加州大学伯克利分校开发电荷编程沉积(CPD)3D打印技术,用于制造轻型高性能天线
导读:随着航空航天对轻量化的需求不断增加,3D打印凭借结构优化优势,成为雷达设计的理想选择之一。
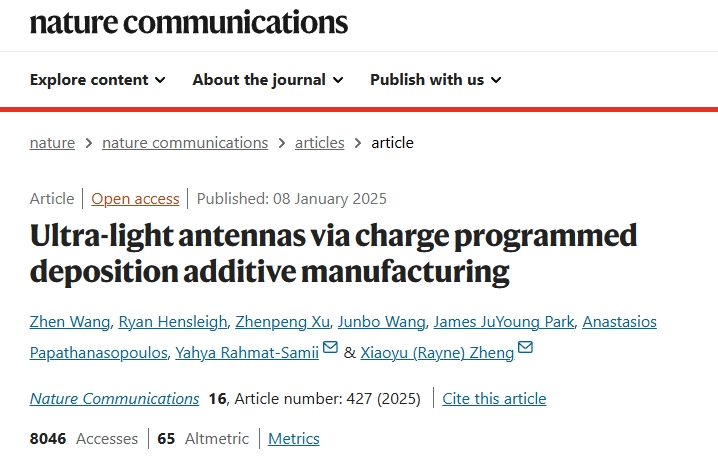
2025年4月24日,加州大学伯克利分校的研究人员开发了一种创新的3D打印技术——电荷编程沉积(CPD)。该技术能够利用电荷引导的多材料沉积工艺,制造出超轻、结构复杂的天线。与传统的光刻或减材制造工艺不同,电荷编程沉积能够直接3D打印由金属与电介质组成的复杂结构电磁设备.研究表明,使用市售桌面SLA打印机,CPD技术可以高效生产多种类型的天线,包括发射阵列、Vivaldi天线和喇叭天线。通过在单次打印中集成高导电性金属和电介质材料,电荷编程沉积显著减少了零件数量、重量和制造复杂度。此外,3D打印不受远距离供应链的限制,通过数字文件直接生产,提升了效率和灵活性。它能够减轻雷达系统重量,同时保持高性能,满足航空航天对轻量化和高性能的严格要求。

表面极性引导的3D打印
CPD工艺的核心基于电荷驱动的材料编程方法。在立体光刻打印过程中,研究人员将不同电荷极性(正电、负电或中性)分配到已打印的图案化介电基板的各个区域。这种“电荷镶嵌”方式决定了选择性化学镀过程中金属的附着位置。只有与区域电荷相反的区域才能吸引金属离子,从而精确地实现无刀具路径的三维导电轨迹图案化。
打印完成后,部件将经过一系列化学处理:钯离子作为催化剂沉积在电荷区域,随后铜被镀到带电区域。这项工艺能够生成光滑且无裂纹的铜路径,电导率为4.9×10⁷S/m,与退火铜相当,非常适合高频应用。
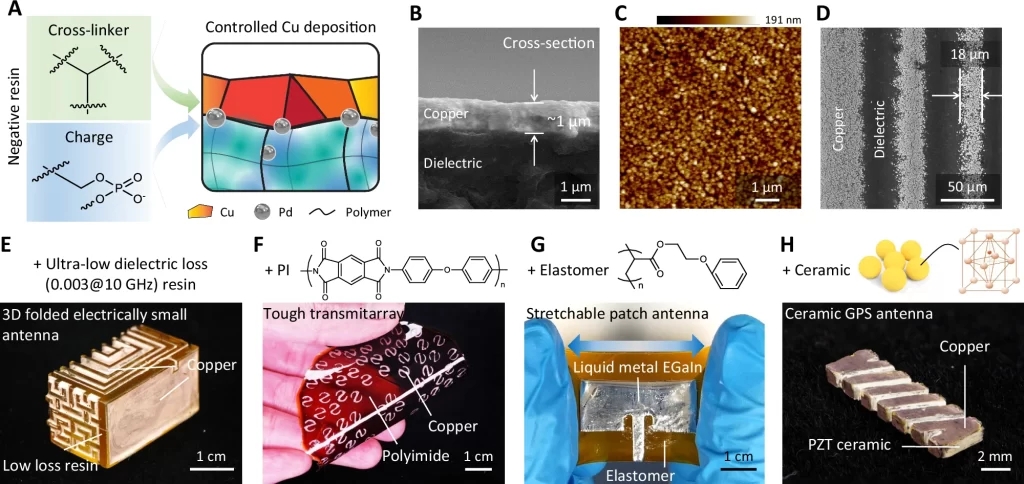
结构和功能的复杂性
研究人员通过制造一个圆极化19 GHz发射阵列天线,展示了这种方法的灵活性。该天线由三层互穿S环单元构成,重量仅为5克,相较于基于PCB的等效设计,减轻了94%的重量,同时保持了高方向性和增益。采用CPD技术制造的喇叭天线,具有隔膜偏振器和蜿蜒波导过渡,展示了此方法在创建复杂内部通道方面的能力。其它示例包括折叠微型天线、分形几何结构,以及使用弹性体和液态金属合金的可拉伸设计。为了解决构建体积的限制,研究团队设计了一种天线阵列模块化平铺策略,使得在不损失性能的情况下能够组装更大的孔径系统。
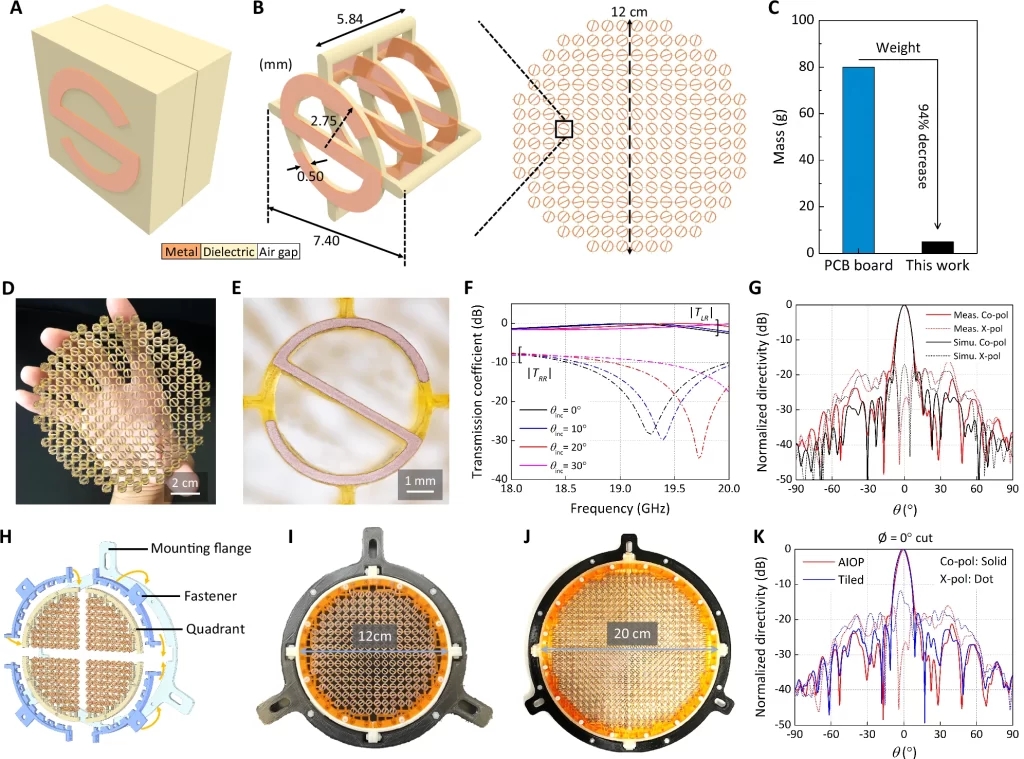
迈向可扩展、低成本的天线生产
与其它多材料增材制造方法不同,CPD工艺无需使用多个打印头、复杂的基板对准流程或高温烧结过程。相反,该方法基于标准SLA打印机,通过手动更换树脂即可实现,具备成本低、操作简便的优势。研究中所探索的材料涵盖聚合物、聚酰亚胺、陶瓷及弹性体,并通过定制树脂配方以支持电荷调制与铜沉积。这项研究显著降低了在空间受限或对重量高度敏感的平台上制造定制化高性能天线的门槛。CPD工艺支持快速原型开发、设计迭代与按需制造,避免了材料浪费,以及减材制造或多步骤组装带来的复杂性。
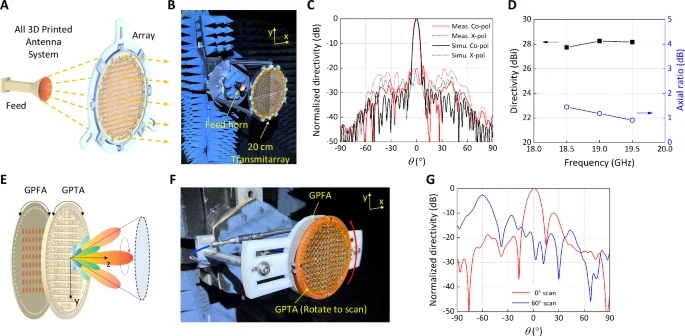
未来的研究方向将聚焦于树脂处理流程的自动化、材料体系的进一步拓展,以及其它功能性涂层(如磁性或压电薄膜)的集成,以满足下一代电子系统的需求。这项工艺在立方体卫星、6G基站、便携式和可穿戴设备等领域具备直接应用潜力,尤其适用于对重量、几何尺寸与电性能要求极为严苛的场景。例如,具有很大的潜力应用于军用雷达系统,包括复杂的相控阵雷达。早些时候,美国海军研究实验室利用3D打印技术制造优化的圆柱形天线阵列,与传统方法相比,实现了更紧凑、更轻巧的设计。
(责任编辑:admin)