重220kg、4米级立柱一体成型,超酷的3D打印艺术立柱是如何完成的?
时间:2024-02-25 09:54 来源:酷鹰科技 作者:admin 阅读:次
在人们传统印象中,柱子的形象往往是单一突兀、占空间且影响美观的,但酷鹰科技团队通过超大尺寸高分子3D打印技术,打破传统造型局限,制作了一个4米高、大曲率、多镂空结构的超酷3D打印艺术立柱,呈现出别具一格的工业之美,使立柱成为空间造型的一大亮点。
3D打印技术的发展使得多种复杂造型结构得以实现,设计师获得了更大的设计自由度,采用参数化设计,一个具有多镂空多曲线复杂中空结构的立柱造型应运而生,将美学和力学融为一体,呈现出别样的美与个性。
打印选用20%玻璃纤维增强的ABS颗粒料,材料具有出色的机械性能与打印性能,性价比极高。
该立柱高4000mm,直径最宽处1024mm,重达220kg,通过机器人增材制造系统BRAM-P300E直接3D打印成型,整个立柱实现一体打印成型,无需任何拼接组装,如此大的装置,酷鹰科技只花费了33小时便完成了整体打印工作。
机器人增材制造系统BRAM是酷鹰科技自主研发的基于机械臂结构的大尺寸非金属3D打印设备。BRAM-P300E是一款带有第七轴的型号,通过Y方向行程的拓展进一步拓宽打印灵活性与打印范围,成型尺寸可达5m*1.5m;同时凭借多轴系统,可以获得更大的打印自由度,使打印更加灵活。
值得一提的是,如此复杂结构立柱的一体打印成型的实现,还得益于酷鹰超大尺寸横向打印与回抽打印技术的研发完成。横向打印技术可以突破打印设备的高度限制,实现超大尺寸部件的打印成型;而回抽打印技术则是通过实时调整熔体温度,改变熔体特性,实现回抽功能,实现复杂镂空造型结构的打印。
超高的打印效率、超大的打印尺寸、大曲率与复杂镂空结构造型的实现等,均展示了熔粒构造成型(FGF)3D打印技术在大型艺术装置、建筑景观等领域的巨大潜力。
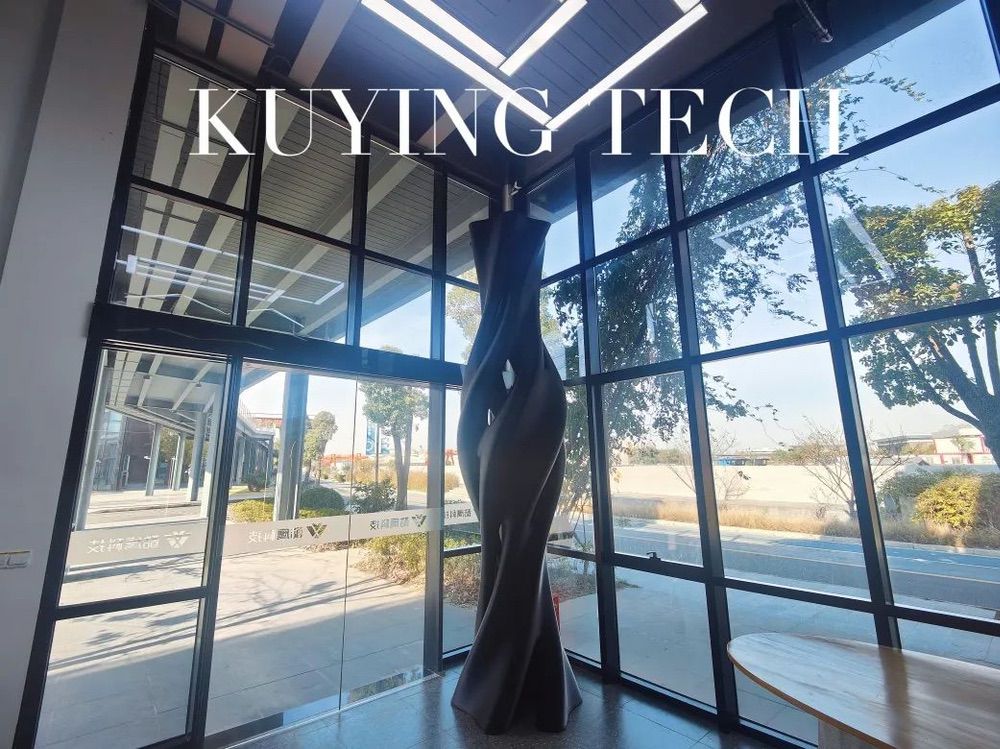

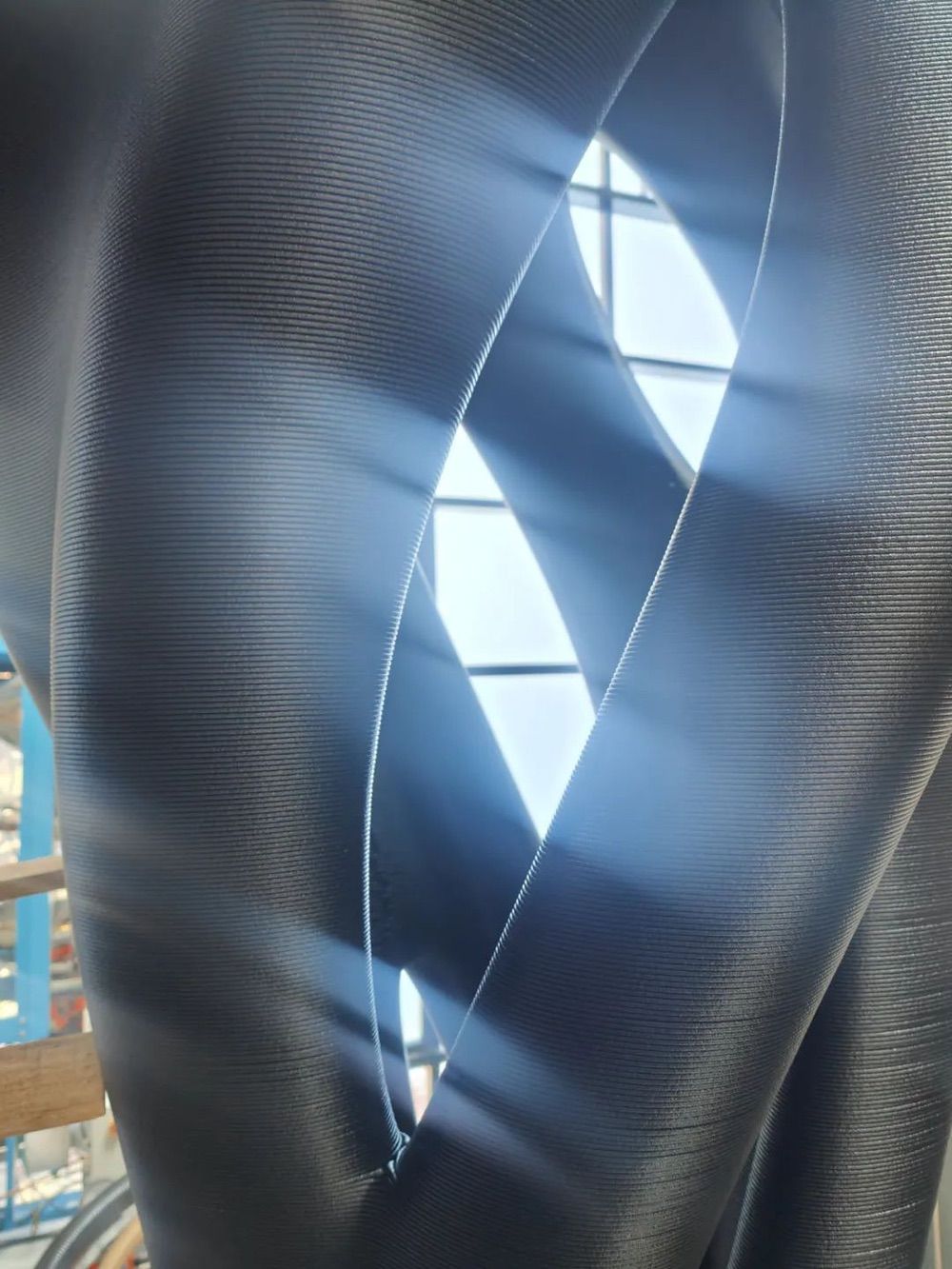
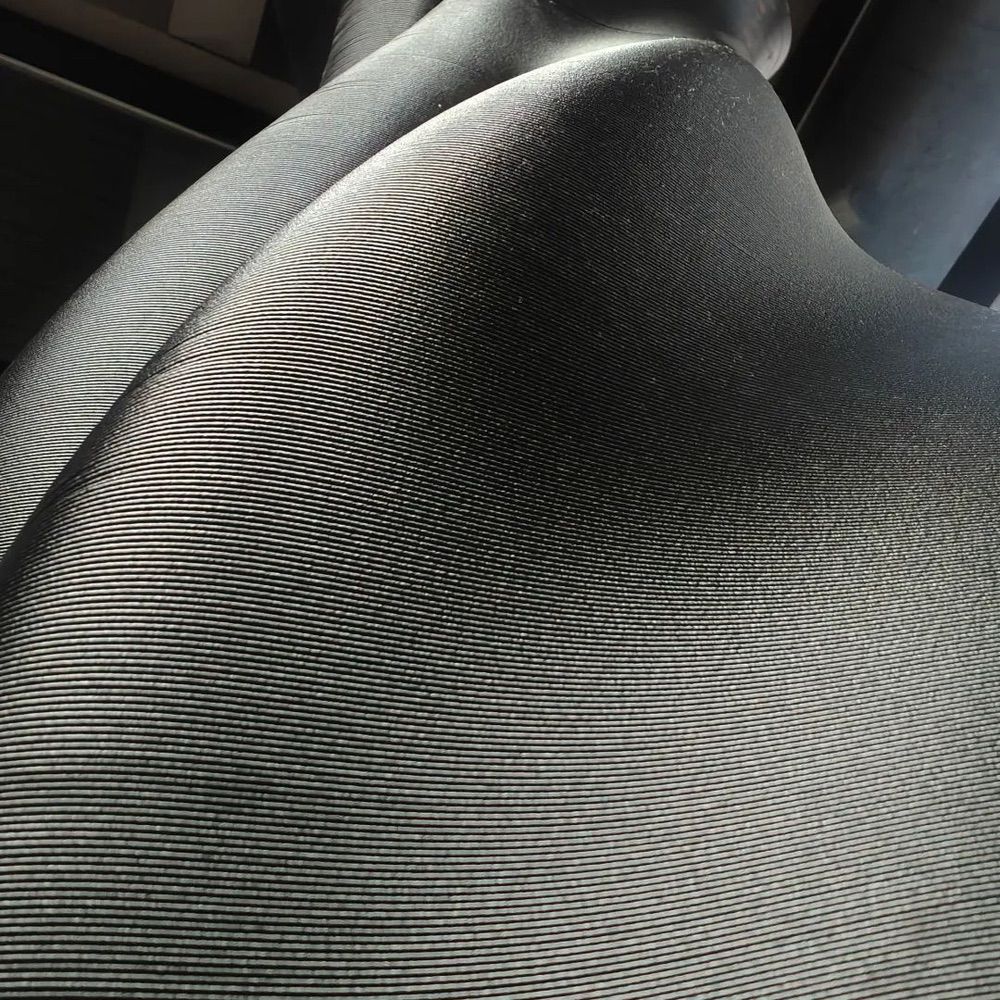

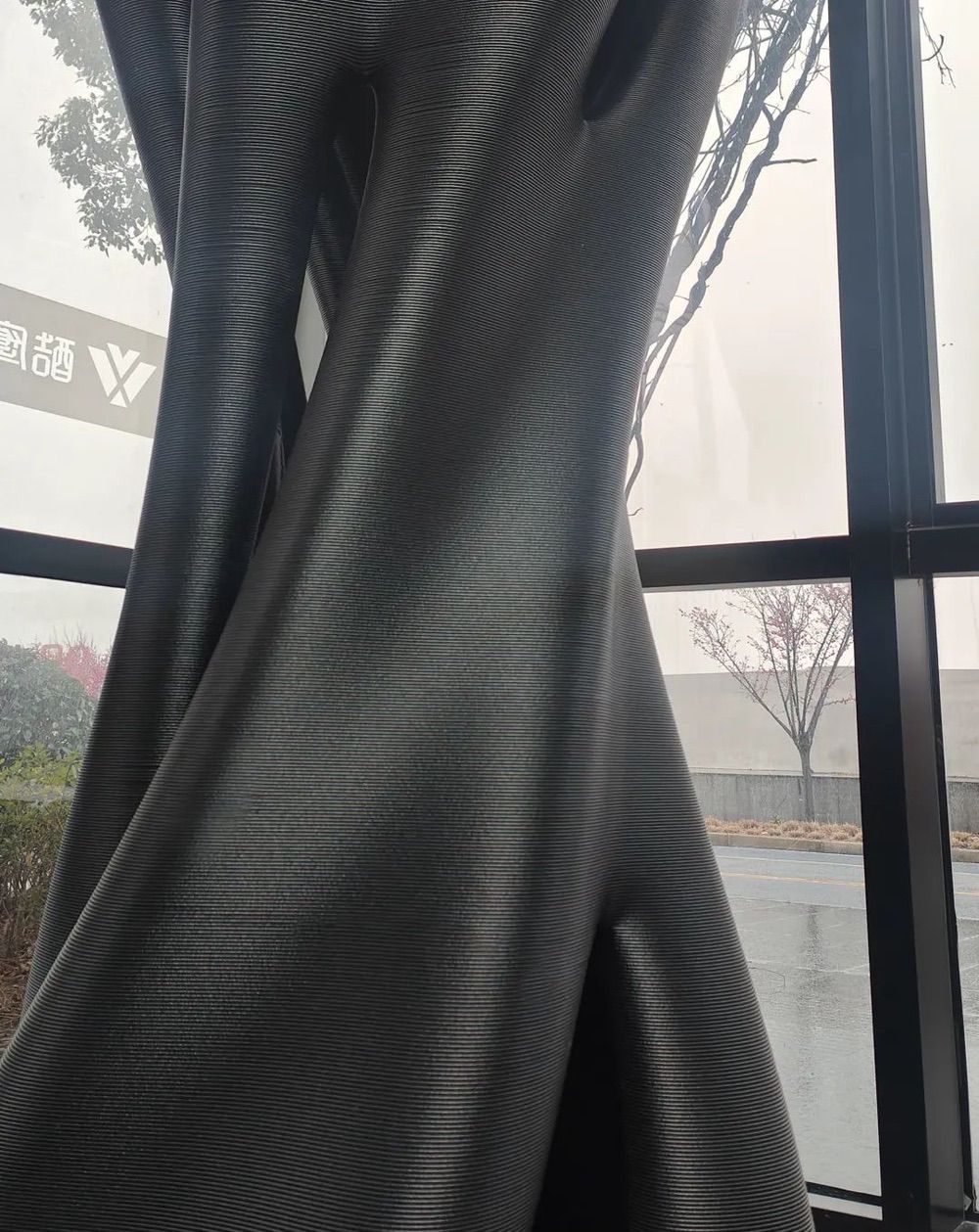
3D打印技术的发展使得多种复杂造型结构得以实现,设计师获得了更大的设计自由度,采用参数化设计,一个具有多镂空多曲线复杂中空结构的立柱造型应运而生,将美学和力学融为一体,呈现出别样的美与个性。
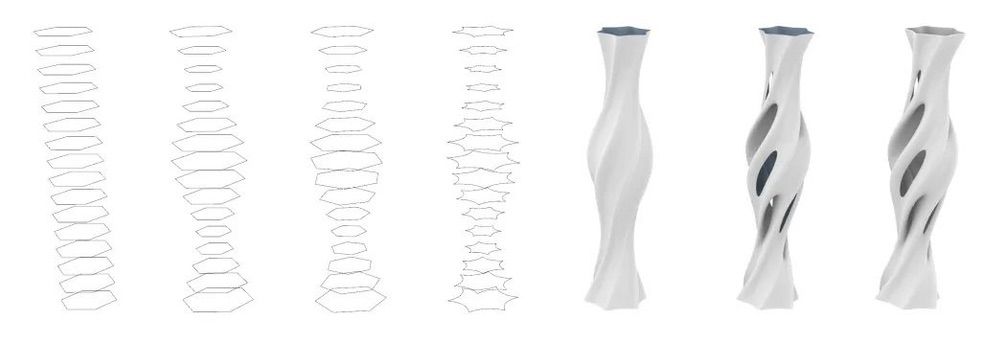
△参数化设计过程
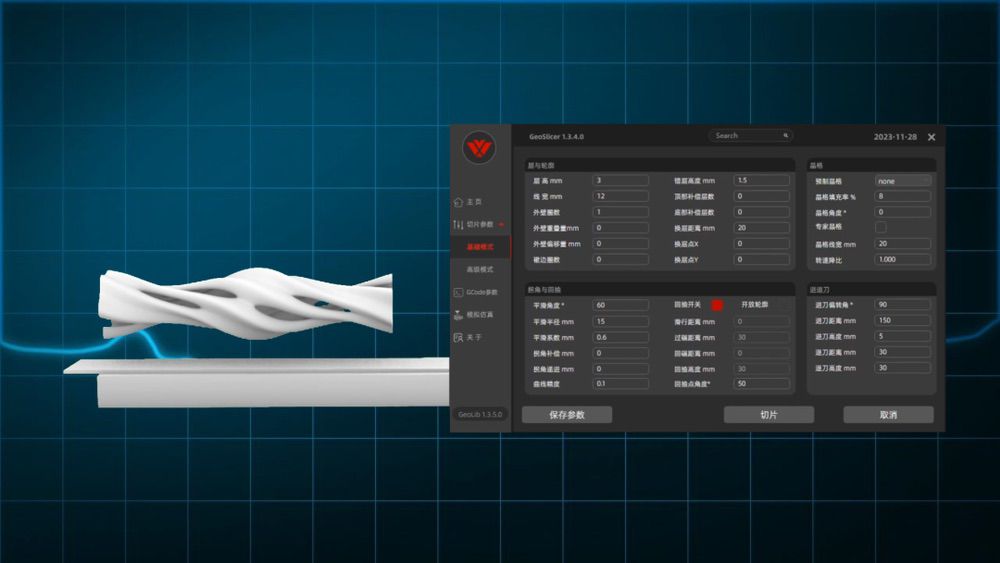
△使用酷鹰GeoSlicer for GH工艺切片软件调整工艺参数
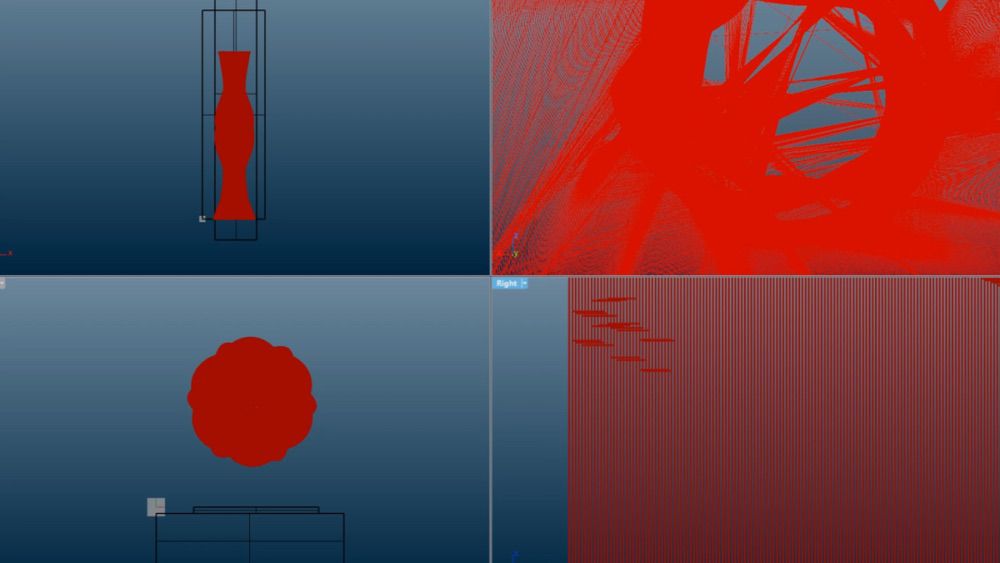
△模型切片处理
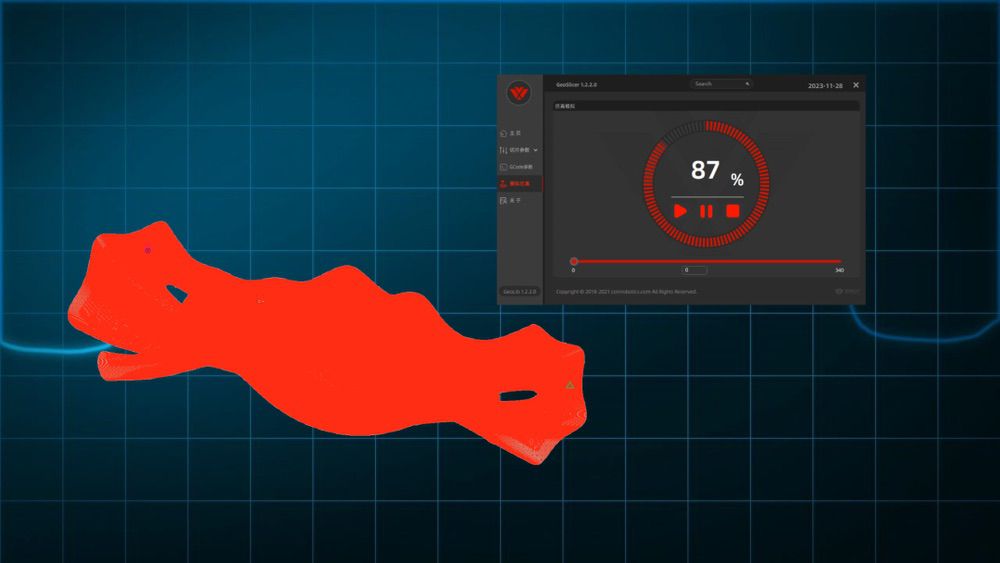
△打印前进行轨迹动态模拟仿真
打印选用20%玻璃纤维增强的ABS颗粒料,材料具有出色的机械性能与打印性能,性价比极高。
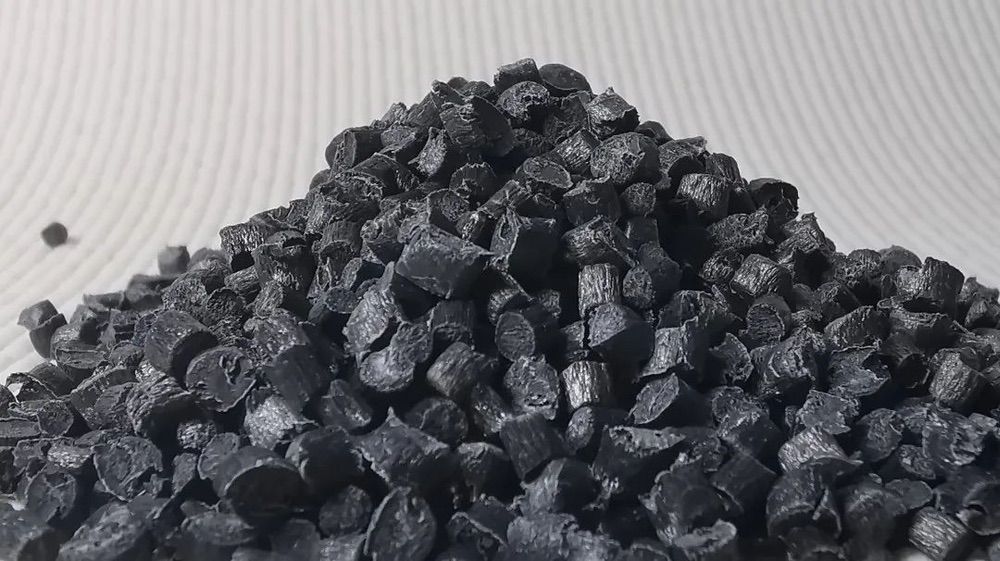
该立柱高4000mm,直径最宽处1024mm,重达220kg,通过机器人增材制造系统BRAM-P300E直接3D打印成型,整个立柱实现一体打印成型,无需任何拼接组装,如此大的装置,酷鹰科技只花费了33小时便完成了整体打印工作。
机器人增材制造系统BRAM是酷鹰科技自主研发的基于机械臂结构的大尺寸非金属3D打印设备。BRAM-P300E是一款带有第七轴的型号,通过Y方向行程的拓展进一步拓宽打印灵活性与打印范围,成型尺寸可达5m*1.5m;同时凭借多轴系统,可以获得更大的打印自由度,使打印更加灵活。
值得一提的是,如此复杂结构立柱的一体打印成型的实现,还得益于酷鹰超大尺寸横向打印与回抽打印技术的研发完成。横向打印技术可以突破打印设备的高度限制,实现超大尺寸部件的打印成型;而回抽打印技术则是通过实时调整熔体温度,改变熔体特性,实现回抽功能,实现复杂镂空造型结构的打印。
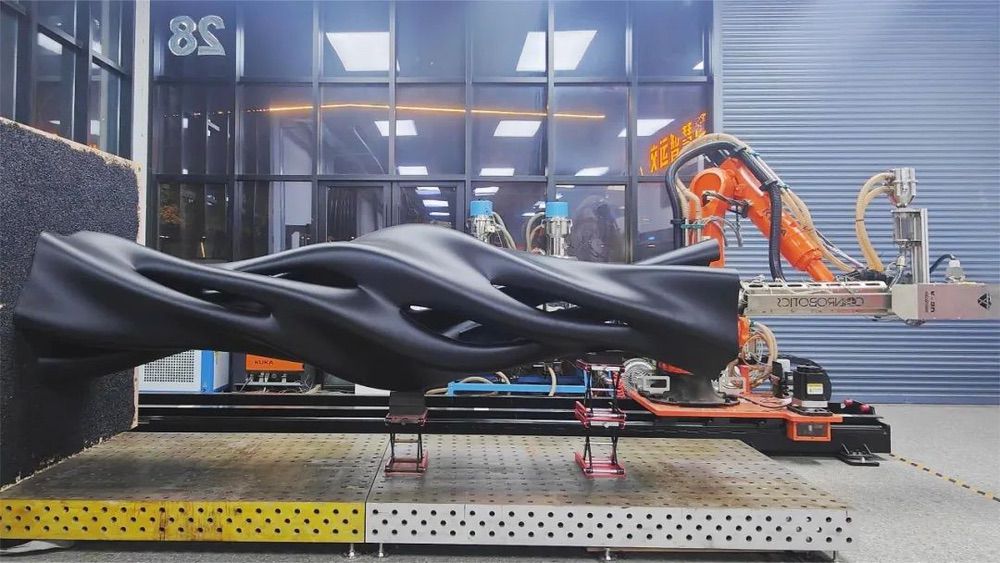
△横向打印技术
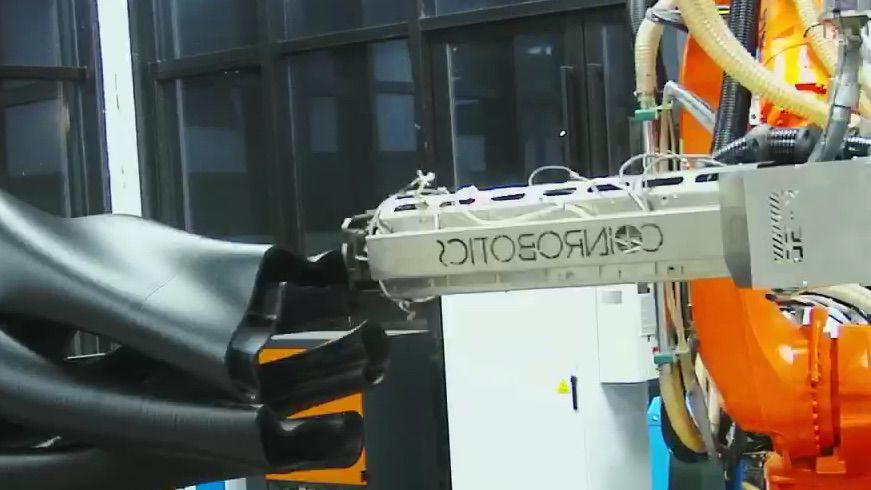
△回抽打印技术
超高的打印效率、超大的打印尺寸、大曲率与复杂镂空结构造型的实现等,均展示了熔粒构造成型(FGF)3D打印技术在大型艺术装置、建筑景观等领域的巨大潜力。
(责任编辑:admin)
相关内容
最新内容
热点内容