航空航天增材制造:3D打印优化的低压涡轮叶片
时间:2019-10-10 08:42 来源:中国3D打印网 作者:中国3D打印网 阅读:次
中国3D打印网10月10日讯,一组研究人员在《中空低压涡轮叶片的初步优化》中探讨了用于制造关键工业组件的增材制造工艺。随着材料科学的飞速发展,通过3D打印和增材制造创建零件的选择有很多。 Abrusci指出,GE Advanced Turboprop(35%的添加剂制造)令人印象深刻,并意在为塞斯纳·德纳利(Cessna Denali)单引擎飞机提供动力。
与传统方法相比,增材制造具有实质性的优势,特别是在生产速度和重量轻(降低5%)。 Abrusci指出以下是最受欢迎的PDF技术:
.EOS的选择性激光烧结(SLS)或直接金属激光烧结(DMLS)
.雷尼绍的选择性激光熔化(SLM)
.规格分析
.初始形状
.定义一组参数
.参数优化
.形状验证
“假设通过单个增材制造过程制造零件,则设计过程首先要定义一组功能性表面,其功能是帮助将零件组装到其他零件上,传递机械或热负荷或确保液体或气密性,以防止零件与其他零件碰撞以及允许流体循环。” Abrusci说。 “此外,零件的材料必须符合制造过程以及行为要求。”在选择材料时,由于零件具有较高的机械性能,因此可能会使用更轻的组件。 Abrusci指出,通过AM工艺,可以使用更好的材料,例如钴铬合金,Ti6Al4V和Inconel。在优化过程中,用户倾向于非常关注重量,而重量是材料的主要组成部分。
在用于增材制造的水上设计中,工业用户还必须考虑:
.优化方法选择
.优化响应定义
.优化目标和约束功能定义
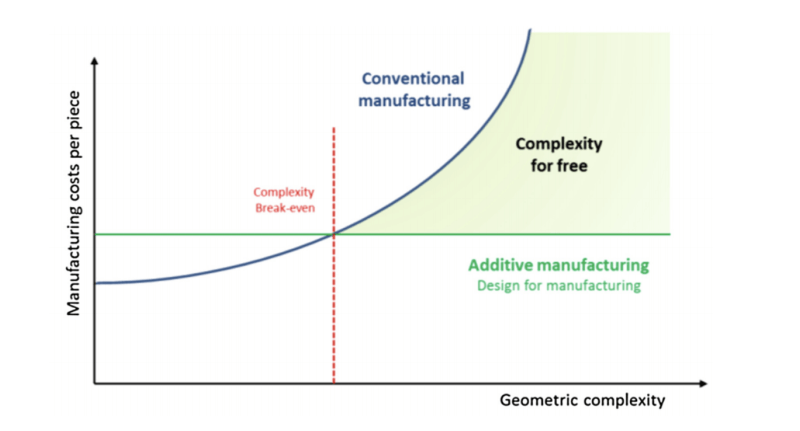
AM技术的成本与零件复杂度
使用创新的轻质材料的能力使增材制造工艺对航空航天业具有吸引力,并且更易于用于涡轮叶片之类的组件-具有简化的几何形状和最终的拓扑优化。这项研究的特色是Avio Aero(GE航空业务部门),因为他们试图利用优化的拓扑。本论文的研究案例是安装在航空涡轮风扇发动机上的低压涡轮转子叶片。基本结构由风扇,压缩机,燃烧室,高/低压涡轮机和喷嘴组成。转子叶片由护罩,叶片主体,轴和燕尾组成。该模型的验证包括:
.设计空间和非设计空间的定义
.网格,载荷和约束的应用
.基本模型的静态分析,与基线的比较
.拓扑优化包括设置功能,响应,参数等,以提高性能。
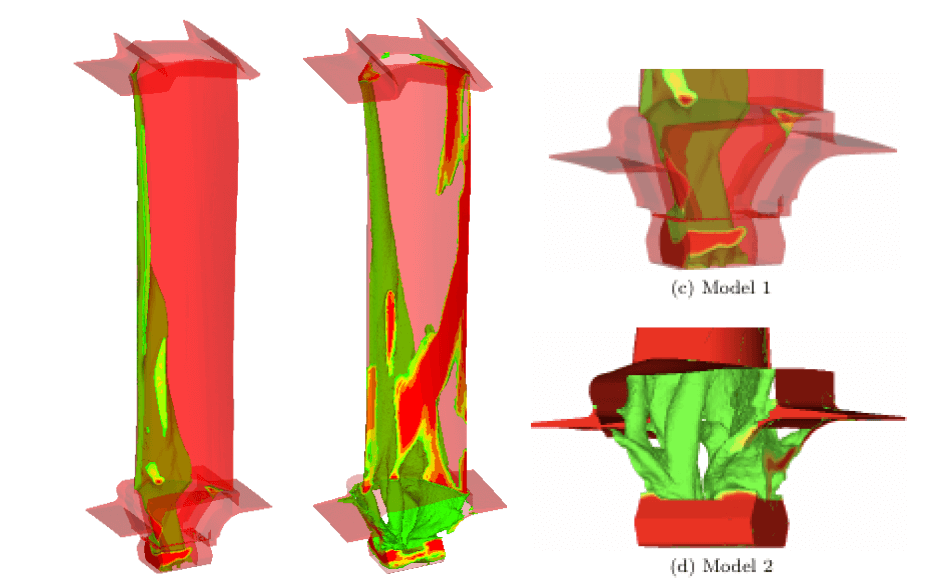
拓扑优化结果
模型1包含悬挑约束,但是模型2(由于设计空间更加复杂)需要进行修改以实现收敛性优化。“静态分析结果与拓扑优化结果完全匹配;因此,所开发的方法论得到了验证。……需要采取进一步的步骤来开展有效的业务案例可行性研究,首先需要进行初步的CAD重建,以验证最终设计,还需要进行LCF和HCF分析;如果存在较高的残余应力或其他不良影响,设计人员应进行其他结构优化,并在最后一步进行完整的过程仿真。”

模型2的平滑处理没有悬垂约束
与传统方法相比,增材制造具有实质性的优势,特别是在生产速度和重量轻(降低5%)。 Abrusci指出以下是最受欢迎的PDF技术:
.EOS的选择性激光烧结(SLS)或直接金属激光烧结(DMLS)
.雷尼绍的选择性激光熔化(SLM)
.ARCAM的电子束熔化(EBM)
AM技术对全球行业的影响
总体而言,增材制造为工业用户带来了巨大的好处,因为与传统的组装设计(DFA)和制造设计(DFM)技术相比,他们可以享受更轻松,更实惠的生产。 AM还可以直接制造复杂零件,甚至包括装甲,曲柄滑块机构,齿轮,铰链,接头等等。减少了材料浪费,可以用更少的零件制造零件,从而使组装更容易。
增材制造设计(DFAM)包括以下内容:.规格分析
.初始形状
.定义一组参数
.参数优化
.形状验证
“假设通过单个增材制造过程制造零件,则设计过程首先要定义一组功能性表面,其功能是帮助将零件组装到其他零件上,传递机械或热负荷或确保液体或气密性,以防止零件与其他零件碰撞以及允许流体循环。” Abrusci说。 “此外,零件的材料必须符合制造过程以及行为要求。”在选择材料时,由于零件具有较高的机械性能,因此可能会使用更轻的组件。 Abrusci指出,通过AM工艺,可以使用更好的材料,例如钴铬合金,Ti6Al4V和Inconel。在优化过程中,用户倾向于非常关注重量,而重量是材料的主要组成部分。
在用于增材制造的水上设计中,工业用户还必须考虑:
.优化方法选择
.优化响应定义
.优化目标和约束功能定义
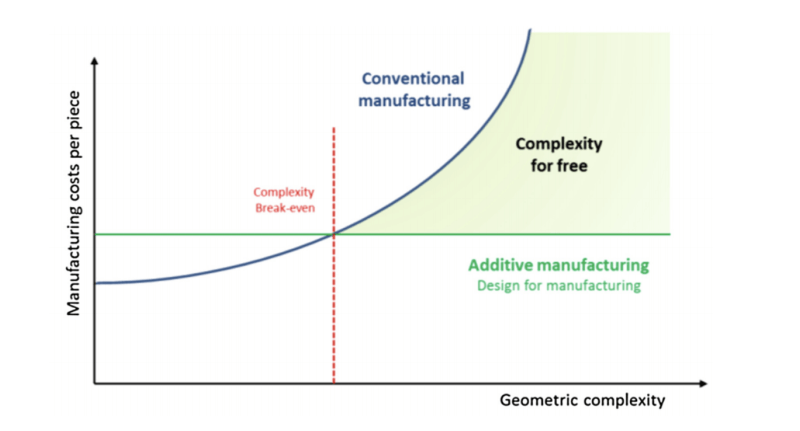
AM技术的成本与零件复杂度
使用创新的轻质材料的能力使增材制造工艺对航空航天业具有吸引力,并且更易于用于涡轮叶片之类的组件-具有简化的几何形状和最终的拓扑优化。这项研究的特色是Avio Aero(GE航空业务部门),因为他们试图利用优化的拓扑。本论文的研究案例是安装在航空涡轮风扇发动机上的低压涡轮转子叶片。基本结构由风扇,压缩机,燃烧室,高/低压涡轮机和喷嘴组成。转子叶片由护罩,叶片主体,轴和燕尾组成。该模型的验证包括:
.设计空间和非设计空间的定义
.网格,载荷和约束的应用
.基本模型的静态分析,与基线的比较
.拓扑优化包括设置功能,响应,参数等,以提高性能。
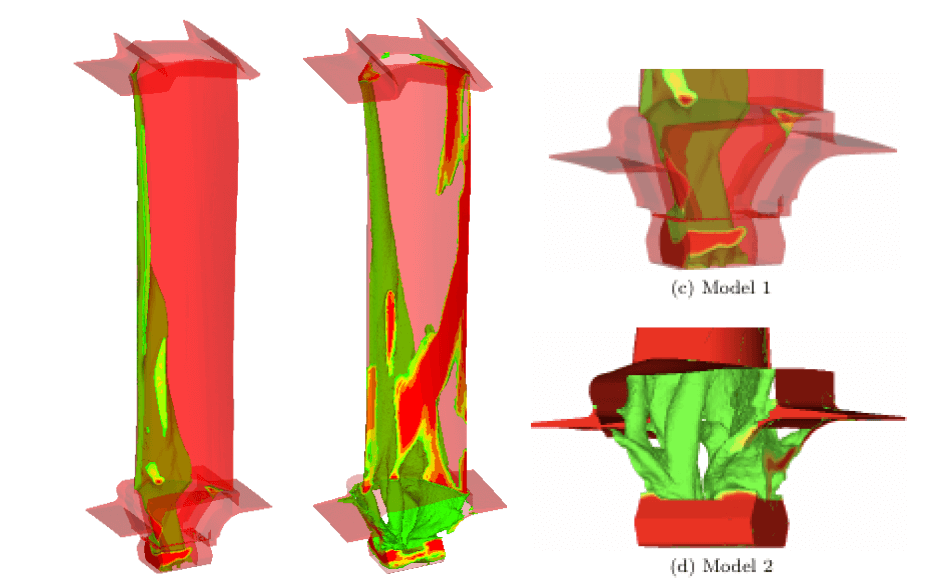
拓扑优化结果
模型1包含悬挑约束,但是模型2(由于设计空间更加复杂)需要进行修改以实现收敛性优化。“静态分析结果与拓扑优化结果完全匹配;因此,所开发的方法论得到了验证。……需要采取进一步的步骤来开展有效的业务案例可行性研究,首先需要进行初步的CAD重建,以验证最终设计,还需要进行LCF和HCF分析;如果存在较高的残余应力或其他不良影响,设计人员应进行其他结构优化,并在最后一步进行完整的过程仿真。”

模型2的平滑处理没有悬垂约束
中国3D打印网点评:几十年来,航空航天业一直在接受3D打印,但是增材制造的创新在过去几年加速了,特别是随着该技术成为主流,生产了如雷达系统,支架和其他类型涡轮等部件。
中国3D打印网原创文章!
(责任编辑:admin)
最新内容
热点内容