增材制造镍基高温合金在航空发动机与燃气轮机中的研究应用进展
时间:2024-04-02 09:57 来源:《航空材料学报》 作者:admin 阅读:次
来源:《航空材料学报》
作者:吴宇、陈冰清、刘伟、黄帅、孙兵兵、张学军、陈沛、黄辰
作者单位:中国航发增材制造技术创新中心;中国航发北京航空材料研究院 3D打印研究与工程技术中心;航发优材(镇江)增材制造有限公司 技术部;石油和化学工业规划院石油化工处
镍基高温合金具有良好的高温性能,被广泛用于航空发动机与燃气轮机热端部件的制造。增材制造逐点快速熔凝、逐层累积堆叠的工艺特点,不仅可实现高性能复杂结构零件的快速制造,还可用于损伤零件的高效率、高质量修复。目前,增材制造技术已逐渐成为镍基高温合金零件制备及修复的重要技术途径之一。本文综述了增材制造镍基高温合金在显微组织与冶金缺陷研究方面的进展,总结现有文献中GH3536、GH3625和GH4169三种常用镍基高温合金的拉伸性能,介绍增材制造镍基高温合金零件在航空发动机及燃气轮机中的典型应用案例。最后,针对现有研究存在的问题及制约增材制造镍基高温合金零件应用的困难,提出从设计增材制造专用镍基高温合金成分、建立增材制造镍基高温合金专用热处理/热等静压工艺、开发单晶镍基高温合金增材制造技术、发展增材制造实时监测控制技术、创新增材制造零件内表面处理技术等方面,进一步促进增材制造镍基高温合金零件的工程应用。
镍基高温合金在600℃以上具有出色的组织稳定性、抗氧化性能、抗热腐蚀性能及力学性能,是热端部件制造的重要材料,在航空发动机与燃气轮机中具有广泛应用,传统制备工艺主要为铸造、锻造及粉末冶金[1-2]。随着航空发动机与燃气轮机的快速发展,镍基高温合金零件表现出复杂化、轻量化、一体化的发展趋势,对镍基高温合金制备工艺提出了新的需求。
增材制造技术是一种近净成形工艺,通过激光、电子束、电弧等高能束热源逐层熔化粉末或丝材,以逐层堆叠的方式实现零件制备。常用的镍基高温合金增材制造工艺主要有激光粉末床熔融(laser powder bedfusion,LPBF)、电子束熔融(electron beam melting,EBM)、激光直接熔化沉积(laser direct energy deposition,LDED)和电弧增材制造(wire arc additive manufacturing,WAAM)[3-4]。
相较于传统工艺,增材制造技术更适合进行复杂结构零件制造。增材制造技术与拓扑优化、集成化设计等设计方法相结合可提高设计自由度,在促进装备轻量化的同时,还能缩短加工周期。罗罗公司使用增材制造技术,使零件制造周期缩短了30%[5]。其为TrentXWB-84发动机生产的低压涡轮,质量减轻约40%[6]。利勃海尔公司采用增材制造替代传统制造技术,使零件质量减少35%,零件数量减少10个,生产时间缩短75%[5]。
GE公司的增材制造T25传感器外壳将10个零件合并为1个零件,使传感器精度提高了30%。2015年,该零件成为首个通过美国联邦航空局适航认证的增材制造航空发动机零件[7-8]。此外,增材制造过程冷却速度快、熔池固液界面温度梯度大,不仅易形成沿沉积方向连续外延生长的柱状晶,还可减少凝固过程中的成分偏析及组织粗大问题,适用于涡轮叶片修复。
2001年,瑞士洛桑联邦理工学院率先使用激光直接熔化沉积技术对CMSX-4合金叶片进行了修复[9-11]。美国普渡大学的一项研究指出,相较于更换新叶片,采用增材制造技术修复旧叶片,可减少36%的能源消耗[12]。因此,增材制造技术已逐渐成为具有良好可焊性镍基高温合金零件快速制造及修复的重要技术途径。
本文对增材制造镍基高温合金在航空发动机与燃气轮机中的研究应用现状进行综述,阐述增材制造镍基高温合金的显微组织特征及常见冶金缺陷的形成原因与控制方法,总结增材制造GH3536、GH3625和GH4169的室温/高温拉伸性能,介绍航空发动机及燃气轮机中增材制造镍基高温合金零件的应用情况。基于国内外研究现状,对今后的重要发展方向进行展望。
1 增材制造镍基高温合金显微组织
增材制造过程温度梯度大、冷却速度快,与传统工艺制备镍基高温合金的显微组织存在差异。采用不同增材制造方法成形的镍基高温合金的晶粒形貌均主要由沿沉积方向外延生长的柱状晶与少量等轴晶构成,具有明显的各向异性。直接能量沉积过程热量通过基板或已沉积部分散失,故柱状晶通常垂直于基板并稍向激光扫描方向倾斜。粉末床熔融成形过程熔池尺寸较小、对流更为剧烈,故柱状晶生长方向与直接能量沉积相比更为复杂[5]。
增材制造镍基高温合金的沉积态组织通常由γ相、γ'相、共晶组织、Laves相、金属间化合物和碳化物等组成(图1(a)~(c))[13]。Xu等[14]采用电弧增材制造技术制备的GH4169合金由沿沉积方向生长的粗大的柱状晶组成,柱状晶的长度和宽度分别约为11mm与0.8mm。
Tayon等[15]对电子束熔融GH4169合金的研究结果表明,沉积态组织具有较强的织构,在1190℃下进行热处理后柱状晶转变为等轴晶,织构显著减弱。有研究在激光粉末床熔融成形GH4169合金的沉积态组织中发现了脆性金属间化合物δ相和Laves相[16-17],还有报道指出激光直接熔化沉积GH4169合金中存在碳化物和Laves相[18]。
激光粉末床熔融成形GH3536合金的沉积态组织主要由单相奥氏体构成,晶界基本无析出物[19-20]。激光粉末床熔融成形GH3625合金沉积态组织主要由γ相基体、金属间化合物和Laves相构成[21-23]。Wang等[24]对激光直接熔化沉积IC10合金的研究表明,凝固过程中的成分偏析会导致晶界形成共晶组织。
非平衡相及Laves相的存在会对材料性能造成不良影响,因此要对成形合金进行热处理/热等静压处理,以改善其内部质量与显微组织。增材制造GH4169合金通常要进行固溶处理,使δ相和Laves相充分溶解,促进后续时效处理中γ'相的析出。由于Nb原子扩散能力较差,为了使δ相充分溶解,增材制造GH4169合金的固溶温度一般要高于锻件的固溶处理温度[25]。
Ni等[26]研究了固溶温度对激光粉末床熔融成形GH4169合金晶粒形貌的影响后指出,经980℃固溶处理后,柱状晶部分转化为等轴晶,导致了晶粒尺寸的减小;经1040℃和1100℃固溶处理后,柱状晶完全转化为等轴晶,不同热处理状态下GH4169合金的晶粒形貌如图1(d)~(g)所示。
激光粉末床熔融成形GH3536合金在经过热处理后,熔池边界消失,并伴随有等轴晶形成[27],其在经过热等静压处理后,晶粒长大并转变为等轴晶,且晶界与晶粒内部的溶质元素扩散会导致碳化物形成[19-20,28]。有研究指出,激光粉末床熔融GH3625合金在700℃固溶处理条件下,显微组织基本不发生变化。
当固溶温度升高至1000℃时,熔池边界消失,有碳化物在晶界析出。经过1150℃热处理后,晶粒进一步长大,且晶界处的碳化物也会明显发生粗化[29]。
Wang等[30]对激光直接熔化沉积GH3230合金的研究表明,合金沉积态组织中存在M23C6与M6C两种碳化物。经固溶处理后,碳化物含量与尺寸均明显减少,且M23C6碳化物完全消失。黄文普等[31]发现激光粉末床熔融成形K4202合金经固溶+时效处理后发生再结晶,且晶界和晶内均有碳化物析出。
增材制造镍基高温合金的定向生长特性,使其成为单晶高温合金制备与修复的重要手段。在单晶高温合金制备方面,Jodi等[32]使用激光粉末床熔融技术,通过平顶光在多晶合金基体上实现了单晶合金的制备。
近年来,随着电子束熔融技术的发展,采用该方法进行单晶高温合金制备成为研究重点之一。
Ramsperger等[33]首次使用电子束粉末床熔融技术制备了单晶高温合金。Körner等[34]制备的CMSX-4单晶高温合金在经过热处理后可达到与铸件相当的力学性能,某些性能甚至优于铸件(图1(h))。Fernandez-Zelaia等[35]研究了工艺参数对高温合金显微组织的影响,发现较高的能量输入可促进单晶的形成。Chauvet等[36]在预热温度约1020℃条件下,在不锈钢基板上制备了无裂纹的单晶高温合金。
林峰教授课题组[37]采用电子束粉末床熔融技术在不锈钢基板上制备了Inconel738单晶高温合金,由于单晶的形成对凝固条件具有很强的依赖性,因此制备不同尺寸的单晶高温合金需要使用不同的工艺参数。在单晶高温合金修复领域,洛桑联邦理工学院研究了激光直接熔化沉积工艺参数对CMSX-4合金组织影响规律,并对CMSX-4合金叶片进行了修复[8-10]。
Liang等[38-42]研究了激光快速凝固过程中单晶高温合金的凝固路径,分析了工艺参数对单晶高温合金显微组织的影响规律,并根据工艺优化结果在单晶基体上成功制备出具有良好定向性的单晶高温合金。
中国科学院金属研究所分析了热处理对增材制造单晶高温合金显微组织的影响,并通过调整工艺参数实现了DD32单晶涡轮叶片的修复[43-44]。Rottwinkel等[45]通过在CMSX-4单晶高温合金修复区周围施加预热及对底部进行水冷,实现了熔池热流方向的控制,从而保证了修复区单晶组织的完整性。
Wang等[46]对比了激光与等离子弧对DD407单晶高温合金的修复效果,发现两种工艺方法均可获得定向生长的单晶组织,但等离子弧修复后的热影响区更大。Zhang等[47]利用同步辐射技术发现了DD5单晶高温合金在激光快速熔凝过程中的晶体转动现象,为单晶高温合金增材制造及修复过程中的晶体取向控制提供了理论依据。
2 增材制造镍基高温合金冶金缺陷
孔隙和裂纹是增材制造镍基高温合金中较为常见的冶金缺陷。孔隙的形成原因主要有增材制造过程中环境及原材料粉末带来气体形成的气孔,凝固过程中液态金属收缩形成的孔洞及未完全熔化粉末颗粒之间的孔隙。对于粉末床熔融工艺,粉末颗粒间的孔隙也可能导致出现气孔[5,49]。增材制造镍基高温合金中的气孔难以避免,但是可通过优化增材制造工艺参数、控制原材料粉末质量、降低成形过程的氧含量及热等静压等手段减小气孔率。对于未融化粉末导致的孔隙,可通过适当增加输入能量避免[50]。Tomus等[27]采用热等静压消除了激光粉末床熔融GH3536合金内部孔隙,提高了材料的室温伸长率。Han等[51]对激光粉末床熔融GH3536合金进行了热等静压处理,消除了材料内部的孔隙与微裂纹,改善了合金的疲劳性能,但同时也导致了抗拉强度与屈服强度的下降。
开裂是目前限制增材制造技术在镍基高温合金制备中应用的主要障碍,增材制造合金裂纹形成机制主要有三种[52-53]:
(1)凝固裂纹:凝固裂纹形成于熔池凝固的最后阶段,在该阶段液相充形困难,凝固收缩引起的应力使枝晶间的液膜被撕裂,导致裂纹出现(图2(a));
(2)液化裂纹:液化裂纹形成于后续沉积过程中,枝晶间的低熔点析出物或共晶组织在后续沉积热循环中熔化形成液膜,液膜在内应力作用下被撕裂形成裂纹(图2(b));
(3)固态裂纹:固态裂纹也是在后续沉积中形成的,但固态裂纹的形成是由于内应力超过了固体材料的抗拉强度导致的,未出现局部熔化(图2(c))。晶界结构、化学成分、成分偏析、晶粒尺寸及内应力等都会对增材制造镍基高温合金裂纹的形成造成影响。凝固过程中大角度晶界处残留的液膜较多、界面能较高,易发生开裂。与大角度晶界相比,小角度晶界具有更好的稳定性,开裂倾向较低[54-55]。Chauvet等[56]的研究表明,当晶界的取向差角大于15°时,易沿晶界形成裂纹(图2(d)、(e))。Guo等[52]对激光直接熔化沉积GH3536合金的开裂行为进行研究后发现,晶界取向差角在25°~45°之间时,晶界的界面能较高,因此更易开裂。合金的化学成分与凝固末期的成分偏析会导致凝固温度范围增大、晶界液膜存在时间延长、阻碍液相填充枝晶间空隙并促进晶间低熔点相形成,从而增加开裂倾向[57-59]。合金的凝固温度范围越大,越易形成凝固裂纹[60]。激光直接熔化沉积GH3536合金裂纹附近区域的化学元素分布如图2(f)所示。Cloots等[61]认为成分偏析是导致激光粉末床熔融IN738LC合金开裂的主要因素之一。在成分偏析作用下,晶界富集的元素不仅会阻碍液相流动,还可能削弱材料强度,从而增大了材料开裂倾向[62-63]。
针对裂纹形成原因,可通过控制成形工艺、调整合金成分及热等静压等手段抑制或消除增材制造镍基高温合金中的裂纹。凝固裂纹及液化裂纹形成机理示意图分别如图2(g)、(h)所示。在成形工艺控制方面,张洁等[22]指出,基板预热可降低激光粉末床熔融GH3625残余应力,从而抑制裂纹产生。当预热温度为300℃时,裂纹数量最少。Kontis等[64]通过调整电子束粉末床熔融工艺参数获得了较大的晶界面积与较小晶粒尺寸,使热应力在晶界上分布更为均匀,同时,调节工艺参数还可降低成分偏析,抑制硼化物的形成;通过以上途径,改善了镍基高温合金的开裂倾向。Xu等[66]研究了扫描策略对激光粉末床熔融Inconel738合金开裂倾向的影响,发现相邻两层的扫描方向每次旋转67°可促进等轴晶形成,有效抑制裂纹形成,获得良好的力学性能。对于可焊性较差的镍基高温合金,仅调整工艺参数难以完全防止开裂,还需对合金成分进行调整。Tomus等[67]指出,降低Si、C元素含量可改善激光粉末床熔融GH3536合金的抗开裂能力。Harrison等[68]通过增加固溶强化元素、减少杂质元素,降低了GH3536合金在激光粉末床熔融成形过程中的开裂倾向,其研究结果显示,GH3536合金在经过成分调整后,裂纹密度下降了约65%,且高温拉伸强度显著升高。Tang等[69]研究了合金成分、成形性与力学性能之间的关系,并在此基础上设计了ABD-850AM与ABD-900AM两种高性能、无裂纹的新型增材制造用镍基高温合金,他们认为通过降低合金凝固温度区间、减少晶界析出物与低熔点共晶组织、提高合金的高温塑性等手段可抑制增材制造镍基高温合金中的裂纹形成。此外,细化晶粒可使每个晶界承受的局部应变减小,并提高液相的充形能力,从而增强合金的抗开裂能力[52]。Han等[70]通过向GH3536合金中加入纳米TiC颗粒,促进凝固过程中的异质形核,使小角度晶界增多,减轻了粉末床熔融GH3536合金的开裂倾向。Cheng等[71]在GH3536合金粉末表面采用原位化学合成方法制备了Y2O3涂层,使用表面改性后粉末为原材料进行激光粉末床熔融成形,Y2O3颗粒促进了凝固过程中的异质形核,形成了细小的组织,有效抑制了裂纹的萌生与扩展。
3 增材制造典型镍基高温合金拉伸性能
目前,GH3536、GH4169和GH3625合金的增材制造工艺相对较为成熟,易获得致密无开裂样品。增材制造镍基高温合金显微组织的各向异性导致其力学性能具有明显的各向异性,热处理可显著改善力学性能。增材制造镍基高温合金的室温和高温拉伸性能普遍高于铸造合金,但低于锻造合金,部分合金的力学性能可达到甚至超过锻件的力学性能[16,72]。
Wang等[73]对比了激光粉末床熔融成形GH3536合金与热锻GH3536合金的拉伸性能,发现激光粉末床熔融成形GH3536合金的强度高于热锻合金,但断后伸长率小于热锻合金。
Wang等[74]制备的激光粉末床熔融成形GH3625合金具有与锻造GH3625合金相近的拉伸性能。西北工业大学的研究结果显示,激光直接熔化沉积GH4169合金热处理后的力学性能可满足锻件标准[75]。
Strößner等[76]发现经过均匀化处理后的激光粉末床熔融成形GH4169合金同锻件性能相当。激光粉末床熔融成形GH3536合金经固溶(950℃保温3h后空冷)与热等静压处理(1125℃、110MPa保温4h炉冷)后,室温抗拉强度和伸长率分别可达750MPa与45%~50%。随着测试温度升高,抗拉强度逐渐下降,但伸长率则基本不变。当测试温度超过600℃后,抗拉强度和伸长率均出现下降;但当测试温度升高至815℃后,虽然抗拉强度仍然降低,但伸长率却有所升高[19]。
Sanchez-Mata等[77]的研究结果表明,GH3536合金沉积态的横向抗拉强度、屈服强度和伸长率分别为924.7、790.2MPa和25.7%,纵向抗拉强度、屈服强度和伸长率分别为777.1、662.8MPa和22.3%;在1177℃下保温2h空冷固溶处理后,横向抗拉强度、屈服强度和伸长率分别为792、384.8MPa和50.3%,纵向抗拉强度、屈服强度和伸长率分别为728.3、412.8MPa和43.4%。
在相同的热处理制度下,Montero-Sistiaga等[78]的研究结果显示,GH3536合金的横向抗拉强度、屈服强度和伸长率分别为709.5、325.5MPa和44.3%,纵向抗拉强度、屈服强度和伸长率分别为662.2、320.5MPa和44.9%。
其研究结果还表明,GH3536合金沉积态的横向抗拉强度、屈服强度和伸长率分别为787.5、552MPa和31.5%,纵向抗拉强度、屈服强度和长伸率分别为494.3、682.2MPa和36.9%;经800℃下保温2h空冷固溶处理后,材料的横向抗拉强度、屈服强度和伸长率分别为798.1、508.3MPa和31.8%,纵向抗拉强度、屈服强度和伸长率分别为728.3、484.4MPa和36.3%[78]。
激光粉末床熔融成形GH3625合金的沉积态抗拉强度、屈服强度和伸长率分别为(925±13)、(652± 10)MPa和(32±3)%;经900℃保温1h固溶处理后,抗拉强度、屈服强度和伸长率分别为(869±7)、(567±15)MPa和(38±1)%;经1100℃保温1h固溶处理后,抗拉强度、屈服强度和伸长率分别为(886±11)、(409±14)MPa和(56±5)%。
对激光直接熔化沉积GH3625合金,其沉积态抗拉强度、屈服强度和伸长率分别(1073±5)、(723±23)MPa和(26±2)%;经900℃保温1h固溶处理后,抗拉强度、屈服强度和伸长率分别为(1084±2)、(654±15)MPa和(27±2)%;经1100℃保温1h固溶处理后,抗拉强度、屈服强度和伸长率分别为(991±13)、(532±22)MPa和(43±1)%[79]。
图3~图5总结了部分文献中增材制造GH3536、GH4169和GH3625合金沉积态及经不同热处理/热等静压制度处理的室温/高温拉伸性能。可以看到,对于GH3536与GH3625合金,热处理虽然导致了强度下降,但促进了塑性的改善。对于GH4169合金,热处理提升了室温强度,但塑性有所降低。
值得注意的是,增材制造镍基高温合金力学性能的偏差较大。即便是同一种材料,不同文献报道的力学性能结果也存在一定差异。这可能与合金内部缺陷与显微组织随成形工艺与热处理/热等静压制度的变化有关。这一现象限制了增材制造镍基高温合金的工程应用,是现阶段亟需解决的问题之一。
4 增材制造镍基高温合金应用
目前,增材制造镍基高温合金构件已在航空发动机及燃气轮机中得到了初步应用。在航空发动机领域,国内的中国航发北京航空材料研究院、中国航发商用航空发动机有限公司、北京航空航天大学、西北工业大学、华中科技大学、中国科学院金属研究所、铂力特等单位对燃油喷嘴、涡流器、预旋喷嘴等航空发动机镍基高温合金零件的增材制造进行了研究。采用增材制造技术,可使燃油喷嘴的加工周期由6周左右缩短至一周以内,涡流器的加工周期由一个月左右缩短至3~5天[1,97]。
国际上,赛峰公司采用增材制造技术成形的镍基高温合金涡轮喷嘴通过了欧洲航空安全局认证[3]。印度斯坦航空公司制造了25kN发动机的镍基高温合金燃烧室机匣[3]。罗罗公司在进行新一代燃烧室制造时,首先采用增材制造技术制造8个燃烧室组件,再通过激光焊将组件焊接成1个整体(图6(b))。
与传统工艺相比,采用该技术路线进行燃烧室加工仅需3.5个月,加工周期缩短约70%[98]。霍尼韦尔公司利用电子束熔融技术制备的HTF7000发动机管腔,将原有的8个零件合并为1个,不但使交货周期大幅缩短,还降低了制造成本[3]。
在燃气轮机领域,GE公司于2021年采用激光粉末床熔融成形LM9000燃气轮机适配器盖(图6(c))取代了原有的铸造零件。这些零件均为一对一替换,没有进行重新设计或零件合并,仅针对增材制造工艺进行了微小调整。传统的铸造零部件通常需要12~18个月的生产时间,而增材制造仅需要10个月时间,采用增材制造技术削减了约35%的制造成本[99-100]。
美国橡树岭国家实验室与SolarTurbines合作,利用电子束熔融技术制备了Inconel738合金发电机涡轮叶片(图6(d))。他们计划后续利用增材制造技术成形复杂内部冷却通道,使涡轮机在更高温度下运行,以提高发电效率[101-102]。
为改善镍基高温合金涡轮叶片的热传递和冲击冷却效果,德国西门子公司采用激光粉末床熔融技术为SGT-400燃气轮机制备了具有复杂内部结构的叶片(图6(e)),叶片已在1250℃下通过了13000r/min旋转速度条件下的满负荷考核[1,103-104]。2017年,曼恩机械在MGT6100燃气轮机中使用了增材制造涡轮叶片,率先在世界上实现了复杂结构增材制造高温合金涡轮导向叶片的应用[105]。
5 总结与展望
本文综述了增材制造镍基高温合金在组织、缺陷及性能方面的研究进展,并介绍了增材制造镍基高温合金零件在航空发动机及燃气轮机中的应用情况。可以看到,虽然增材制造镍基高温合金在理论研究及工程应用方面都已取得巨大突破,但在组织性能调控及缺陷控制等方面仍存在一定问题,要实现增材制造镍基高温合金构件在航空发动机与燃气轮机中更广泛的应用,还需在以下方面进一步开展工作:
(1)设计增材制造专用镍基高温合金成分
合金成分设计要同时考虑材料的使用性能与加工性能,加工工艺对合金成分设计具有重要影响。目前,增材制造镍基高温合金主要使用传统牌号成分,而传统镍基高温合金的成分是基于铸造、锻造等工艺开发的,并不完全适合增材制造工艺。例如,易开裂是阻碍增材制造镍基高温合金应用的重要障碍之一,造成这一问题的主要原因是部分牌号镍基高温合金的成分在增材制造工艺条件下易形成凝固裂纹及液化裂纹。因此,需要针对增材制造工艺特点进行合金成分设计,充分发挥增材制造镍基高温合金的性能。
(2)建立增材制造镍基高温合金专用热处理/热等静压工艺
增材制造过程具有高温度梯度、高冷却速度和原位热循环等特点。与传统工艺制备镍基高温合金相比,增材制造镍基高温合金的显微组织表现出明显的各向异性,且第二相的种类、含量及分布等也可能存在差异,导致传统热处理制度不能完全适用于增材制造镍基高温合金。此外,部分牌号镍基高温合金在增材制造过程中易形成裂纹,需要进行热等静压处理使裂纹闭合,改善力学性能。但是,热等静压引起的显微组织变化可能导致力学性能恶化。因此,需要依据增材制造镍基高温合金显微组织与缺陷特点有针对性地建立热处理及热等静压工艺,改善力学性能。
(3)开发单晶高温合金叶片增材制造技术
单晶高温合金具有出色的高温性能,是制造航空发动机涡轮叶片的重要材料。目前,单晶高温合金叶片主要通过定向凝固技术进行制备。但是,铸造合金组织粗大、偏析严重、易形成铸造缺陷,制约了高温合金性能的充分发挥。增材制造过程中,熔池具有极高的温度梯度与冷却速度,有助于减少成分偏析、疏松以及组织粗大等问题。
通过增材制造技术进行单晶高温合金叶片制备,可进一步提升其力学性能。然而,增材制造技术目前主要用于叶片修复,尚未用于叶片制造。近年来,有研究发现使用电子束粉末床熔融技术及激光光束整形技术可在多晶合金基体上实现单晶高温合金制备。这一发现使得直接使用增材制造技术进行单晶高温合金叶片成形成为可能,有必要进行系统深入研究。
(4)发展增材制造实时监测控制技术
增材制造镍基高温合金的显微组织是在快速凝固及原位热循环过程中形成的,熔池的凝固条件及原位热循环的升温/冷却速率是增材制造镍基高温合金显微组织的主要影响因素,决定了共晶组织、γ相、γ′相,析出相等的分布、含量及尺寸等特征。
此外,增材制造过程的温度场及应力场变化对材料变形开裂具有重要影响。尤其是对于易开裂镍基高温合金,需严格控制成形过程温度场及应力场才能获得成形质量良好的零件。同时,粉末及其他杂质在成形过程中的飞溅,可能导致未熔合、夹杂、层间开裂等缺陷。因此,有必要发展增材制造实时监测控制技术,依据温度、图像等信号对工艺参数进行调控,提高增材制造镍基高温合金成形质量稳定性。
(5)创新增材制造零件内表面处理技术
由于增材制造是逐层叠加过程,因此构件表面通常较为粗糙。虽然通过改进原材料粉末质量、调整成形过程零件摆放位置、优化工艺参数等手段可在一定程度上改善表面质量,但无法完全解决表面粗糙问题。
因此,增材制造零件必须经过表面处理后方可使用。增材制造零件通常具有复杂的内部结构,而现有的表面处理手段(磨粒流、电化学腐蚀、水射流、振动抛光、喷砂等)难以对复杂内表面进行有效处理,是限制增材制造零件工程应用的关键技术瓶颈之一。因此,需要开发新的内表面处理技术,促进增材制造零件应用。
(6)引入人工智能技术
人工智能具有强大的数据分析处理能力,且自动化程度和工作效率更高。利用人工智能对设计数据进行分析,能突破人类思维限制,进一步实现零件结构的快速优化设计。此外,使用人工智能对增材制造过程中产生的数据进行处理,预测可能产生的缺陷及何时需要对设备进行维护。不仅可在生产过程中提前对工艺参数进行调整,还可减少计划外停机时间,提高产品合格率及生产效率。
同时,采用人工智能对材料数据进行挖掘,建立“材料成分-冶金缺陷-力学性能”关系,在实验之前进行成分优化筛选,节约时间和资源,加速增材制造专用镍基高温合金成分开发。因此,有必要将人工智能与增材制造技术进行结合,促进增材制造技术快速发展。
(7)推动增材制造技术创新
虽然使用现有增材制造技术生产的零件已在航空发动机与燃气轮机中实现应用,但未来仍需进一步对增材制造技术进行改进创新,满足更大的应用需求。通过增材制造技术的发展,优化零件成形精度、改善设备稳定性、提高制造效率。
同时,将增材制造技术与智能制造、数字化工厂等技术相结合,实现增材制造的数字化转型。此外,还需要考虑环保和可持续发展问题,实现增材制造技术的绿色化、环保化、可持续发展化。
作者:吴宇、陈冰清、刘伟、黄帅、孙兵兵、张学军、陈沛、黄辰
作者单位:中国航发增材制造技术创新中心;中国航发北京航空材料研究院 3D打印研究与工程技术中心;航发优材(镇江)增材制造有限公司 技术部;石油和化学工业规划院石油化工处
镍基高温合金具有良好的高温性能,被广泛用于航空发动机与燃气轮机热端部件的制造。增材制造逐点快速熔凝、逐层累积堆叠的工艺特点,不仅可实现高性能复杂结构零件的快速制造,还可用于损伤零件的高效率、高质量修复。目前,增材制造技术已逐渐成为镍基高温合金零件制备及修复的重要技术途径之一。本文综述了增材制造镍基高温合金在显微组织与冶金缺陷研究方面的进展,总结现有文献中GH3536、GH3625和GH4169三种常用镍基高温合金的拉伸性能,介绍增材制造镍基高温合金零件在航空发动机及燃气轮机中的典型应用案例。最后,针对现有研究存在的问题及制约增材制造镍基高温合金零件应用的困难,提出从设计增材制造专用镍基高温合金成分、建立增材制造镍基高温合金专用热处理/热等静压工艺、开发单晶镍基高温合金增材制造技术、发展增材制造实时监测控制技术、创新增材制造零件内表面处理技术等方面,进一步促进增材制造镍基高温合金零件的工程应用。
镍基高温合金在600℃以上具有出色的组织稳定性、抗氧化性能、抗热腐蚀性能及力学性能,是热端部件制造的重要材料,在航空发动机与燃气轮机中具有广泛应用,传统制备工艺主要为铸造、锻造及粉末冶金[1-2]。随着航空发动机与燃气轮机的快速发展,镍基高温合金零件表现出复杂化、轻量化、一体化的发展趋势,对镍基高温合金制备工艺提出了新的需求。
增材制造技术是一种近净成形工艺,通过激光、电子束、电弧等高能束热源逐层熔化粉末或丝材,以逐层堆叠的方式实现零件制备。常用的镍基高温合金增材制造工艺主要有激光粉末床熔融(laser powder bedfusion,LPBF)、电子束熔融(electron beam melting,EBM)、激光直接熔化沉积(laser direct energy deposition,LDED)和电弧增材制造(wire arc additive manufacturing,WAAM)[3-4]。
相较于传统工艺,增材制造技术更适合进行复杂结构零件制造。增材制造技术与拓扑优化、集成化设计等设计方法相结合可提高设计自由度,在促进装备轻量化的同时,还能缩短加工周期。罗罗公司使用增材制造技术,使零件制造周期缩短了30%[5]。其为TrentXWB-84发动机生产的低压涡轮,质量减轻约40%[6]。利勃海尔公司采用增材制造替代传统制造技术,使零件质量减少35%,零件数量减少10个,生产时间缩短75%[5]。
GE公司的增材制造T25传感器外壳将10个零件合并为1个零件,使传感器精度提高了30%。2015年,该零件成为首个通过美国联邦航空局适航认证的增材制造航空发动机零件[7-8]。此外,增材制造过程冷却速度快、熔池固液界面温度梯度大,不仅易形成沿沉积方向连续外延生长的柱状晶,还可减少凝固过程中的成分偏析及组织粗大问题,适用于涡轮叶片修复。
2001年,瑞士洛桑联邦理工学院率先使用激光直接熔化沉积技术对CMSX-4合金叶片进行了修复[9-11]。美国普渡大学的一项研究指出,相较于更换新叶片,采用增材制造技术修复旧叶片,可减少36%的能源消耗[12]。因此,增材制造技术已逐渐成为具有良好可焊性镍基高温合金零件快速制造及修复的重要技术途径。
本文对增材制造镍基高温合金在航空发动机与燃气轮机中的研究应用现状进行综述,阐述增材制造镍基高温合金的显微组织特征及常见冶金缺陷的形成原因与控制方法,总结增材制造GH3536、GH3625和GH4169的室温/高温拉伸性能,介绍航空发动机及燃气轮机中增材制造镍基高温合金零件的应用情况。基于国内外研究现状,对今后的重要发展方向进行展望。
1 增材制造镍基高温合金显微组织
增材制造过程温度梯度大、冷却速度快,与传统工艺制备镍基高温合金的显微组织存在差异。采用不同增材制造方法成形的镍基高温合金的晶粒形貌均主要由沿沉积方向外延生长的柱状晶与少量等轴晶构成,具有明显的各向异性。直接能量沉积过程热量通过基板或已沉积部分散失,故柱状晶通常垂直于基板并稍向激光扫描方向倾斜。粉末床熔融成形过程熔池尺寸较小、对流更为剧烈,故柱状晶生长方向与直接能量沉积相比更为复杂[5]。
增材制造镍基高温合金的沉积态组织通常由γ相、γ'相、共晶组织、Laves相、金属间化合物和碳化物等组成(图1(a)~(c))[13]。Xu等[14]采用电弧增材制造技术制备的GH4169合金由沿沉积方向生长的粗大的柱状晶组成,柱状晶的长度和宽度分别约为11mm与0.8mm。
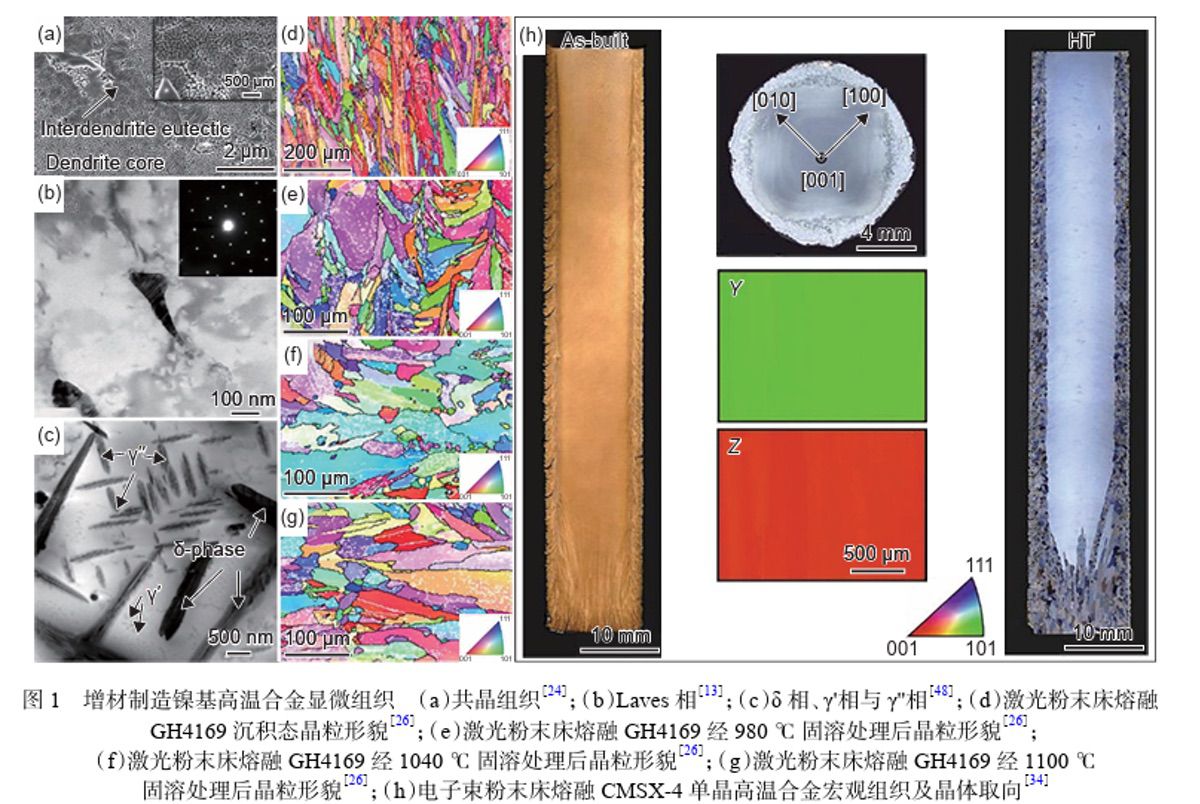
激光粉末床熔融成形GH3536合金的沉积态组织主要由单相奥氏体构成,晶界基本无析出物[19-20]。激光粉末床熔融成形GH3625合金沉积态组织主要由γ相基体、金属间化合物和Laves相构成[21-23]。Wang等[24]对激光直接熔化沉积IC10合金的研究表明,凝固过程中的成分偏析会导致晶界形成共晶组织。
非平衡相及Laves相的存在会对材料性能造成不良影响,因此要对成形合金进行热处理/热等静压处理,以改善其内部质量与显微组织。增材制造GH4169合金通常要进行固溶处理,使δ相和Laves相充分溶解,促进后续时效处理中γ'相的析出。由于Nb原子扩散能力较差,为了使δ相充分溶解,增材制造GH4169合金的固溶温度一般要高于锻件的固溶处理温度[25]。
Ni等[26]研究了固溶温度对激光粉末床熔融成形GH4169合金晶粒形貌的影响后指出,经980℃固溶处理后,柱状晶部分转化为等轴晶,导致了晶粒尺寸的减小;经1040℃和1100℃固溶处理后,柱状晶完全转化为等轴晶,不同热处理状态下GH4169合金的晶粒形貌如图1(d)~(g)所示。
激光粉末床熔融成形GH3536合金在经过热处理后,熔池边界消失,并伴随有等轴晶形成[27],其在经过热等静压处理后,晶粒长大并转变为等轴晶,且晶界与晶粒内部的溶质元素扩散会导致碳化物形成[19-20,28]。有研究指出,激光粉末床熔融GH3625合金在700℃固溶处理条件下,显微组织基本不发生变化。
当固溶温度升高至1000℃时,熔池边界消失,有碳化物在晶界析出。经过1150℃热处理后,晶粒进一步长大,且晶界处的碳化物也会明显发生粗化[29]。
Wang等[30]对激光直接熔化沉积GH3230合金的研究表明,合金沉积态组织中存在M23C6与M6C两种碳化物。经固溶处理后,碳化物含量与尺寸均明显减少,且M23C6碳化物完全消失。黄文普等[31]发现激光粉末床熔融成形K4202合金经固溶+时效处理后发生再结晶,且晶界和晶内均有碳化物析出。
增材制造镍基高温合金的定向生长特性,使其成为单晶高温合金制备与修复的重要手段。在单晶高温合金制备方面,Jodi等[32]使用激光粉末床熔融技术,通过平顶光在多晶合金基体上实现了单晶合金的制备。
近年来,随着电子束熔融技术的发展,采用该方法进行单晶高温合金制备成为研究重点之一。
Ramsperger等[33]首次使用电子束粉末床熔融技术制备了单晶高温合金。Körner等[34]制备的CMSX-4单晶高温合金在经过热处理后可达到与铸件相当的力学性能,某些性能甚至优于铸件(图1(h))。Fernandez-Zelaia等[35]研究了工艺参数对高温合金显微组织的影响,发现较高的能量输入可促进单晶的形成。Chauvet等[36]在预热温度约1020℃条件下,在不锈钢基板上制备了无裂纹的单晶高温合金。
林峰教授课题组[37]采用电子束粉末床熔融技术在不锈钢基板上制备了Inconel738单晶高温合金,由于单晶的形成对凝固条件具有很强的依赖性,因此制备不同尺寸的单晶高温合金需要使用不同的工艺参数。在单晶高温合金修复领域,洛桑联邦理工学院研究了激光直接熔化沉积工艺参数对CMSX-4合金组织影响规律,并对CMSX-4合金叶片进行了修复[8-10]。
Liang等[38-42]研究了激光快速凝固过程中单晶高温合金的凝固路径,分析了工艺参数对单晶高温合金显微组织的影响规律,并根据工艺优化结果在单晶基体上成功制备出具有良好定向性的单晶高温合金。
中国科学院金属研究所分析了热处理对增材制造单晶高温合金显微组织的影响,并通过调整工艺参数实现了DD32单晶涡轮叶片的修复[43-44]。Rottwinkel等[45]通过在CMSX-4单晶高温合金修复区周围施加预热及对底部进行水冷,实现了熔池热流方向的控制,从而保证了修复区单晶组织的完整性。
Wang等[46]对比了激光与等离子弧对DD407单晶高温合金的修复效果,发现两种工艺方法均可获得定向生长的单晶组织,但等离子弧修复后的热影响区更大。Zhang等[47]利用同步辐射技术发现了DD5单晶高温合金在激光快速熔凝过程中的晶体转动现象,为单晶高温合金增材制造及修复过程中的晶体取向控制提供了理论依据。
2 增材制造镍基高温合金冶金缺陷
孔隙和裂纹是增材制造镍基高温合金中较为常见的冶金缺陷。孔隙的形成原因主要有增材制造过程中环境及原材料粉末带来气体形成的气孔,凝固过程中液态金属收缩形成的孔洞及未完全熔化粉末颗粒之间的孔隙。对于粉末床熔融工艺,粉末颗粒间的孔隙也可能导致出现气孔[5,49]。增材制造镍基高温合金中的气孔难以避免,但是可通过优化增材制造工艺参数、控制原材料粉末质量、降低成形过程的氧含量及热等静压等手段减小气孔率。对于未融化粉末导致的孔隙,可通过适当增加输入能量避免[50]。Tomus等[27]采用热等静压消除了激光粉末床熔融GH3536合金内部孔隙,提高了材料的室温伸长率。Han等[51]对激光粉末床熔融GH3536合金进行了热等静压处理,消除了材料内部的孔隙与微裂纹,改善了合金的疲劳性能,但同时也导致了抗拉强度与屈服强度的下降。
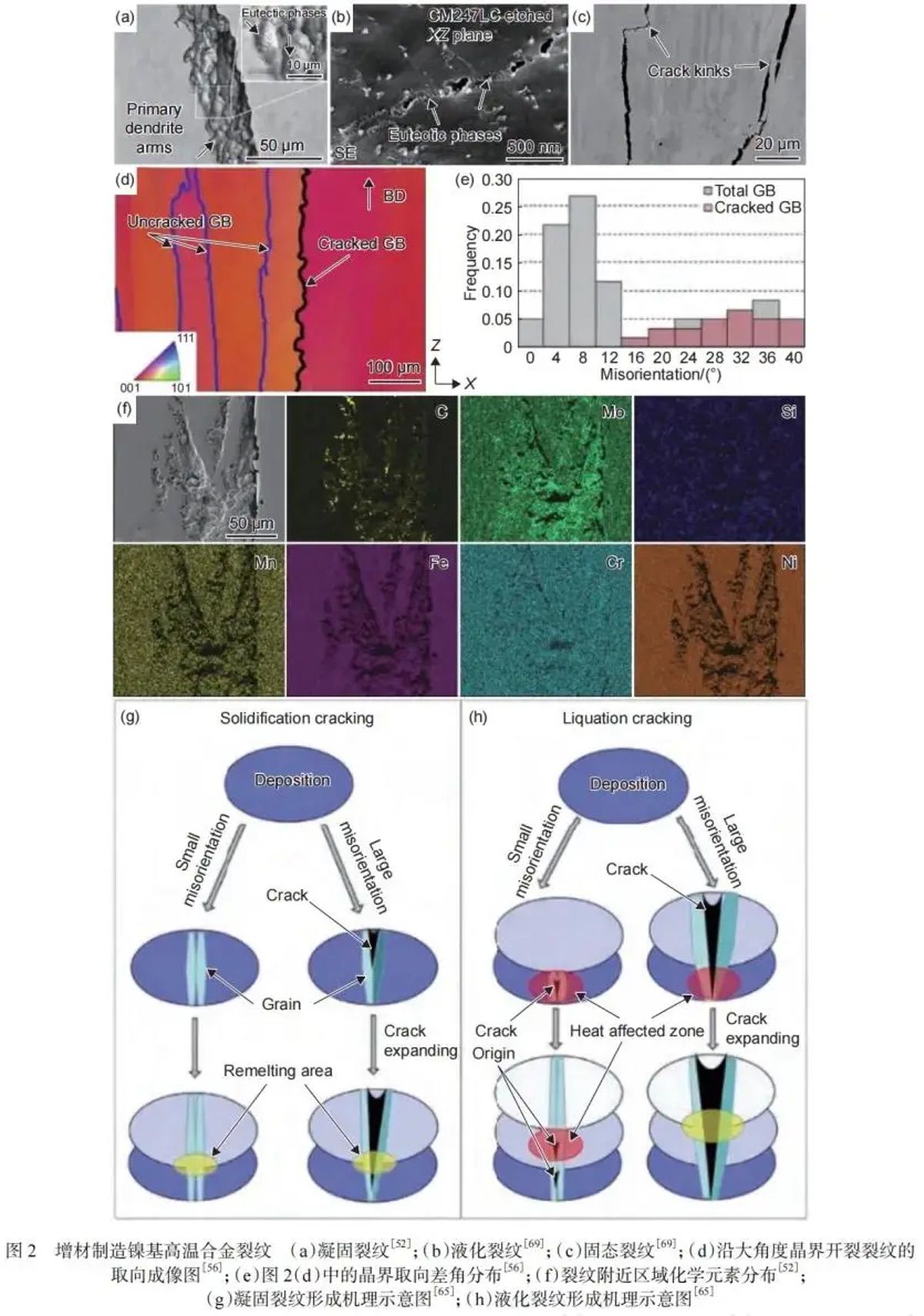
(1)凝固裂纹:凝固裂纹形成于熔池凝固的最后阶段,在该阶段液相充形困难,凝固收缩引起的应力使枝晶间的液膜被撕裂,导致裂纹出现(图2(a));
(2)液化裂纹:液化裂纹形成于后续沉积过程中,枝晶间的低熔点析出物或共晶组织在后续沉积热循环中熔化形成液膜,液膜在内应力作用下被撕裂形成裂纹(图2(b));
(3)固态裂纹:固态裂纹也是在后续沉积中形成的,但固态裂纹的形成是由于内应力超过了固体材料的抗拉强度导致的,未出现局部熔化(图2(c))。晶界结构、化学成分、成分偏析、晶粒尺寸及内应力等都会对增材制造镍基高温合金裂纹的形成造成影响。凝固过程中大角度晶界处残留的液膜较多、界面能较高,易发生开裂。与大角度晶界相比,小角度晶界具有更好的稳定性,开裂倾向较低[54-55]。Chauvet等[56]的研究表明,当晶界的取向差角大于15°时,易沿晶界形成裂纹(图2(d)、(e))。Guo等[52]对激光直接熔化沉积GH3536合金的开裂行为进行研究后发现,晶界取向差角在25°~45°之间时,晶界的界面能较高,因此更易开裂。合金的化学成分与凝固末期的成分偏析会导致凝固温度范围增大、晶界液膜存在时间延长、阻碍液相填充枝晶间空隙并促进晶间低熔点相形成,从而增加开裂倾向[57-59]。合金的凝固温度范围越大,越易形成凝固裂纹[60]。激光直接熔化沉积GH3536合金裂纹附近区域的化学元素分布如图2(f)所示。Cloots等[61]认为成分偏析是导致激光粉末床熔融IN738LC合金开裂的主要因素之一。在成分偏析作用下,晶界富集的元素不仅会阻碍液相流动,还可能削弱材料强度,从而增大了材料开裂倾向[62-63]。
针对裂纹形成原因,可通过控制成形工艺、调整合金成分及热等静压等手段抑制或消除增材制造镍基高温合金中的裂纹。凝固裂纹及液化裂纹形成机理示意图分别如图2(g)、(h)所示。在成形工艺控制方面,张洁等[22]指出,基板预热可降低激光粉末床熔融GH3625残余应力,从而抑制裂纹产生。当预热温度为300℃时,裂纹数量最少。Kontis等[64]通过调整电子束粉末床熔融工艺参数获得了较大的晶界面积与较小晶粒尺寸,使热应力在晶界上分布更为均匀,同时,调节工艺参数还可降低成分偏析,抑制硼化物的形成;通过以上途径,改善了镍基高温合金的开裂倾向。Xu等[66]研究了扫描策略对激光粉末床熔融Inconel738合金开裂倾向的影响,发现相邻两层的扫描方向每次旋转67°可促进等轴晶形成,有效抑制裂纹形成,获得良好的力学性能。对于可焊性较差的镍基高温合金,仅调整工艺参数难以完全防止开裂,还需对合金成分进行调整。Tomus等[67]指出,降低Si、C元素含量可改善激光粉末床熔融GH3536合金的抗开裂能力。Harrison等[68]通过增加固溶强化元素、减少杂质元素,降低了GH3536合金在激光粉末床熔融成形过程中的开裂倾向,其研究结果显示,GH3536合金在经过成分调整后,裂纹密度下降了约65%,且高温拉伸强度显著升高。Tang等[69]研究了合金成分、成形性与力学性能之间的关系,并在此基础上设计了ABD-850AM与ABD-900AM两种高性能、无裂纹的新型增材制造用镍基高温合金,他们认为通过降低合金凝固温度区间、减少晶界析出物与低熔点共晶组织、提高合金的高温塑性等手段可抑制增材制造镍基高温合金中的裂纹形成。此外,细化晶粒可使每个晶界承受的局部应变减小,并提高液相的充形能力,从而增强合金的抗开裂能力[52]。Han等[70]通过向GH3536合金中加入纳米TiC颗粒,促进凝固过程中的异质形核,使小角度晶界增多,减轻了粉末床熔融GH3536合金的开裂倾向。Cheng等[71]在GH3536合金粉末表面采用原位化学合成方法制备了Y2O3涂层,使用表面改性后粉末为原材料进行激光粉末床熔融成形,Y2O3颗粒促进了凝固过程中的异质形核,形成了细小的组织,有效抑制了裂纹的萌生与扩展。
3 增材制造典型镍基高温合金拉伸性能
目前,GH3536、GH4169和GH3625合金的增材制造工艺相对较为成熟,易获得致密无开裂样品。增材制造镍基高温合金显微组织的各向异性导致其力学性能具有明显的各向异性,热处理可显著改善力学性能。增材制造镍基高温合金的室温和高温拉伸性能普遍高于铸造合金,但低于锻造合金,部分合金的力学性能可达到甚至超过锻件的力学性能[16,72]。
Wang等[73]对比了激光粉末床熔融成形GH3536合金与热锻GH3536合金的拉伸性能,发现激光粉末床熔融成形GH3536合金的强度高于热锻合金,但断后伸长率小于热锻合金。
Wang等[74]制备的激光粉末床熔融成形GH3625合金具有与锻造GH3625合金相近的拉伸性能。西北工业大学的研究结果显示,激光直接熔化沉积GH4169合金热处理后的力学性能可满足锻件标准[75]。
Strößner等[76]发现经过均匀化处理后的激光粉末床熔融成形GH4169合金同锻件性能相当。激光粉末床熔融成形GH3536合金经固溶(950℃保温3h后空冷)与热等静压处理(1125℃、110MPa保温4h炉冷)后,室温抗拉强度和伸长率分别可达750MPa与45%~50%。随着测试温度升高,抗拉强度逐渐下降,但伸长率则基本不变。当测试温度超过600℃后,抗拉强度和伸长率均出现下降;但当测试温度升高至815℃后,虽然抗拉强度仍然降低,但伸长率却有所升高[19]。
Sanchez-Mata等[77]的研究结果表明,GH3536合金沉积态的横向抗拉强度、屈服强度和伸长率分别为924.7、790.2MPa和25.7%,纵向抗拉强度、屈服强度和伸长率分别为777.1、662.8MPa和22.3%;在1177℃下保温2h空冷固溶处理后,横向抗拉强度、屈服强度和伸长率分别为792、384.8MPa和50.3%,纵向抗拉强度、屈服强度和伸长率分别为728.3、412.8MPa和43.4%。
在相同的热处理制度下,Montero-Sistiaga等[78]的研究结果显示,GH3536合金的横向抗拉强度、屈服强度和伸长率分别为709.5、325.5MPa和44.3%,纵向抗拉强度、屈服强度和伸长率分别为662.2、320.5MPa和44.9%。
其研究结果还表明,GH3536合金沉积态的横向抗拉强度、屈服强度和伸长率分别为787.5、552MPa和31.5%,纵向抗拉强度、屈服强度和长伸率分别为494.3、682.2MPa和36.9%;经800℃下保温2h空冷固溶处理后,材料的横向抗拉强度、屈服强度和伸长率分别为798.1、508.3MPa和31.8%,纵向抗拉强度、屈服强度和伸长率分别为728.3、484.4MPa和36.3%[78]。
激光粉末床熔融成形GH3625合金的沉积态抗拉强度、屈服强度和伸长率分别为(925±13)、(652± 10)MPa和(32±3)%;经900℃保温1h固溶处理后,抗拉强度、屈服强度和伸长率分别为(869±7)、(567±15)MPa和(38±1)%;经1100℃保温1h固溶处理后,抗拉强度、屈服强度和伸长率分别为(886±11)、(409±14)MPa和(56±5)%。
对激光直接熔化沉积GH3625合金,其沉积态抗拉强度、屈服强度和伸长率分别(1073±5)、(723±23)MPa和(26±2)%;经900℃保温1h固溶处理后,抗拉强度、屈服强度和伸长率分别为(1084±2)、(654±15)MPa和(27±2)%;经1100℃保温1h固溶处理后,抗拉强度、屈服强度和伸长率分别为(991±13)、(532±22)MPa和(43±1)%[79]。
图3~图5总结了部分文献中增材制造GH3536、GH4169和GH3625合金沉积态及经不同热处理/热等静压制度处理的室温/高温拉伸性能。可以看到,对于GH3536与GH3625合金,热处理虽然导致了强度下降,但促进了塑性的改善。对于GH4169合金,热处理提升了室温强度,但塑性有所降低。
值得注意的是,增材制造镍基高温合金力学性能的偏差较大。即便是同一种材料,不同文献报道的力学性能结果也存在一定差异。这可能与合金内部缺陷与显微组织随成形工艺与热处理/热等静压制度的变化有关。这一现象限制了增材制造镍基高温合金的工程应用,是现阶段亟需解决的问题之一。
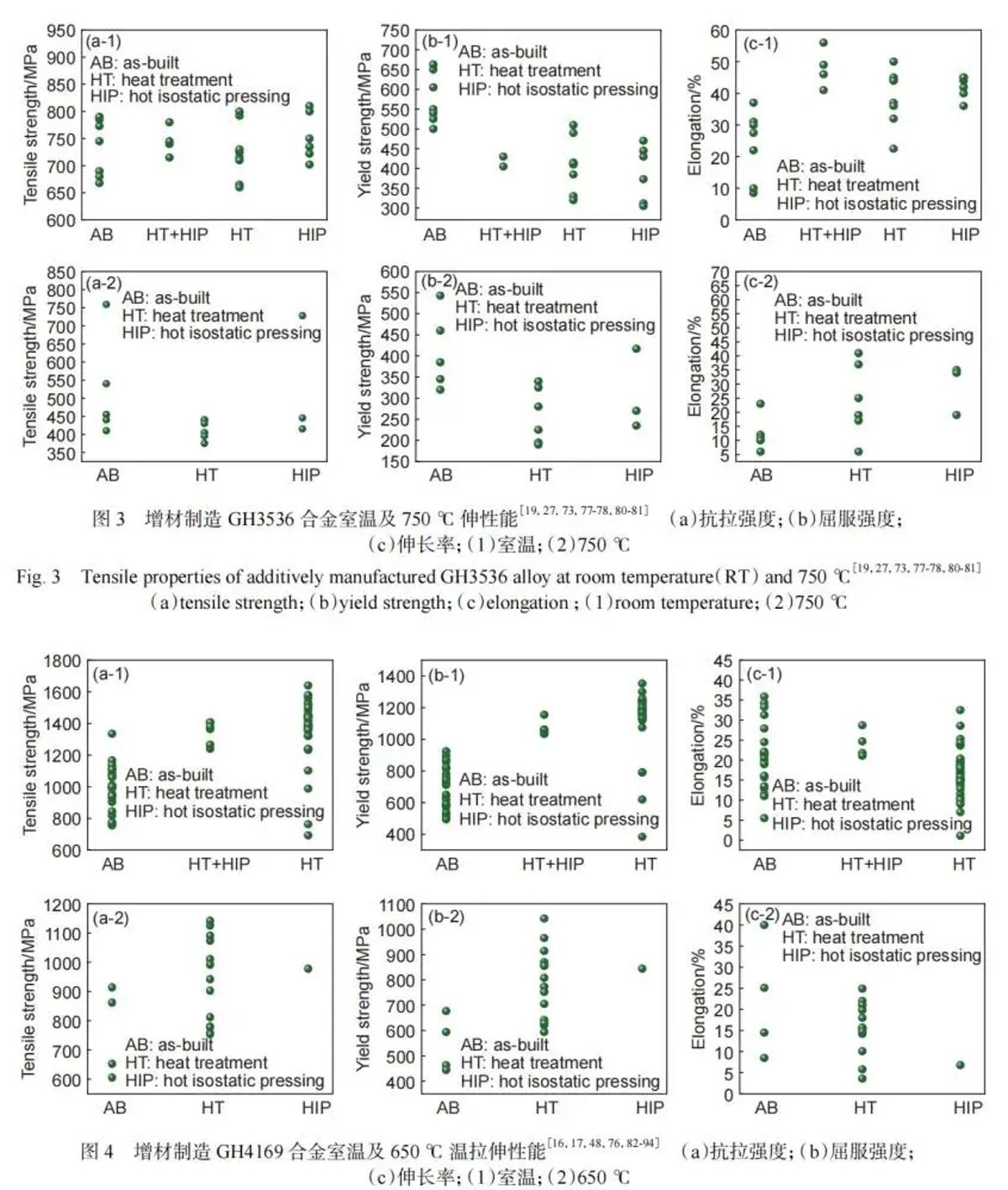
目前,增材制造镍基高温合金构件已在航空发动机及燃气轮机中得到了初步应用。在航空发动机领域,国内的中国航发北京航空材料研究院、中国航发商用航空发动机有限公司、北京航空航天大学、西北工业大学、华中科技大学、中国科学院金属研究所、铂力特等单位对燃油喷嘴、涡流器、预旋喷嘴等航空发动机镍基高温合金零件的增材制造进行了研究。采用增材制造技术,可使燃油喷嘴的加工周期由6周左右缩短至一周以内,涡流器的加工周期由一个月左右缩短至3~5天[1,97]。
国际上,赛峰公司采用增材制造技术成形的镍基高温合金涡轮喷嘴通过了欧洲航空安全局认证[3]。印度斯坦航空公司制造了25kN发动机的镍基高温合金燃烧室机匣[3]。罗罗公司在进行新一代燃烧室制造时,首先采用增材制造技术制造8个燃烧室组件,再通过激光焊将组件焊接成1个整体(图6(b))。
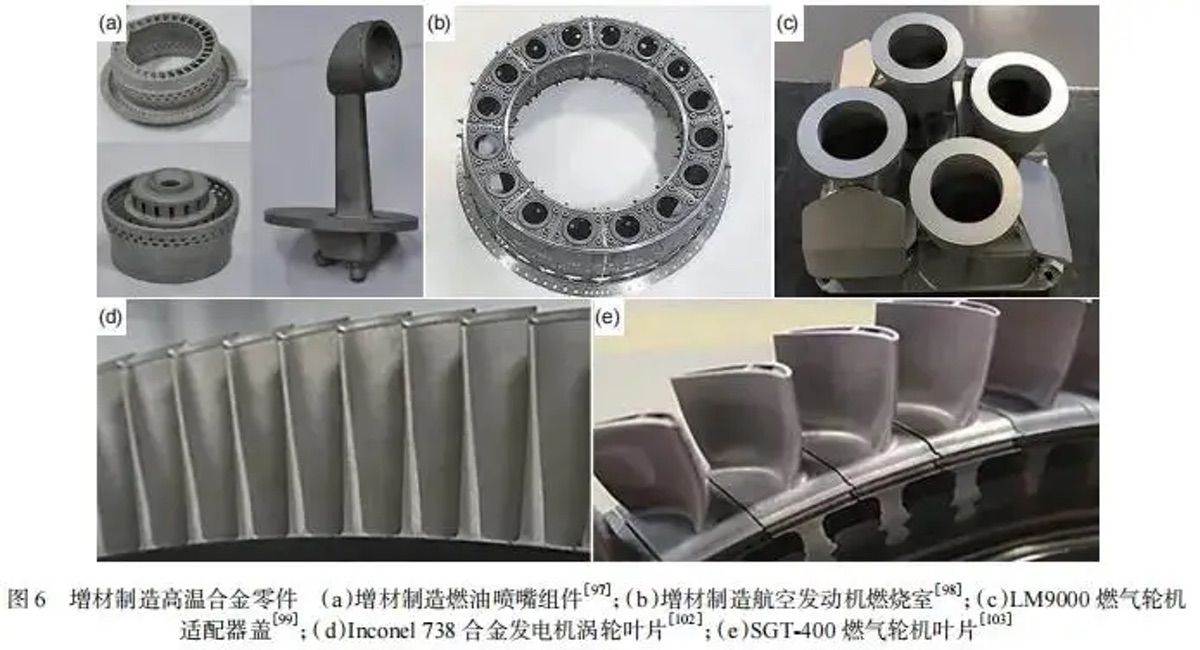
在燃气轮机领域,GE公司于2021年采用激光粉末床熔融成形LM9000燃气轮机适配器盖(图6(c))取代了原有的铸造零件。这些零件均为一对一替换,没有进行重新设计或零件合并,仅针对增材制造工艺进行了微小调整。传统的铸造零部件通常需要12~18个月的生产时间,而增材制造仅需要10个月时间,采用增材制造技术削减了约35%的制造成本[99-100]。
美国橡树岭国家实验室与SolarTurbines合作,利用电子束熔融技术制备了Inconel738合金发电机涡轮叶片(图6(d))。他们计划后续利用增材制造技术成形复杂内部冷却通道,使涡轮机在更高温度下运行,以提高发电效率[101-102]。
为改善镍基高温合金涡轮叶片的热传递和冲击冷却效果,德国西门子公司采用激光粉末床熔融技术为SGT-400燃气轮机制备了具有复杂内部结构的叶片(图6(e)),叶片已在1250℃下通过了13000r/min旋转速度条件下的满负荷考核[1,103-104]。2017年,曼恩机械在MGT6100燃气轮机中使用了增材制造涡轮叶片,率先在世界上实现了复杂结构增材制造高温合金涡轮导向叶片的应用[105]。
5 总结与展望
本文综述了增材制造镍基高温合金在组织、缺陷及性能方面的研究进展,并介绍了增材制造镍基高温合金零件在航空发动机及燃气轮机中的应用情况。可以看到,虽然增材制造镍基高温合金在理论研究及工程应用方面都已取得巨大突破,但在组织性能调控及缺陷控制等方面仍存在一定问题,要实现增材制造镍基高温合金构件在航空发动机与燃气轮机中更广泛的应用,还需在以下方面进一步开展工作:
(1)设计增材制造专用镍基高温合金成分
合金成分设计要同时考虑材料的使用性能与加工性能,加工工艺对合金成分设计具有重要影响。目前,增材制造镍基高温合金主要使用传统牌号成分,而传统镍基高温合金的成分是基于铸造、锻造等工艺开发的,并不完全适合增材制造工艺。例如,易开裂是阻碍增材制造镍基高温合金应用的重要障碍之一,造成这一问题的主要原因是部分牌号镍基高温合金的成分在增材制造工艺条件下易形成凝固裂纹及液化裂纹。因此,需要针对增材制造工艺特点进行合金成分设计,充分发挥增材制造镍基高温合金的性能。
(2)建立增材制造镍基高温合金专用热处理/热等静压工艺
增材制造过程具有高温度梯度、高冷却速度和原位热循环等特点。与传统工艺制备镍基高温合金相比,增材制造镍基高温合金的显微组织表现出明显的各向异性,且第二相的种类、含量及分布等也可能存在差异,导致传统热处理制度不能完全适用于增材制造镍基高温合金。此外,部分牌号镍基高温合金在增材制造过程中易形成裂纹,需要进行热等静压处理使裂纹闭合,改善力学性能。但是,热等静压引起的显微组织变化可能导致力学性能恶化。因此,需要依据增材制造镍基高温合金显微组织与缺陷特点有针对性地建立热处理及热等静压工艺,改善力学性能。
(3)开发单晶高温合金叶片增材制造技术
单晶高温合金具有出色的高温性能,是制造航空发动机涡轮叶片的重要材料。目前,单晶高温合金叶片主要通过定向凝固技术进行制备。但是,铸造合金组织粗大、偏析严重、易形成铸造缺陷,制约了高温合金性能的充分发挥。增材制造过程中,熔池具有极高的温度梯度与冷却速度,有助于减少成分偏析、疏松以及组织粗大等问题。
通过增材制造技术进行单晶高温合金叶片制备,可进一步提升其力学性能。然而,增材制造技术目前主要用于叶片修复,尚未用于叶片制造。近年来,有研究发现使用电子束粉末床熔融技术及激光光束整形技术可在多晶合金基体上实现单晶高温合金制备。这一发现使得直接使用增材制造技术进行单晶高温合金叶片成形成为可能,有必要进行系统深入研究。
(4)发展增材制造实时监测控制技术
增材制造镍基高温合金的显微组织是在快速凝固及原位热循环过程中形成的,熔池的凝固条件及原位热循环的升温/冷却速率是增材制造镍基高温合金显微组织的主要影响因素,决定了共晶组织、γ相、γ′相,析出相等的分布、含量及尺寸等特征。
此外,增材制造过程的温度场及应力场变化对材料变形开裂具有重要影响。尤其是对于易开裂镍基高温合金,需严格控制成形过程温度场及应力场才能获得成形质量良好的零件。同时,粉末及其他杂质在成形过程中的飞溅,可能导致未熔合、夹杂、层间开裂等缺陷。因此,有必要发展增材制造实时监测控制技术,依据温度、图像等信号对工艺参数进行调控,提高增材制造镍基高温合金成形质量稳定性。
(5)创新增材制造零件内表面处理技术
由于增材制造是逐层叠加过程,因此构件表面通常较为粗糙。虽然通过改进原材料粉末质量、调整成形过程零件摆放位置、优化工艺参数等手段可在一定程度上改善表面质量,但无法完全解决表面粗糙问题。
因此,增材制造零件必须经过表面处理后方可使用。增材制造零件通常具有复杂的内部结构,而现有的表面处理手段(磨粒流、电化学腐蚀、水射流、振动抛光、喷砂等)难以对复杂内表面进行有效处理,是限制增材制造零件工程应用的关键技术瓶颈之一。因此,需要开发新的内表面处理技术,促进增材制造零件应用。
(6)引入人工智能技术
人工智能具有强大的数据分析处理能力,且自动化程度和工作效率更高。利用人工智能对设计数据进行分析,能突破人类思维限制,进一步实现零件结构的快速优化设计。此外,使用人工智能对增材制造过程中产生的数据进行处理,预测可能产生的缺陷及何时需要对设备进行维护。不仅可在生产过程中提前对工艺参数进行调整,还可减少计划外停机时间,提高产品合格率及生产效率。
同时,采用人工智能对材料数据进行挖掘,建立“材料成分-冶金缺陷-力学性能”关系,在实验之前进行成分优化筛选,节约时间和资源,加速增材制造专用镍基高温合金成分开发。因此,有必要将人工智能与增材制造技术进行结合,促进增材制造技术快速发展。
(7)推动增材制造技术创新
虽然使用现有增材制造技术生产的零件已在航空发动机与燃气轮机中实现应用,但未来仍需进一步对增材制造技术进行改进创新,满足更大的应用需求。通过增材制造技术的发展,优化零件成形精度、改善设备稳定性、提高制造效率。
同时,将增材制造技术与智能制造、数字化工厂等技术相结合,实现增材制造的数字化转型。此外,还需要考虑环保和可持续发展问题,实现增材制造技术的绿色化、环保化、可持续发展化。
(责任编辑:admin)
最新内容
热点内容