3D打印个性化晶格超材料定制鞋垫
时间:2023-05-12 11:09 来源:西安交通大学机械制造系统 作者:admin 阅读:次
定制鞋垫通常用于糖尿病患者,以重新分配足底压力,降低产生溃疡的风险。3D打印技术的进步使3D打印个性化超材料的制造成为可能,这些材料的性能不仅来自基材,还来自超材料内部的晶格微结构。使用个性化超材料制造的鞋垫具有患者特定的几何形状和刚度,结合3D打印工艺的使用,为快速制造符合患者生理需求的定制鞋垫提供了可行性。华盛顿大学机械工程系的Yuri
F Hudak等研究者通过熔融沉积成型(Fused deposition modeling, FDM)技术,使用EPU41材料,采用定制的晶格结构,基于患者的足型和足底压力,为患者设计和制造了全3D打印鞋垫和混合3D打印鞋垫(图1),并与非3D打印的标准护理鞋垫进行对照,测试了不同鞋垫的抗剪刚度和抗压刚度,并研究了穿戴这3种鞋垫时最大足底压力峰值和压力时间积分在卸载区域的降低情况。证实了3D打印制造个性化超材料定制鞋垫的可行性,并证明了它们降低足底压力的能力
在1 K、10 K、100 K和1 M循环时,全3D打印鞋垫的原始厚度变形率分别为3.88%、4.30%、5.45%和9.49%。在相同循环次数下,混合3D打印鞋垫对原始厚度的变形分别为9.91%、20.58%、24.13%和25.20%。最后,在相同循环次数下,标准护理鞋垫样品对原始厚度的变形分别为10.74%、21.08%、23.59%和25.42%。
从每个鞋垫样品的剪切刚度来看,标准护理鞋垫的最高剪切刚度为223 kPa,其次是全3D打印小晶格鞋垫(191 kPa)、混合3D打印小晶格鞋垫 (160 kPa)、混合3D打印大晶格鞋垫(122 kPa),最后是全3D打印大晶格鞋垫(109 kPa),说明在给定剪切位移下,在测试的剪切应变范围内,标准护理鞋垫的刚度最高。
研究者还测试了穿戴不同鞋垫时足底压力的降低情况。实验表明,无卸荷区标准护理鞋垫在行走过程中足底压力峰值较普通标准鞋垫增加(平均值±标准差:268.8±7.0 kPa vs. 248.8±9.9 kPa)。混合和全3D打印鞋垫在卸载区域的最大足底压力峰值值分别为207.8±9.6kPa(与普通标准鞋垫相比减少了16.5%)和209.3±2.9kPa(与标准化鞋垫相比减少了15.9%)(图5)。
参考文献:
Hudak Y F, Li J-S, Cullum S, et al. "A novel workflow to fabricate a patient-specific 3D printed accommodative foot orthosis with personalized latticed metamaterial." Medical Engineering & Physics(2022)
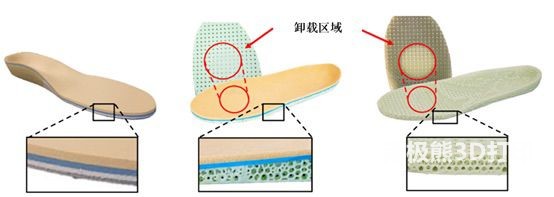
图1 不同制造方式的定制鞋垫
该研究提出了一种新的定制鞋垫的生产流程,这种流程实现了完全定制的鞋垫,符合患者的脚型和鞋子,并结合患者特定的足底压力,通过设计卸载区域的鞋垫刚度降低来缓解足底压力。首先由矫形师使用高精度3D可见光扫描仪扫描患者足部印模生成数字文件。然后, 使用扫描后处理软件对扫描数据进行处理,并将印模导出为STL文件,用于以后针对患者的鞋垫设计。同时,研究者使用鞋内足底压力传感器在实验室环境下的平地上行走时收集患者特定的足底压力。使用定制的MATLAB算法计算足底压力数据,并使用200
kPa的阈值定义卸载区域。在鞋垫模型设计软件中,手动标记足部的解剖标志,包括脚跟和第一和、五跖骨头,以辅助设计合适的鞋垫形状与尺寸,鞋垫建模以匹配患者足部扫描的几何形状。然后,根据之前使用CAD软件定义的足底压力图,导出得到的一体式鞋垫模型,并进一步划分为正常压力区域和卸载区域。在鞋垫内部结构的晶格优化阶段,研究者对晶格单元尺寸和厚度参数进行调整,直到打印出的鞋垫的刚度符合预期效果。最后,使用FDM工艺对设计好的鞋垫模型进行打印。
图2 鞋垫制造流程
在该研究中,研究者对图1中3种鞋垫进行了耐久性和抗压刚度测试,并测量了其剪切刚度。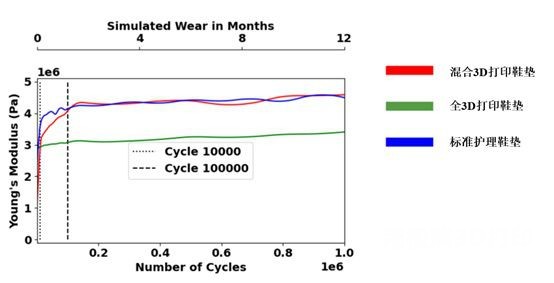
图3 耐久性和抗压刚度测试
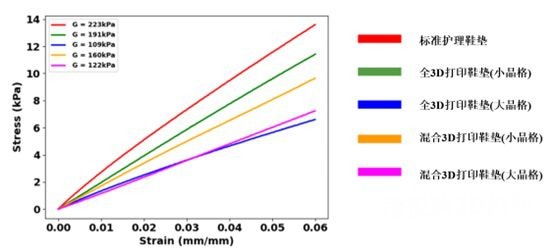
图4 鞋垫样品的剪切刚度
在耐久性和抗压刚度测试中,混合3D打印鞋垫样品与标准护理鞋垫样品的耐久性曲线非常接近,而全3D打印鞋垫样品在100万次循环过程中显示出较低的刚度增长(图3)。在1 K、10 K、100 K和1 M循环时,全3D打印鞋垫的原始厚度变形率分别为3.88%、4.30%、5.45%和9.49%。在相同循环次数下,混合3D打印鞋垫对原始厚度的变形分别为9.91%、20.58%、24.13%和25.20%。最后,在相同循环次数下,标准护理鞋垫样品对原始厚度的变形分别为10.74%、21.08%、23.59%和25.42%。
从每个鞋垫样品的剪切刚度来看,标准护理鞋垫的最高剪切刚度为223 kPa,其次是全3D打印小晶格鞋垫(191 kPa)、混合3D打印小晶格鞋垫 (160 kPa)、混合3D打印大晶格鞋垫(122 kPa),最后是全3D打印大晶格鞋垫(109 kPa),说明在给定剪切位移下,在测试的剪切应变范围内,标准护理鞋垫的刚度最高。
研究者还测试了穿戴不同鞋垫时足底压力的降低情况。实验表明,无卸荷区标准护理鞋垫在行走过程中足底压力峰值较普通标准鞋垫增加(平均值±标准差:268.8±7.0 kPa vs. 248.8±9.9 kPa)。混合和全3D打印鞋垫在卸载区域的最大足底压力峰值值分别为207.8±9.6kPa(与普通标准鞋垫相比减少了16.5%)和209.3±2.9kPa(与标准化鞋垫相比减少了15.9%)(图5)。
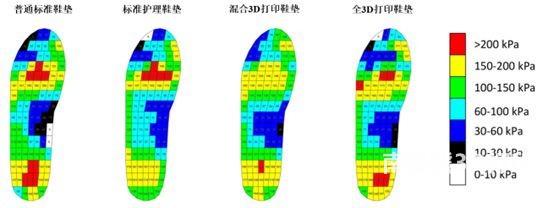
图5 穿戴不同鞋垫时足底压力分布情况
该研究表明,两种使用3D打印工艺制作的鞋垫至少与标准护理鞋垫一样耐用,而且全3D打印的鞋垫在重复载荷的作用下有更低的刚度增长,表明其具有更高的耐用性能。因此,从患者的角度来看,鞋垫的舒适度可能与标准护理鞋垫相当或超过标准护理鞋垫。3D打印鞋垫制作方法和材料选择表明,其具有更低的剪切刚度,这可以减少佩戴者足底组织上的剪切应力。并且通过控制鞋垫内部晶格大小可以实现区域控制抗剪刚度和抗压刚度的能力,以满足患者的特定需求。参考文献:
Hudak Y F, Li J-S, Cullum S, et al. "A novel workflow to fabricate a patient-specific 3D printed accommodative foot orthosis with personalized latticed metamaterial." Medical Engineering & Physics(2022)
(责任编辑:admin)
最新内容
热点内容