粉床熔融金属3D打印的模拟仿真–用计算逼近现实
万道强光,从天而降;飞沙走石,电光石火;所到之处,皆为“焦土”……
这不是世界末日,不过是从粉末的角度去看粉末熔融金属成形过程罢了。瞬态的反应,很难用传统的模型进行精确地描述,而熔融过程又决定成品的质量。模拟仿真可以弥补精确模型难以预测的物化过程,为这个工艺提供更多的指导。靖哥请到了彭浩博士为大家解读当前金属3D打印仿真模拟领域的主要进展。
作者简介
彭浩,本科毕业于华中科技大学机械设计制造及其自动化专业,博士毕业于University of Missouri, Columbia机械与航空工程系,目前在University of Notre Dame攻读博士后,专注于金属3D打印的仿真模拟工作。
开篇语
以粉床熔融成形技术(PBF)为代表的金属3D打印在近些年逐步由实验室走向市场。粉床熔融金属3D打印通过激光或者电子束层层熔化金属粉末,能够一次性制造出材料性质媲美锻件的复杂金属零件。然而,目前金属3D打印也存在很多缺陷,比如产量低,不确定性大,零件尺寸精度低等。到目前为止,金属3D打印的参数优化主要依赖于反复实验。然而实验会耗费大量的时间,人力和资金。因此,通过计算机模拟仿真来了解金属3D打印的机理,在打印零件之前通过计算机提前优化打印的各项参数,便成为克服金属3D打印缺陷的一条捷径。
1、背景
由于粉床熔融金属3D打印中所用的金属粉末尺寸大约为50微米,激光束或者电子束的最小聚焦直径也在100微米左右,然而需要打印的零件尺寸却常常大于几十或上百个厘米,如果在微米尺度上直接模拟整个大型零件,有人估计以现有的计算机所需要的时间是5.7x10^18年(宇宙的年龄才不到1.4x10^10年)。此外,在金属3D打印中的物理过程也是极其复杂的如图1。整个物理过程涉及到热传导、热辐射、热对流、热应力、金属粉末相变、熔池自由表面流体流动、流体润湿性、流体表面张力等等多领域多学科的复杂物理过程。这些过程的模拟仿真不仅需要对单一领域有深刻了解,更需要各个学科领域之间的通力合作。总的来说,金属3D打印的模拟仿真需要在一个多尺度多物理场(multi-scale and multi-physical)的大框架下进行。下面就对金属3D打印中的几个主要物理过程的模拟仿真做一一介绍。
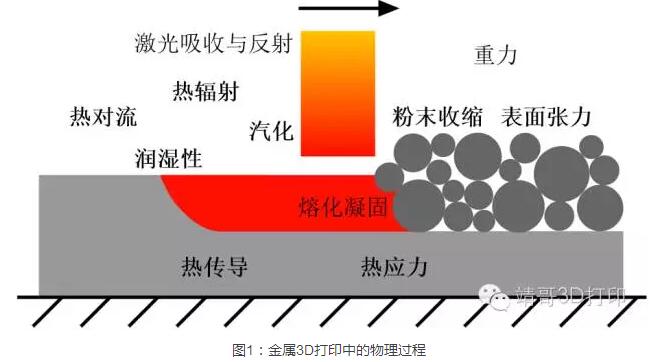
2、粉床仿真
a)现状与优势:
金属3D打印中的粉床由直径大小不等的金属粉末构成,粉末一般接近球状,大小一般呈现正态分布,不同打印设备所用的金属粉末大小都有所不同,平均直径在50微米左右。在激光或电子束烧结之前,这些粉末由平铺刀刃(recoater blade)或者滚筒(roller)平铺到打印平台上。目前模拟金属粉末平铺过程最常用的方法是离散单元法(DEM)如图2,金属粉末的不同颜色代表了不同的运动速度。通过离散单元法可以模拟不同大小金属颗粒在平铺刀刃或者滚筒推动下的运动情况。
b)局限:
离散单元法只能模拟有限数量的金属颗粒。目前能够模拟的金属颗粒数量最多在百万数量级,远少于实际金属3D打印中的金属颗粒数量。
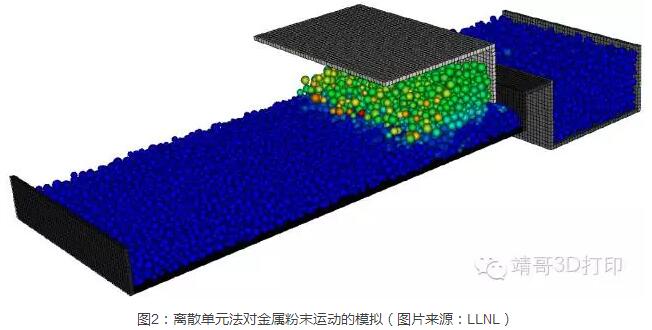
3、热源仿真
a)现状与优势:
在模拟激光或者电子束时,最常见也是最简单的方法是应用Lambert-Beer吸收定律。该定律假设热源强度在打印平面上呈现高斯分布,而在垂直于打印平面方向,热源强度呈指数级递减。不过,Lambert-Beer吸收定律没有解决热源的吸收率问题。金属颗粒对激光和电子束都有很强的反射或者散射效果,所有激光和电子束的能量只有一部分能够被金属颗粒吸收并转化成热能。目前计算金属粉末对激光的吸收率最常用的方法是光线追迹法(ray tracing)如图3。该方法假设激光束由一组平行光线组成,当光线与金属颗粒接触时在金属颗粒表面发生反射。每一束光线的运动轨迹都被追踪记录,最后通过统计算出金属粉床对激光的总体吸收率。通过光线追迹法可以计算出在不同金属材料、不同颗粒形状大小和不同光源直径下,金属粉床对光源的吸收率。
b)局限:
光线追迹法需要大量的计算资源才能预测到比较准确的吸收率。此外,在实际金属打印过程中,金属颗粒的形状大小和位置分布也很随机,因此目前的模拟仿真还不能利用光线追迹法实时计算光源的吸收率。
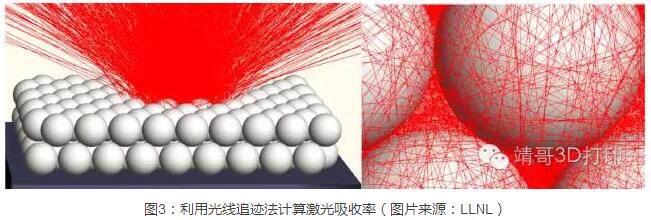
4、熔池仿真
a)现状与优势:
当金属颗粒被激光或者电子束熔化后会形成熔池(meltpool)。熔池的形状大小深度以及其动态变化直接影响了打印零件的品质。因此,很早的时候就出现了大量对熔池的模拟仿真如图4。熔池内部的金属液体在重力、液体表面张力和金属汽化形成的反冲压力的联合作用下进行着剧烈的对流运动。同时,主要的传热过程包括热传导、热对流、热辐射,主要的相变过程包括金属颗粒的熔融与凝固、液体金属的汽化等都集中在熔池附近。目前对熔池的模拟仿真主要利用有限体积法预测熔池内的金属液体的温度和流速。美国LLNL实验室对熔池的仿真还考虑了金属颗粒的熔化与凝固,金属液体汽化形成的反冲压力以及液体运动时的自由表面形状。
b)局限:
为了准确模拟熔池附近的复杂物理过程以及金属颗粒的几何形状,网格的大小经常需要被设定到几个微米,因此对熔池的模拟目前局限在几个毫米范围内,并不能直接用于常见零件的仿真。
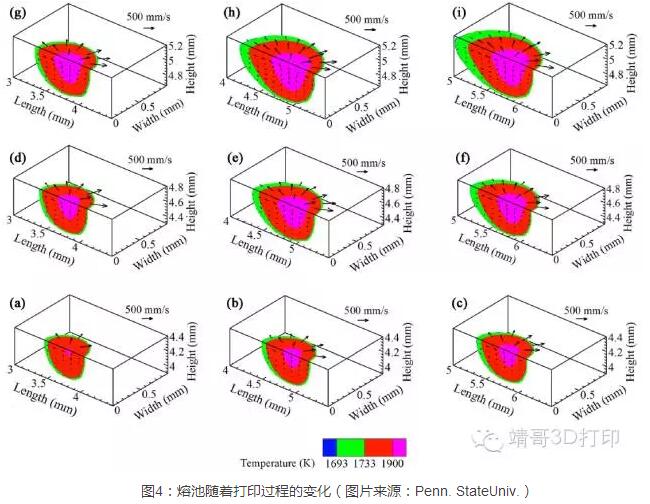
5、微结构仿真
a)现状与优势:
微结构(microstructure)形成于熔池凝固成固态时。微结构直接决定了材料的机械性能。微结构的模拟仿真通常分为两步。第一步,通过有限单元或者有限体积法预测熔池凝固时的冷却速率以及温度梯度。第二步,利用冷却速率和温度梯度对晶枝的成核以及生长进行仿真。图5展示了在不同冷却速率和温度梯度下,晶枝生长形成的微结构。
b)局限:
由于计算资源的限制,绝大多数的微结构仿真都只局限与二维,计算域也只有几十个微米。

6、零件热变形
a)现状与优势:
在金属3D打印中,零件经常打印在很厚的金属板基座上,打印完成后需要将零件从基座上取下。由于在打印过程中零件内部积累了大量的热应力,当零件从基座上取下后通常会出现很明显的变形,如图6。虽然变形是在打印完成之后发生的,导致变形的热应力却是在整个打印过程中积累的。因此,为了准确预测金属3D打印中的零件变形就必须要对整个打印过程进行模拟仿真。由于普通零件的尺寸通常有几十甚至上百厘米,对于这种大小的零件进行全真模拟几乎不可能实现,因此对于整个打印过程的抽象和假设就必不可少。最常见的抽象和假设就是将多个相邻的层合并成为更厚的一层进行传热和应力分析。经过抽象和假设,基于有限单元法的模拟仿真目前已经能够预测尺度在一米左右的大零件变形。
b)局限:
经过抽象和假设的热应力模型需要接受实验的检验。目前能够系统地与实验进行对比的仿真模型仍然很少。
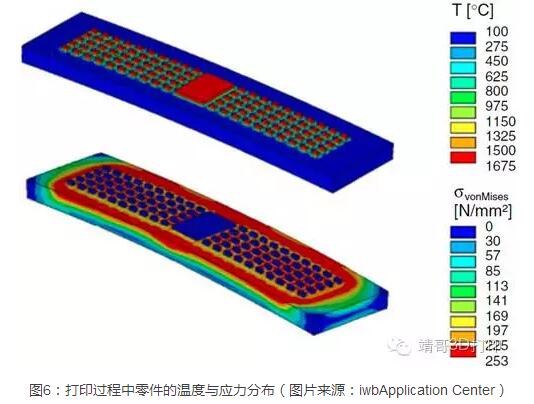
结束语
金属3D打印的模拟与仿真是打开金属3D打印的一把金钥匙。通过建立多尺度多物理场的金属3D打印模型并且利用高性能的并行运算,我们将不断逼近真实的金属3D打印过程,从而优化金属3D打印的参数,节省重复实验带来的资源浪费。
(责任编辑:admin)