通过激光粉末床熔合技术实现多材料界面结合强度的增强
导读:随着汽车行业对降低能耗的需求日益增长,汽车轻量化已成为关键趋势。铝合金以低密度特性成为实现轻量化的重要材料,但单一材料难以满足汽车零部件的多样化需求。因此,结合钢铁和铝合金的多材料的3D打印零部件,展现了在汽车领域的巨大应用潜力。
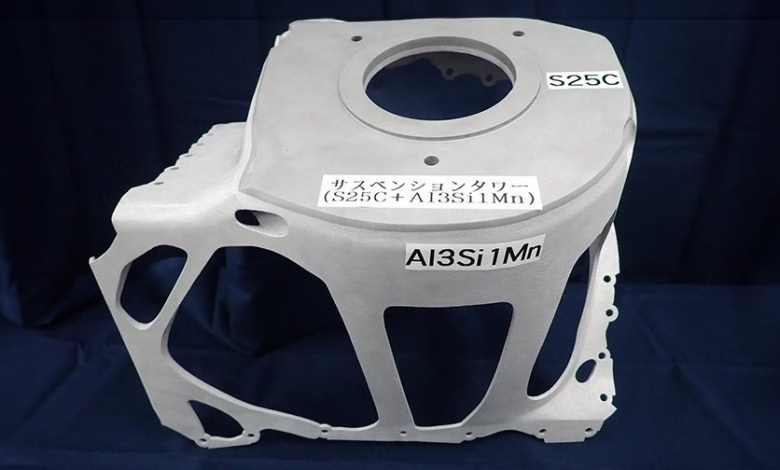
2024年12月18日,日本东北大学(Tohoku University)材料研究中心与新兴产业创造孵化中心的研究团队,已在多材料3D打印技术领域取得新的进展。通过激光粉末床熔合(LPBF)技术制造轻质且耐用汽车零件,为汽车制造业带来了新的可能性。
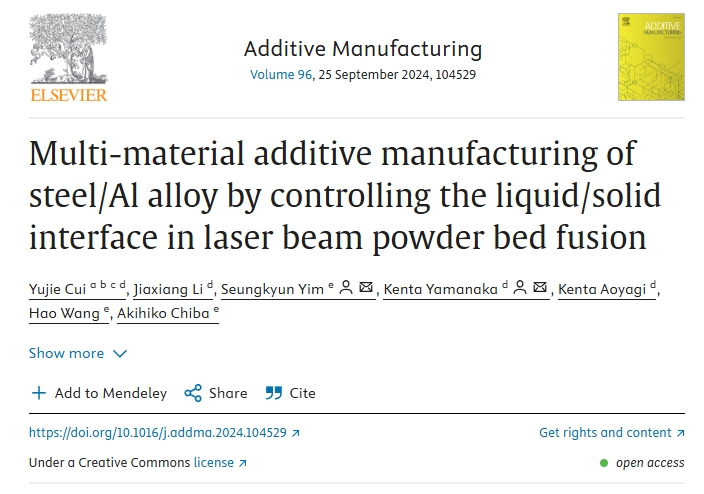
多材料3D打印技术凭借其在制造过程中的独特灵活性,已成为增材制造领域备受关注的焦点。然而,该技术在实际应用中面临挑战,尤其是当涉及到不同金属材料组合时,例如钢和铝。这些金属界面容易形成脆性金属间化合物,导致材料虽然变得更轻,但强度却有所下降。
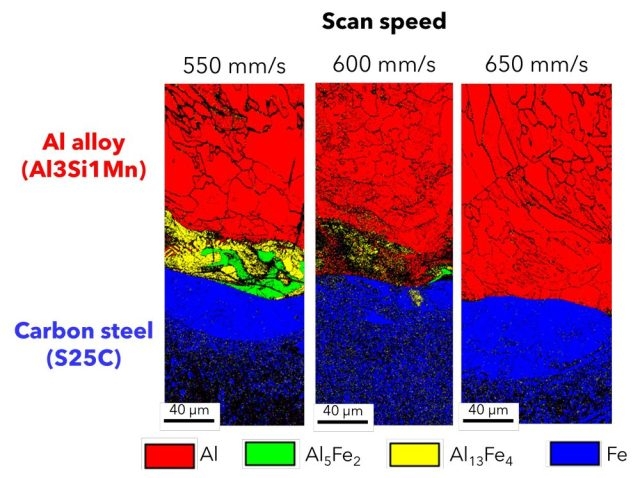
轻质高强度钢铝合金的多材料3D打印技术
这项研究的目的是生产一种重量轻但不影响强度的钢铝合金。为此,研究团队采用了激光粉末床熔合(LPBF)技术,并发现通过提高激光扫描速度,可以显著减少脆性金属间化合物(例如Al5Fe2和Al13Fe4)的形成。研究者提出,高速扫描引发的非平衡凝固过程有助于最小化溶质分配,从而降低材料弱点的产生。结果,最终产品展现出优异的结合界面强度。
东北大学特聘助理教授Seungkyun Yim强调:“简单地将两种金属并置并不能保证它们能够自发地结合。我们必须深入理解原位合金化的过程。”
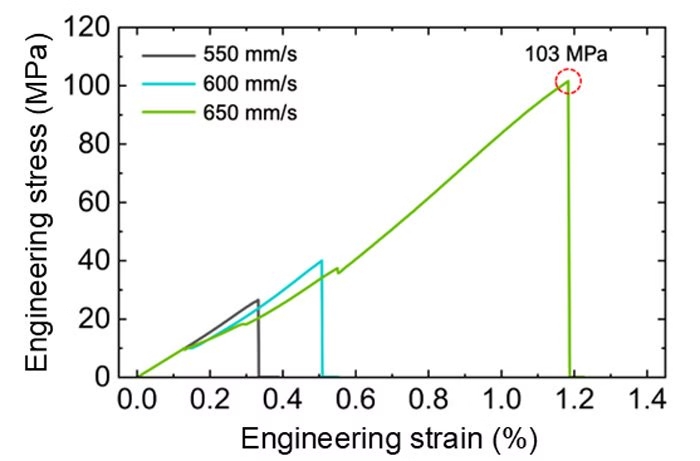
依托于这一发现,研究团队成功制造出了他们认为是世界上首个采用定制几何形状的全尺寸汽车多材料部件——悬架塔的原型。该研究小组计划将这些研究成果扩展至其它需要解决类似金属粘合问题的材料组合,以实现更广泛的应用。
这项研究不仅为多材料3D打印技术的应用开辟了新的道路,也为汽车制造业的轻量化和性能提升提供了新的解决方案。随着多材料3D打印技术的不断进步,预计未来将有更多高性能、轻质化的零件被应用到汽车及其它工业领域。
(责任编辑:admin)
下一篇:Sintavia推出首台采用nLIGHT光束整形技术多激光工业3D打印机,打印层厚可达150µm