增材制造高熵合金的组织结构和性能
高熵合金因其优异的力学性能、耐腐蚀性和热稳定性,成为近年来材料科学领域的研究热点。然而,传统制备工艺面临的成分均匀性不足、高裂纹敏感性和高成本等问题限制了其工业应用。增材制造技术以其逐层制造、高设计自由度和快速冷却的优势,为高熵合金的复杂结构制备提供了新的解决方案。本文论述了增材制造技术在高熵合金领域的最新研究进展,重点分析了选择性激光熔化、直接能量沉积、电子束熔化等技术在组织调控和性能优化中的应用。研究发现,不同技术在组织控制、性能提升及适用领域方面各具优势,同时也面临裂纹形成、成分偏析和残余应力等共性挑战。通过深入分析工艺的优化策略及其对性能的影响,揭示了增材制造高熵合金组织与性能的内在关联,并提出了未来的发展方向,包括开发新型合金体系、优化工艺参数、提高制造效率以及拓展多功能材料应用。
高熵合金(High-entropy alloys,HEAs)是一种由多种近等摩尔比金属元素组成的新型合金体系,其高混合熵(配置熵)影响了相的形成,使得高熵合金倾向于形成简单固溶体结构(如BCC、FCC、HCP),而非易碎的金属间化合物。这种独特的组织结构使高熵合金在力学、化学和热学性能上表现出优异的综合性能,从而被广泛认为是航空航天、能源和海洋工程等领域的理想材料。同时,高熵合金的近等摩尔比提供了广阔的成分设计空间,可根据实际需求优化合金性能。然而,传统制备工艺(如铸造和锻造)通常导致材料成分不均匀、微观结构难以控制,并伴随高生产成本,限制了高熵合金的工业化应用,这一现状对高熵合金的高效制备技术提出了迫切需求。
增材制造技术(Additive manufacturing,AM)近年来在制备高熵合金领域得到了广泛关注。作为一种基于计算机辅助设计(CAD)的现代制造工艺,增材制造技术利用金属粉末或线材,通过逐层堆积的方式构建三维结构,不仅展现了极高的设计自由度,还通过快速冷却过程优化了材料的微观组织。与传统制造工艺相比,增材制造能够直接成形复杂零件,已在航空航天、医疗器械和汽车制造等领域得到了广泛应用。在多种增材制造技术中,选择性激光熔化(Selective laser melting,SLM)作为一种基于粉末床的熔化工艺,因其产品具有高精度和良好的表面质量成为研究热点。选择性激光熔化工艺中的高温梯度和快速冷却有助于形成高饱和度的固溶体结构,对优化高熵合金的微观组织和性能具有显著优势。然而,选择性激光熔化技术仍面临裂纹形成、成分均匀性控制和微观组织调控等技术挑战。
现有文献综述聚焦于特定增材制造技术的基础研究,未能系统讨论实验室研究成果在实践中的意义。因此,本文结合增材制造领域的最新进展和实验室实践,系统分析了选择性激光熔化(SLM)、电子束熔化(Electron beam melting,EBM)、直接能量沉积(Directed energy deposition,DED)等技术在高熵合金制备中的应用优势与挑战。重点探讨增材制造在优化微观组织、提升力学性能及开发新功能特性(如耐腐蚀性、氧化行为、磁性和储氢性能)方面的作用,并分析当前技术瓶颈及未来发展方向,为后续研究提供理论支持和技术参考。
高熵合金基础概述
高熵合金(High-entropy alloys,HEAs)是一类由至少5种、最多13种近等摩尔比金属元素组成的新型合金体系。为了扩大合金设计范围,每种主元素的摩尔分数通常介于5%~35%,且摩尔比相近。高熵合金因其独特的组成特性和多样化的相结构,在力学、化学和热学性能方面表现出显著优势。
高熵合金的性能和结构特性主要源自其4个核心效应:(1)热力学高熵效应;(2)结构晶格畸变效应;(3)动力学缓慢扩散效应;(4)“鸡尾酒”效应。这些效应总结了高熵合金在相形成与性能上的基本规律。高熵效应通过降低金属间化合物的形成倾向,促进了面心立方(FCC)、体心立方(BCC)或六方密堆积(HCP)等简单固溶体相的稳定性,抑制复杂相的析出,从而使合金趋于形成均匀的单一相。
在高熵合金中,近等摩尔比和多元素特性显著影响原子扩散行为和晶格特性。由于不存在传统合金中溶质、溶剂的区分,高熵合金中的原子主要通过空位机制扩散。但不同元素的原子半径差异会引发晶格畸变,导致不同晶格位置的势能变化较大,阻碍了原子扩散速率。这种缓慢的扩散行为有助于稳定单一固溶体相,并使高熵合金在快速冷却工艺(如选择性激光熔化)中表现出优异的热力学稳定性。同时,晶格畸变导致不同的相结构具有不同的力学性能:FCC相具有较高的原子密堆积率,晶格畸变较小,具有良好的延展性和韧性;BCC相虽然原子密堆积率较低,但晶格畸变较大,使其具有较高的强度和硬度;HCP结构则以高密度的原子排列和较少的滑移面表现出优异的抗腐蚀性和耐高温性能。在某些条件下,高熵合金还可能同时存在FCC和BCC双相结构,通过优化成分设计和工艺参数,实现强度与韧性的平衡。
相结构的调控是提升高熵合金综合性能的关键。通过调整成分设计、制造工艺及冷却条件,可以精确控制相结构的形成与稳定性。然而,传统制造工艺在制造均质高熵合金方面存在较大局限性,如存在成分不均匀和相分离问题。相比之下,增材制造技术因其优异的微观组织调控能力和设计自由度,为高熵合金的工业应用提供了广阔的可能性。
增材制造技术在高熵合金制备中的应用
增材制造技术已成为制备高熵合金的重要工艺,其核心在于通过逐层沉积原料构建复杂结构,展现了高设计自由度和高材料利用率的优势。以下将从技术简介与工作原理、对高熵合金组织调控的作用、以及各技术的适用范围和优缺点3个层次展开讨论。
2.1 增材制造技术简介
目前,应用于金属材料的增材制造技术主要包括选择性激光熔化(SLM)、直接能量沉积(DED)、激光熔化沉积(LMD)、电子束熔化(EBM)以及线弧增材制造(WAAM)等。表1所示为各增材制造技术的基本信息,图1所示为对应的工作原理示意图。这些技术为高熵合金的制备提供了多样化的工艺路径,不同工艺的特点决定了其在组织调控与性能优化方面的应用潜力。
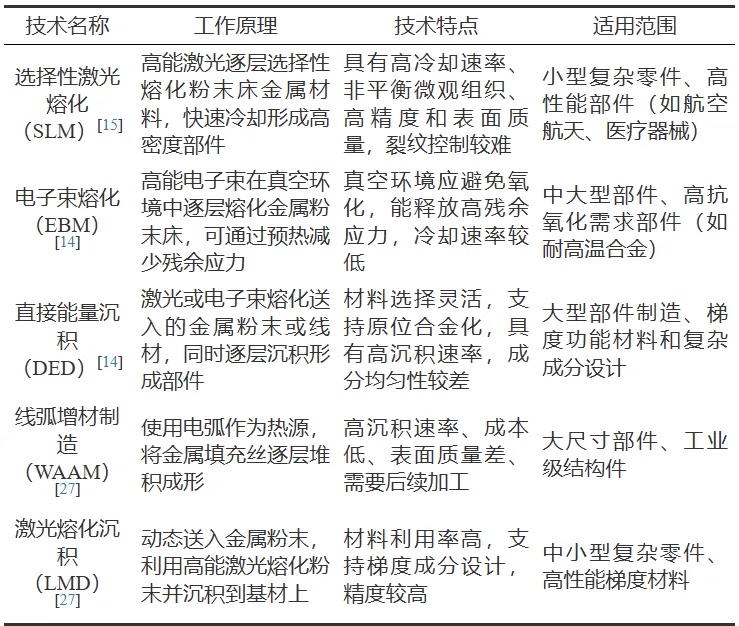
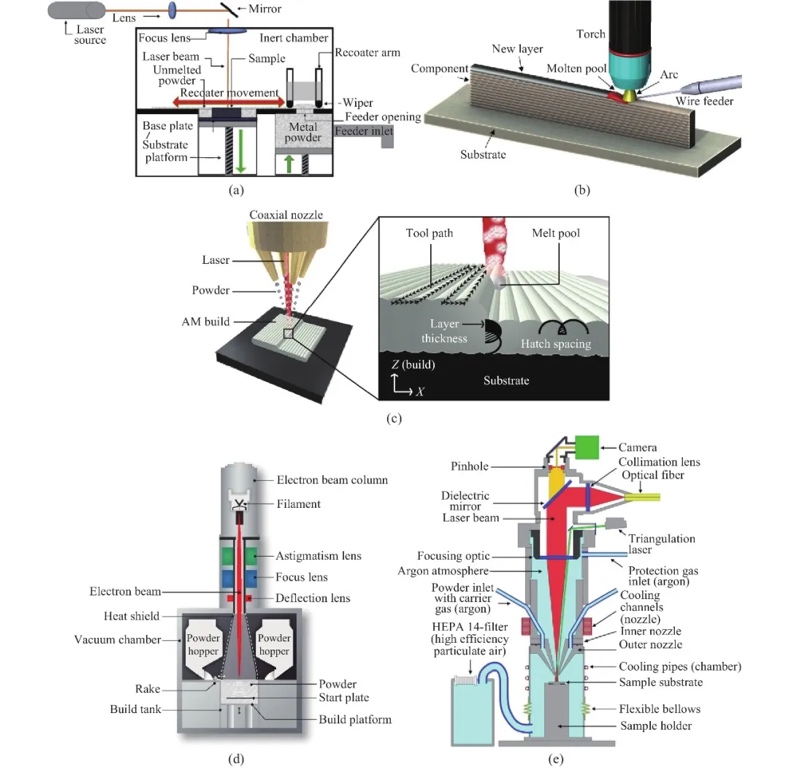
2.2 增材制造技术对高熵合金组织调控的作用
增材制造技术通过其独特的快速冷却和高能量密度工艺,对高熵合金的微观组织调控展现出显著优势。相较于传统制造方法,增材制造技术可以在制造过程中通过直接影响晶粒形态、织构取向、位错分布和沉淀析出,从而调控高熵合金的组织结构和性能特性。
2.2.1 晶粒形态与细化
增材制造工艺中,通过快速冷却(103~106 K/s)抑制了晶粒的长大趋势,使得选择性激光熔化和直接能量沉积等技术制备的高熵合金呈现细小的柱状晶或胞状亚结构。这种微观组织在提升材料强度和硬度的同时,也显著改善了材料的塑性。快速冷却还能够稳定非平衡组织,如纳米孪晶和非晶态结构,这在传统制备工艺中较难实现。
2.2.2 相结构稳定与控制
高熵合金的相结构(FCC、BCC或HCP)对其性能影响显著。增材制造技术通过高冷却速率实现过饱和固溶体的形成,减少不需要的金属间化合物析出,同时通过调节激光功率、扫描策略和预热条件实现双相组织(FCC+BCC)的精准控制,达到强度与韧性的平衡。
2.2.3 织构取向与位错网络
增材制造工艺逐层构建的特点易导致强织构取向。通过选择性激光熔化和电子束熔化技术制备的高熵合金,柱状晶沿热流方向生长,形成明显的织构。通过调节激光扫描路径或束流偏转角度,可以优化织构取向,进一步提升特定方向上的性能。此外,在增材制造过程中,快速冷却和高温梯度引入了大量位错和孪晶边界,这些缺陷有助于提升材料的强度和抗蠕变性能。
2.2.4 沉淀析出与元素分布均匀性
在直接能量沉积和激光熔化沉积等技术中,由于熔池较大且冷却速率相对较低,容易出现沉淀析出现象。通过优化粉末成分和熔池温度梯度,可以生成细小且分布均匀的析出相,进而提高材料的硬度和耐磨性。同时,直接能量沉积的多料斗进料方式能够实现多元素均匀分布,避免传统工艺中常见的偏析问题。
2.2.5 微观缺陷与致密度控制
增材制造技术在快速成形的同时也可能引入孔隙、裂纹等缺陷。选择性激光熔化技术通过优化激光功率、扫描速度和层厚等参数,可显著降低孔隙率,提高零件致密度。电子束熔化技术通过预热粉末床可减少残余应力和热裂纹的生成,而直接能量沉积技术则可以通过多次熔覆重熔消除不连续的熔池缺陷。
综上所述,增材制造技术在高熵合金的组织调控中展现了独特优势,通过精确的工艺控制优化微观结构,为性能提升奠定了基础。这些特点为后续优化工艺提供了理论支持,成为改善高熵合金性能的重要途径。
2.3 增材制造技术的比较与适用性分析
不同增材制造技术在组织调控中的应用各具特色,其工艺特点决定了适用范围和最终性能表现。以下从微观结构调控能力、成分设计灵活性和工业应用适配性3个维度对主要技术进行分析:
2.3.1 选择性激光熔化技术与电子束熔化技术
选择性激光熔化技术和电子束熔化技术均为粉末床熔融技术。选择性激光熔化技术利用高能激光在惰性气氛中快速熔化粉末,形成细小柱状晶和非平衡结构,适合制备复杂形状的小型零件。其高冷却速率有效防止金属间化合物的形成。然而,选择性激光熔化技术工艺对激光功率和扫描速度等参数要求严格,稍有偏差可能导致裂纹生成。相比之下,电子束熔化技术在高真空环境中操作,通过预热粉末床减小残余应力和热裂纹,适合制备尺寸较大的零件,但其冷却速率较低,对微观组织的细化能力有限。
2.3.2 直接能量沉积技术与激光熔化沉积技术
直接能量沉积技术和激光熔化沉积技术通过逐层沉积的方式构建零件,其中直接能量沉积技术可通过多料斗进料实现原位合金化,适合复杂成分设计和梯度功能材料的制备。其高沉积速率和材料灵活性使其在大型零件制造中具有优势,但需通过多次重熔优化元素分布。激光熔化沉积技术通过动态送粉的方式与激光束同步作用,可实现复杂几何形状部件的高效制造,但在微观组织细化和致密度方面不及选择性激光熔化技术。
2.3.3 线弧增材制造技术
线弧增材制造技术以电弧为热源,利用金属线材逐层堆积,具有较高的沉积效率和较低的成本,是制造大尺寸金属部件的理想选择。然而,其冷却速率较慢,容易导致残余应力和成分偏析,且表面质量较差,需进行后续加工以提升精度。
综上所述,增材制造技术为高熵合金的制备开辟了新的工艺路径,各技术在微观组织调控、成分均匀性和性能优化等方面各具优势。目前实验室针对不同增材制造技术在制备高熵合金时存在的问题与不足,研究通过优化工艺参数和开发新型粉末材料,克服当前的技术瓶颈,以期获得性能更好的高熵合金。
增材制造技术对高熵合金性能优化分析
3.1 工艺优化对性能的影响
高熵合金的性能优化需在多个尺度上进行调控。首先是纳米尺度:通过增材制造实现亚稳相和纳米析出物的精确控制,提高材料的强度和抗疲劳等性能。然后是微观尺度:调整晶粒尺寸、形状和取向,优化抗拉强度和延展性等。最后还要考虑到宏观尺度:通过复合材料设计(如异质结构)实现多功能性能的综合提升。目前研究的优化方向主要集中在优化增材制造工艺参数,通过调整工艺参数来改善性能。工艺优化的核心要素主要分为以下3个方面。
(1)激光功率:优化激光功率可以改变材料的熔池形态,图2所示为3种不同类型的熔池。可通过控制不同的熔池类型,从而控制微观组织的晶粒尺寸和分布。高激光功率可能导致熔池过度熔化,产生孔洞或微裂纹,而低激光功率则可能导致熔池不足,形成未熔缺陷。
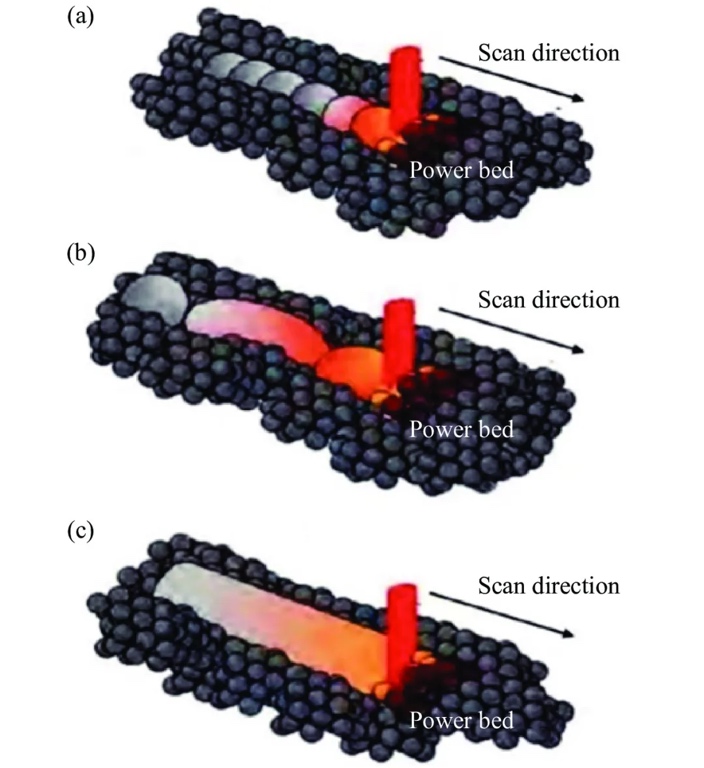
(责任编辑:admin)