2026 年,PBF、DED 将各占据 74%和 8.6%的市场份额。
1.1粉末床熔化(PBF)
PBF是一种铺粉工艺的增材制造技术,PBF按照不同的能量源可以分为激光熔化和电子束熔化。
其中选择性激光烧结 (SLS)、选择性激光熔化 (SLM)能量源都是激光。SLM的成型原理与SLS极为相似,不同点在于SLM的激光温度较高,会在成型过程中完全熔化所有金属粉末。因此SLM整个打印过程需要在惰性气体保护的腔体中进行,以避免金属发生氧化。这给SLM带来了更好的成型性能,相比SLS制造的金属零件的致密度更高,力学性能更好,尺寸精度更高、表面粗糙度也更高。但是SLM工艺参数复杂、制造速度偏低,尤其是面对需要大量支撑结构的复杂零件,SLM的打印成本、时长会明显提高。
适合应用于载人飞船引擎的冷却道、喷射头、节流阀等结构复杂程度非常高的结构上面。(注:SLS技术既可以应用于金属,也可以用于非金属)
电子束熔炼 (EBM)的能量源为电子束。相比于激光路线,EBM 精度略低但速度高:SLM 沉积速率通常在 0.1kg/h, 而 EBM 速度可达数倍。EBM相比于SLM在几乎所有步骤里都存在很明显的成本优势:特别是在设备运行、热处理与支撑拆除方面。此外,相比于 SLM,EBM 无需后加工处理残余应力。且EBM 的支撑能够很轻易的移除,因此其拆除成本很低。
1.2直接能量沉积(DED)
DED整体的打印效率高于PBF,但是精度逊于 PBF。按照材料状态分送粉式和送丝式,能量源包括激光、电子束、电弧等。
-
激光同步送粉技术 (LENS/LMD/LSF):DED 中研究和应用最广泛的技术,能够实现梯度材料、复杂曲面修复,在大型器件的修复上正不断地发挥作用。
-
电子束熔丝沉积成形(EBDM/EBAM/EBF):在沉积速率方面拥有绝对优势:EBAM 沉积速率达到了 18.2kg/h,比基于激光的 DED 技术路线高出了 1 个数量级,超过 PBF 技术路线 2 个数量级
-
电弧熔丝增材制造(
WAAM):WAAM技术主打大尺寸高效率,每小时沉积效率可达数十公斤,极大降低制造成本。由于不需要气氛保护箱和真空箱等设备,工件尺寸不受其空间尺寸的限制,也大幅减少对设备的投资成本。此外,WAAM可成形的材料种类广泛,适合成形对激光反射率高的材质(如铝合金、铜合金)。WAAM本质上与工艺焊接非常接近,因此会出现裂纹、孔隙、飞溅等情况。此外零件表面精度较低,需后加工以控制精度。应用领域包括:需要进一步后加工的零件成型(近净成型)、在已有结构件上自由打印特定结构;生产拓扑优化构件;高价值零部件维修等。
此外,金属增材制造技术中经历高能量输入的增材制造工艺需要后处理,后处理操作通常包括粉末清理、支撑去除、构建板分离、机加工、清洁、抛光或表面增强以及焊接等连接方式。将零件和构建板分离之前,通常需要消除应力,确保残余应力不会导致零件变形。不同工艺的去支撑、去应力、热处理等需求汇总如下:
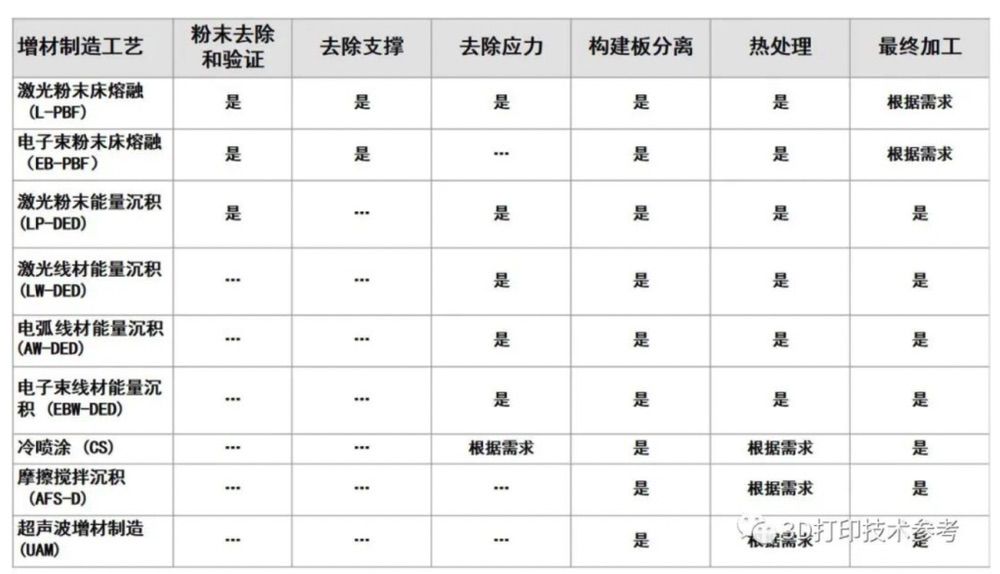
图:不同增材制造工业的后处理(来源:3D打印技术参考)
2、非金属增材制造2.1还原聚合
聚合还原是一种树脂3d打印技术,工艺过程为光线精确地指向液体塑料的特定点或区域以使其硬化。第一层固化后,构建平台将向上或向下移动(取决于打印机)少量(通常在 0.01 和 0.05 毫米之间),下一层固化并与前一层连接。聚合还原按照不同光源可以分为SLA、DLP、LCD等。
立体光刻 (SLA)使用固态激光来固化部件,是目前世界上研究最为深入、技术最为成熟、应用最为广泛的一种3D打印技术。该技术的优点是尺寸精度高、表面质量优良、系统分辨率较高,可以制作结构比较复杂的模型或零件。缺点包括零件较易弯曲和变形、设备运转及维护成本较高、材料不利于长时间保存等。
数字光处理 (DLP)使用数字光投射器(而不是激光)在一层或树脂上同时闪烁每一层的单个图像(或为较大的部件多次曝光)。每一层曝光都需要完全相同的时间,比SLA 中的点激光方法效率更高。用于生产更大的零件或更大体积的零件。
液晶显示器 (LCD)使用 LCD 屏幕而不是数字微镜设备 (DMD),也就是使用数百个单独发射器的阵列,而不是像激光二极管或 DLP 灯泡那样的单点发射光源。LCD 单元成本低,这项技术已成为低价桌面树脂打印机领域的首选技术。常见应用包括注塑模状聚合物原型和最终用途部件、珠宝铸造、牙科应用、消费品。
2.2材料挤出
熔融沉积建模 (FDM、FFF)是典型的材料挤出工艺,该工艺过程为将线轴上的一根(或一次几根)灯丝装入 3D 打印机,然后送入挤出头中的打印机喷嘴。打印机喷嘴或多个喷嘴被加热到所需温度,使灯丝软化,从而使连续的层连接起来形成一个坚固的部件。材料挤出是成本较低的 3D 打印方法,无需激光器等贵重原件,成本低、速度快。且该工艺干净、简单、易于操作且不产生垃圾。对使用环境没有限制,可以放在办公室或者家庭环境使用,维护简单、体积小无污染 。但是材料挤出的成型精度相对SLA工艺较低,成型表面光洁度不如SLA工艺。
3、其他增材制造技术
其他增材制造技术包括材料喷射、粘结剂喷射、片材层压等,这些技术既可以应用于金属,也可以应用于非金属。
3.1粘结剂喷射
粘结剂喷射的工艺过程是用重涂刀片在构建平台上涂抹一层薄薄的粉末。然后,带有喷墨喷嘴的打印头在床上方经过,选择性地沉积粘合剂液滴以将粉末颗粒粘合在一起。层完成后,构建平台向下移动,刀片重新涂覆表面。然后重复该过程,直到整个部分完成。该技术的独特之处在于打印过程中没有热量。粘合剂喷射速度快且生产率高。但是聚合物粘合剂喷射的材料选择有限,并且生产的部件结构性能较低。
3.2片材层压
片材层压的工艺过程为将非常薄的材料片堆叠和层压在一起以产生 3D 物体或堆叠,然后通过机械或激光切割以形成最终形状。材料层可以使用多种方法融合在一起,包括加热和声音,具体取决于材料,材料范围从纸张、聚合物到金属。具体包括层压物体制造 (LOM)、超声波固结 (UC)等,相关材料有纸张、聚合物和片状金属等。该技术的优点是可以快速生产,复合打印。缺点为精度低,浪费多,部分零件需要后期制作。抗拉强度和弹性差,不能制造中空件;受制于材料影响,利用 LOM 技术打印的零件易吸湿膨胀,表面有台阶纹。
3.3材料喷射
材料喷射将材料沉积到构建表面上,然后使用紫外光固化或硬化该层。逐层重复,直到对象完成。由于材料以液滴形式沉积,因此材料仅限于光敏聚合物、金属或蜡,它们在暴露于紫外线或高温时会固化或硬化。材料喷射过程需要支撑结构,通常也是在构建过程中同时使用可溶解材料来进行3D打印,然后在后处理步骤中去除支撑材料。该技术可以提供出色的细节、高精度和光滑的表面。使用材料喷射技术进行打印的主要缺点是成本高,并且紫外线活化的光敏聚合物会随着时间的推移失去力学性能并且会变脆。
不同增材制造技术的在成型尺寸、粘结性能、工作环境等方面各有差异,详细的技术比较如下图:
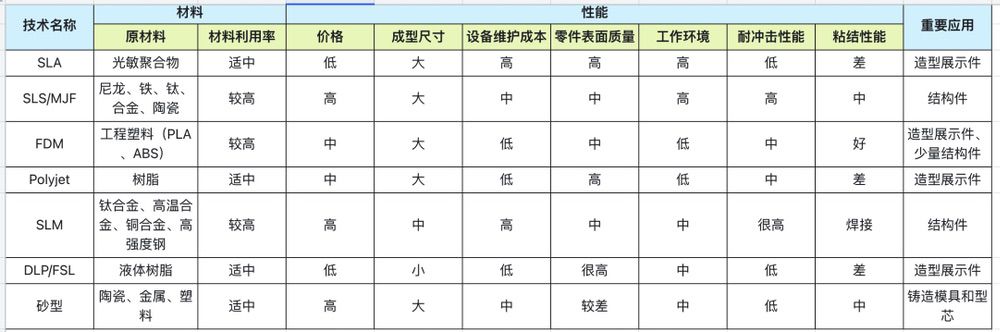
图:各类增材制造技术的性能比较
同时,各类技术路线的产业化进程也有所不同,具体进展如下:
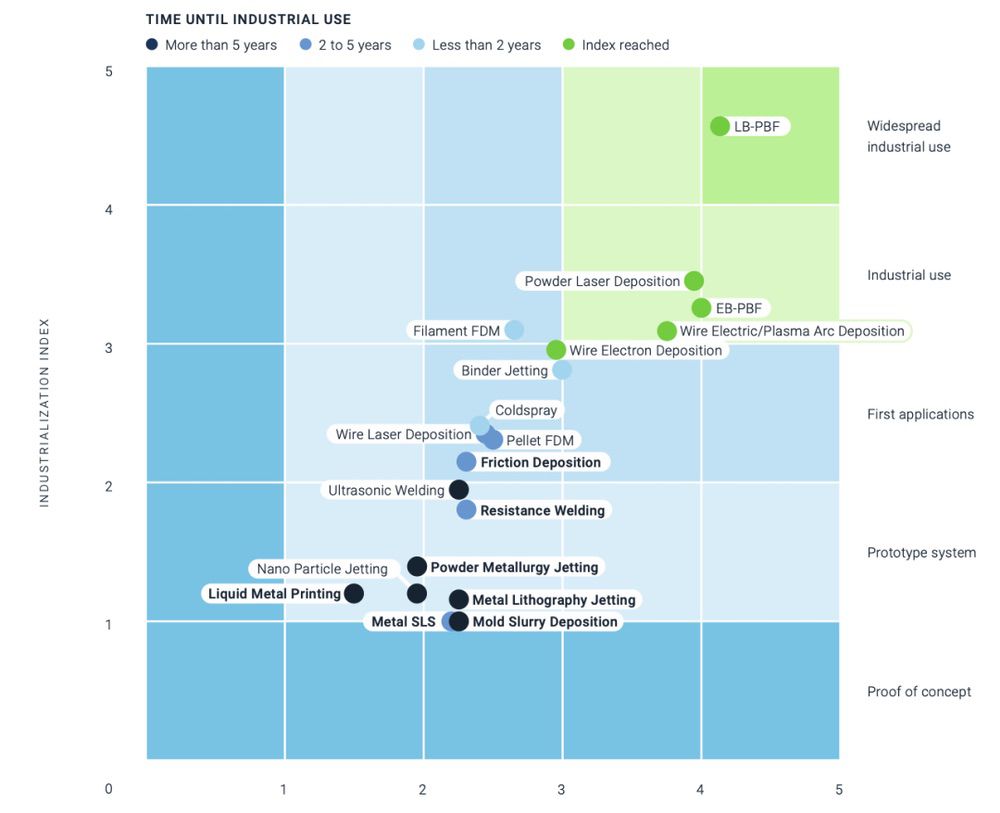
图:不同增材制造技术的成熟度(来源:AMpower)
四、市场规模和集中度全球增材制造市场空间广阔,未来仍保持高速增长:根据Wohlers Associates数据,2022年全球增材制造全球市场规模180.27亿美金,过去34年的复合增长率达到25.6%,预计2030年市场规模达到853亿美金(近6000亿人民币)。
中国增材制造市场短期有望突破500亿,渗透率仍有较大提升空间:根据中国增材制造产业联盟,2022年我国3D打印市场规模330亿,2018-2022年的复合增长率为28%。根据赛迪咨询数据,2024年中国的3D打印市场规模有望进一步提升,突破500亿元。目前增材制造在制造业渗透率不足0.1%,处于产业化的前期,长期制造业渗透率3-5%。
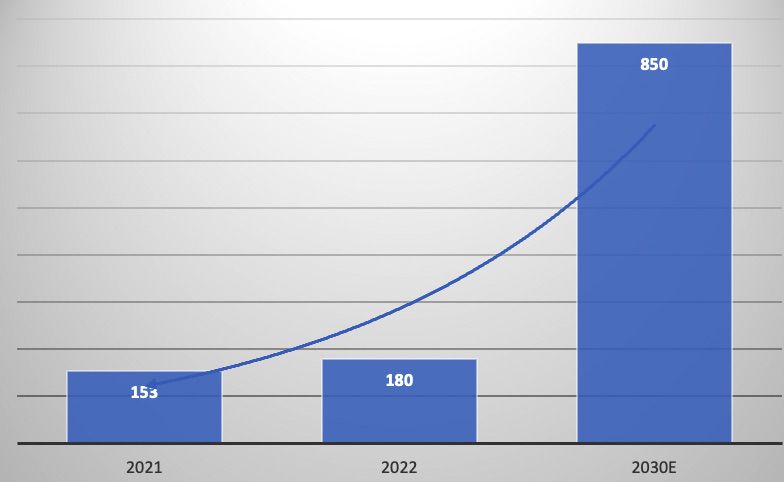
图:全球增材制造市场规模 单位:美金(来源:Wohlers Associates)
中国增材制造市场规模在全球领先:Wohlers Associates 的研究表明,我国工业级增材制造设备安装量全球领先。在全球安装的所有工业增材制造 (AM) 系统中有 34.9%在北美,28.4% 安装在亚太地区,30.7% 在欧洲。按照国家来看,美国、中国、德国是工业级增材制造设备安装量最多的三个国家。
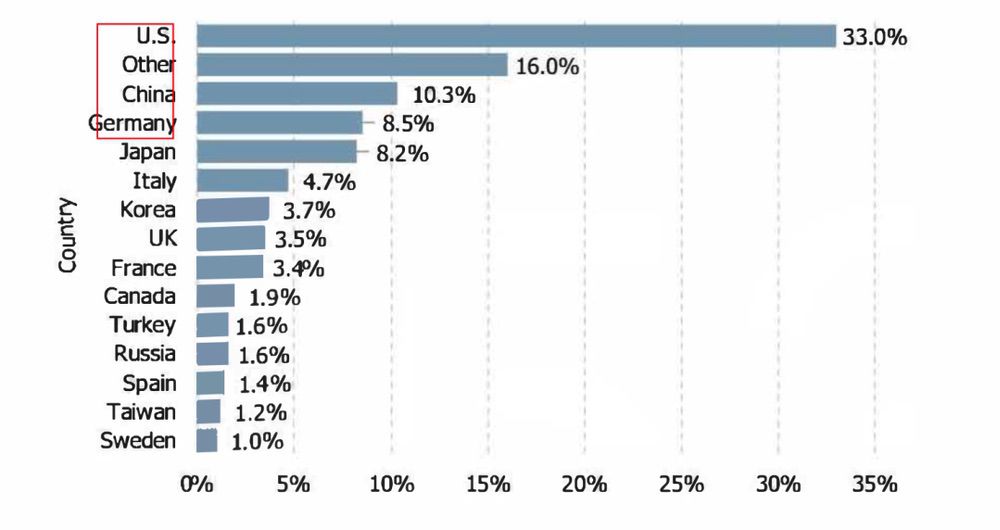
图:增材制造工业设备出货量情况
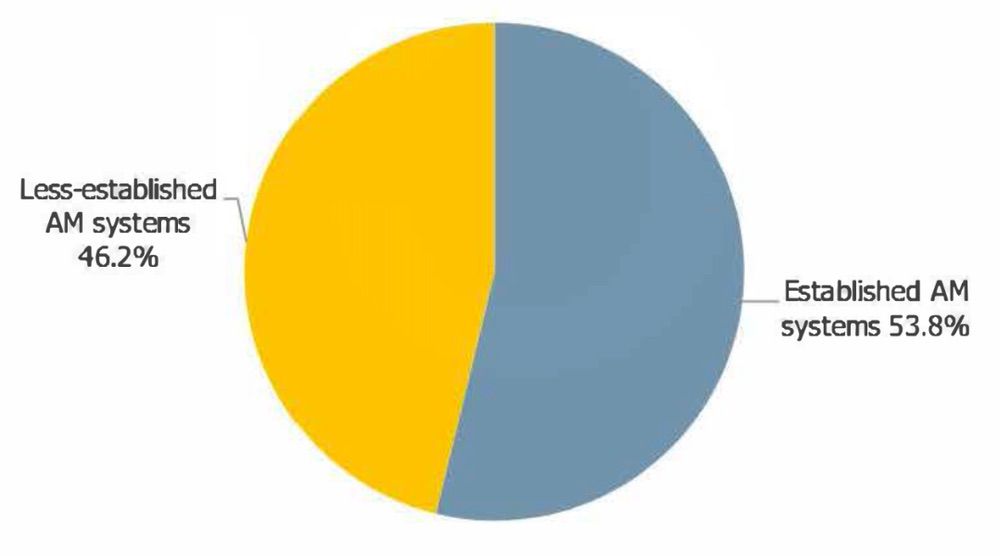
图:知名和非知名品牌的出货占比
增材制造行业集中度不高,市场竞争逐渐激烈:根据Wohlers Associates 研究,2022 年前 10 家最大的系统制造商贡献了整个增材制造行业约 27.21 亿美金的产值,占比15.1%。非品牌厂商的市占率呈现逐年提升趋势:服务供应商以前基本从 3D Systems、EOS 和 Stratasys 等成熟的 AM 制造商处购买系统。然而,2022 年服务供应商购买的 290 台机器中,包括了156 台非成熟制造供应商的 AM 系统(占比53.8%),连续第三年从非成熟公司购买设备呈现增长趋势。
五、产业链
3D打印上游包括材料类、核心硬件、辅助设备等。其中材料包括金属材料和非金属材料。核心硬件类涵盖激光器、振镜系统和引擎,辅助设备包括3D建模软件、扫描仪等。3D打印的中游包括3D打印设备制造商和服务商,按照材料性能分为金属类和非金属类。下游面向的应用领域包括航空航天、医疗、模具等。
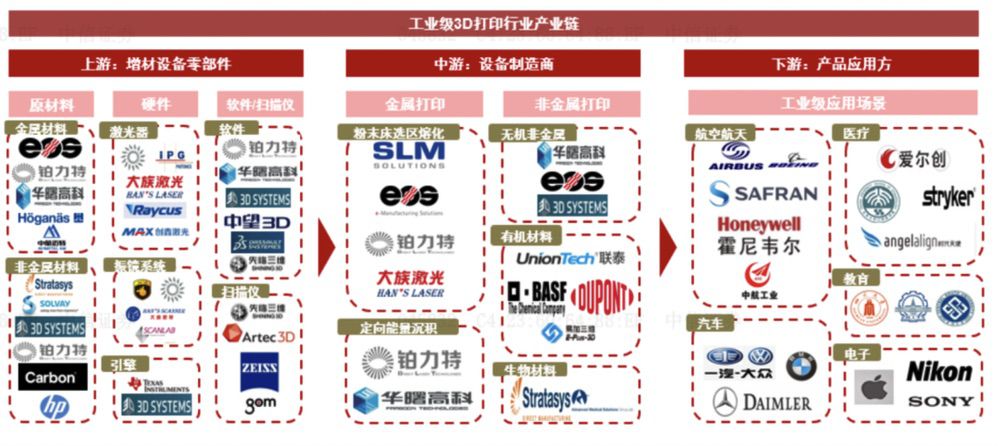
图:增材制造产业链及相关公司(来源:中信证券)
上游:激光器、振镜
激光器是增材制造产业链上游的核心硬件,可以分为光纤激光器、CO2激光器等。
激光器的国产化比例不断提升:根据 Laser Focus World 数据,2020 年中国光纤激光器市场规模约为 13.8 亿美元,其中国产比例约 56%,达 7.73 亿美元。美国的光纤激光器制造商 IPG 占据了中国光纤激光器市场的最大份额(2019年42%),但是总体市场销售份额明显下降。国产品牌占比显著上升,包括来自中国的锐科激光、创鑫激光和杰普特等企业。增材制造所使用的激光器功率普遍较低,此类中低功率的光纤激光器基本完成了国产化进程。
振镜类也是增材制造上游的零部件,据《2021年中国激光产业发展报告》,2021年中国激光振镜行业市场规模约8.4亿元。目前国内振镜厂家在中低端的激光应用上占了大部分份额,但在高端应用领域,外国振镜品牌仍然牢牢的占据了主要份额。市场的参与者主要包括美国CTI、德国SCANLAB、Raylase等国外企业及大族思特、金海创、智博泰克、世纪桑尼、菲镭泰克等国内企业。国产扫描振镜在我国增材制造设备厂商中已经占据了一定的市场份额,未来有望实现国产化替代。
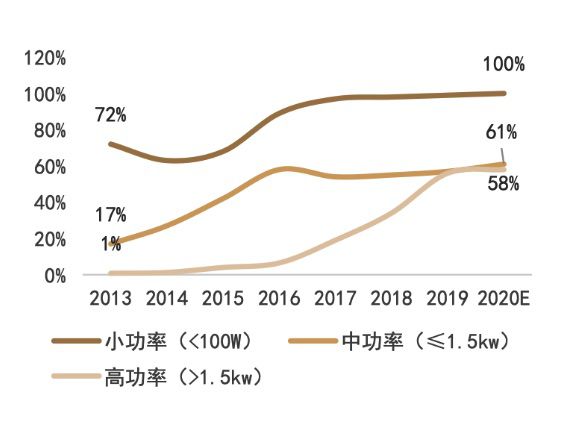
图:中国光纤激光器国产化率
(来源:2020年中国激光产业发展报告)
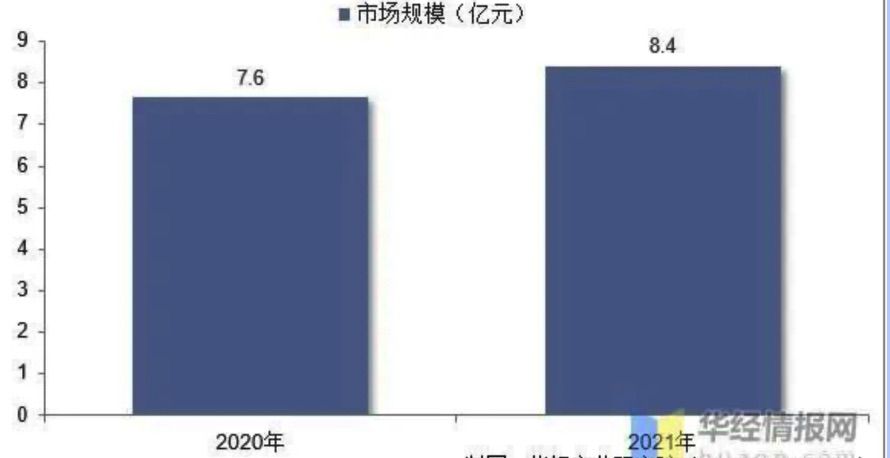
图:中国激光振镜市场规模(来源:华经产业研究院)
上游:原材料
全球和国内增材制造原材料处于快速增长阶段:根据Wohlers Associates数据,2022年全球增材制造材料产值 32.6 亿美元,同比增长了 25.5%(2021 年产值 25.98 亿美元)。其中聚合物粉末、丝材、光敏树脂、金属粉末分别占比37.9%、21%、21%、18.2%。根据中国增材制造产业联盟,2021年我国3D打印原材料产值14.7亿元,其中非金属占比63%,金属占比37%,金属原材料的产值高于世界平均水平。
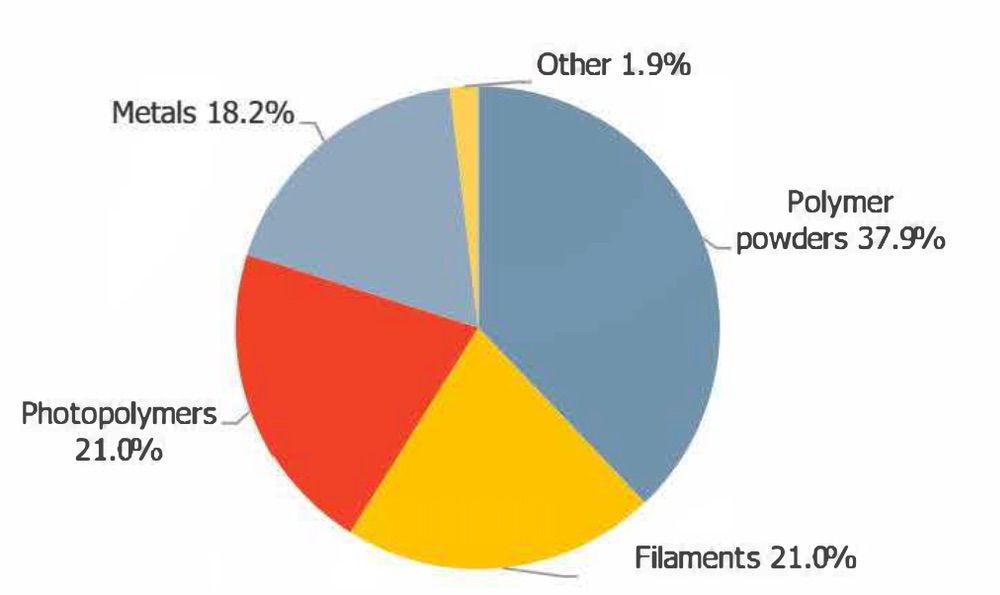
图:全球增材制造原材料产值(来源:Wohlers Associates)
增材制造原材料可以大致分为光敏树脂、高分子粉末、丝材、金属粉末等,其中光敏树脂和丝材主要用在消费级3D打印,高分子和金属主要用在工业级。金属材料包括钛合金、钴铬合金、不锈钢、铝合金材料等,其中钛合金具有强度高、耐蚀性好、耐热性高的特征,可以广泛应用于飞机发动机冷端压气机部件以及火箭、导弹和飞机的各种结构件制作。光敏树脂材料则主要用于制作高强度、耐高温、防水材料,应用于汽车、家电、电子消费品等领域。
3D打印的原材料种类有限,限制了部分场景的技术应用:区别于传统制造工艺的材料,3D打印使用的材料粉末有特殊性质要求,材料的含氧量、流动性、粒度等都有不同的要求。整体来看,由于材料的发展应用周期较长,在产业发展阶段一定程度限制了细分场景的落地和应用。
典型的增材制造厂商包括金属材料类:有研粉材(2021年产能500吨)、中航迈特(2021年产能800吨)、威拉里(2021年产能300吨)、宁波众远等,非金属材料类厂商:华曙高科(2022年产能500吨)、Polymaker(2022年产能数千吨-含消费级)、巴斯夫等。
上游:软件和扫描仪
2023年全球3D扫描仪的市场规模接近30亿美元,CAGR5=15%。海外厂商有先发优势,蔡司1970年之后就开始布局,目前齿科扫描等细分领域逐渐产生了国产替代的厂商:先临三维、思看科技等。
3D打印的软件功能涵盖拓扑优化、衍生式设计和算法建模、模型修复、模拟、切片和打印准备、打印管理和监督、MES 工具跟踪等,部分设备厂自研符合工艺流程的软件提升产品制造过程的各种性能。
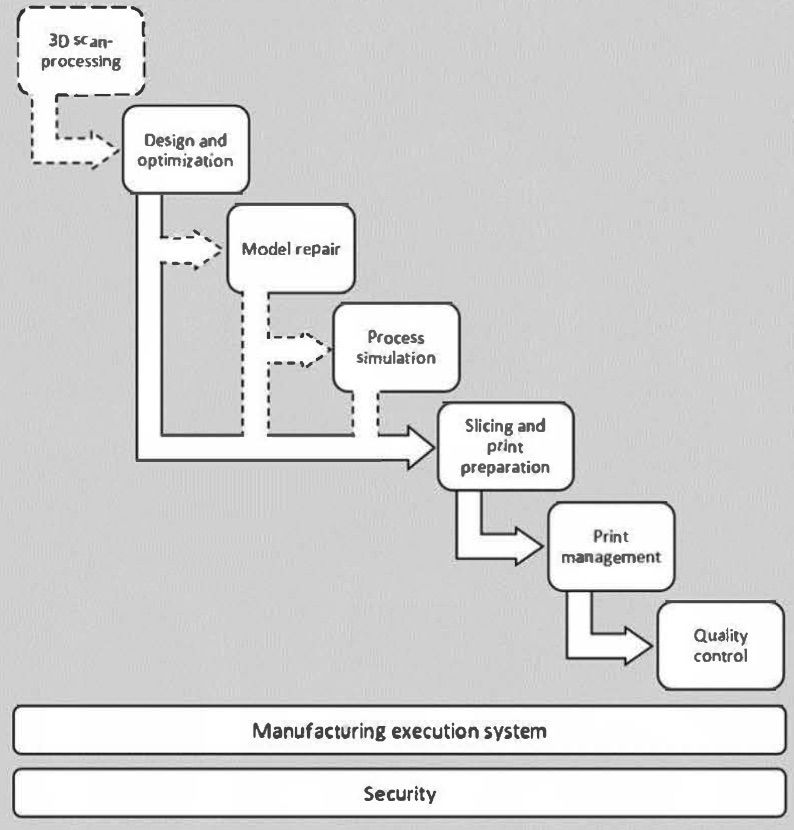
图:AM软件流程和功能(来源:Wohlers Associates)
中游:3D打印设备商
2021年全球工业级3D打印设备销量超过2.6万台,CAGR10=14%。其中装机量最多的国家依次为:美国、中国、日本。销量最多的公司分别为stratasys、Formlabs、3D Systems等。最主流的技术路线依次为:SLM/SLS(32%)、非金属中的FDM(15%)、SLA(15%)、DLP(14%),这几大技术路线共占据市场76%。2022年增材制造商的数量持续增加,相比于2021年一共增加20家(7.5%)。
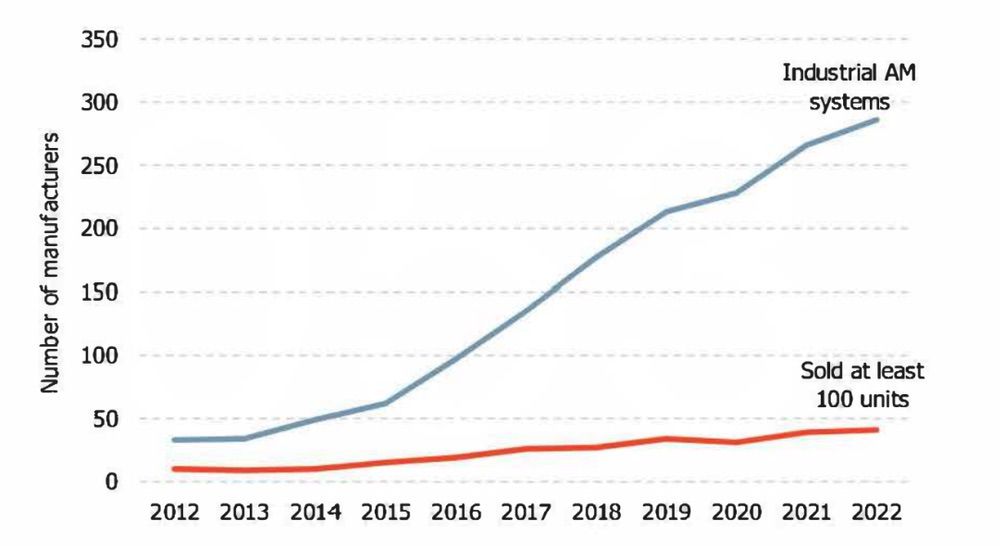
图:全球工业级增材制造商数量(来源:Wohlers Associates)
对于国内设备厂商,2021年按照企业收入规模营收超过10亿的有面向消费级的创想三维、深圳众维等,营收2-10亿元的企业包括华曙高科、铂力特等16家企业,营收5000万-2个亿的约有60家企业,剩余还有100多家企业收入5000万以下。
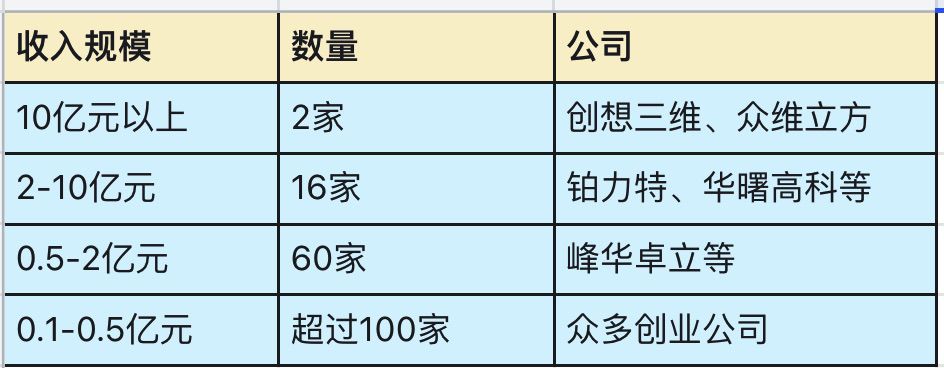
图:中国3D打印厂商收入情况(来源:南极熊)
中游:3D打印服务商
3D打印服务商提供预处理(即模型修复、构建方向、零件嵌套、构建准备等)、打印和后处理加工(即支撑材料去除、清洁、表面处理等)等功能,各个环节在整个打印服务中的成本占比如下:
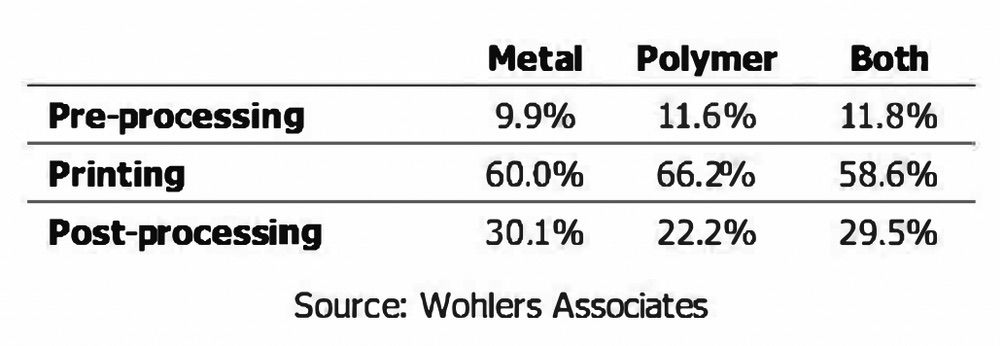
图:不同环节在整个打印服务中的成本占比(来源:Wohlers Associates)
过去十年,增材制造服务商的营收保持较高增速的增长,大部分年段服务商收入增速15%以上。
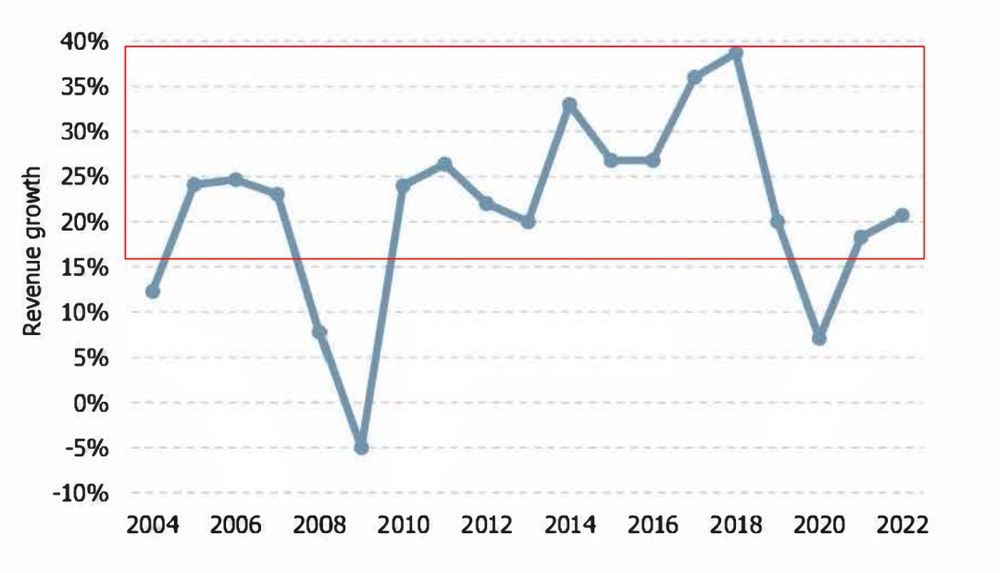
图:3D打印服务商收入增速(来源:Wohlers Associates)
(责任编辑:admin)
最新内容
热点内容