揭秘3D打印技术之铸造砂型3D打印(5)
时间:2016-08-22 18:27 来源:南极熊 作者:中国3D打印网 阅读:次
著名砂型3d打印机公司Exone
Exone公司就是一家该领域中的领先企业。早在1999年这家集团公司包括今天的企业负责人Rainer Höchsmann先生在内的工程师们就研发成功了砂型和砂芯用的3D打印机样机。今天,作为Exone公司经营业务的一个组成部分,它们的砂芯铸模3D打印技术已经发展成为国际上领先的技术。
Exone集团公司开发这项技术的主要目的是:经快速制造进入实际铸造生产之中。新一代造型机的成本和费用与传统造型机的相同,但却可以极大的提高铸件的质量和精度。目前,已有两种型号的设备可供用户选用:小型的S-Print和大型的S-Max。由于这一技术有着非常广泛的应用领域,因此它具有很强的生命力。ExOne的3D砂型、砂芯打印机产品具有很大优势,能取代现有工业生产中的复杂的砂型制作流程,采取的是Binder Jetting Techonolgy(喷墨砂型打印技术),SLS和SLA两种技术主要采用激光热熔技术,这种技术下3D打印机机的工作状态可以理解为以一个点一个点来成型,然后直接做出产品。喷墨砂型打印技术则是一个平面一个平面打印,直到做出产品的砂型,然后用传统的铸造技术和这个砂型制造出需要的产品。
目前S-Max系列产品最大能打印出长1.8米×宽1米×高0.7米的砂型产品,另外,因为只打印砂型而不是直接打印产品,所以可以用砂型制作各种金属的产品甚至各种合金都可以灌注入砂型成型。传统制造砂型的过程短则1个月多则需数月,而3D打印砂型缺耗时很少,比如一台发动机的3D打印砂型也只需11个小时就可制作完成。ExOne成立至今一共卖出72台3D打印机,每台售价在100万欧元左右,主要销售市场是美国、欧洲,以及亚洲。
直接铸型制造工艺和传统的铸型制造技术相比,直接铸型制造工艺具有无可比拟的优越性, 它不仅使铸造过程高度自动化、 柔性化、 敏捷化, 降低工人劳动强度,而且在技
术上突破了传统工艺的许多障碍, 使设计、 制造的约束条件大大减少, 具体表现在以下几个方面:
1. 无需模型。在传统铸造生产中,模型制造是一个重要环节。模样一般用木材、 塑料、 金属等材料由手工或机器加工而成, 有时需要钳工修理,费时耗资, 且精度不易保证。对一些形状复杂的铸件, 例如发动机叶片、 船用螺旋桨、 汽车缸体、 缸盖等,虽然目前有些模样的加工采用数控机床、仿形铣等先进的设备和工艺,但由于编程复杂以及刀具干涉对几何形状的制约都使难度增大, 造成成本高、 周期长;而直接铸型制造工艺则完全避免了传统铸型制造技术的这一最大缺陷, 从而在缩短砂型制造时间、 降低砂型制造成本等诸多方面, 都使砂型制造技术有了一个质的飞跃。
2. 制造时间短。 铸型的制造时间是指从铸型设计结束到制造完成用于浇铸之前的这一段时间。传统方法制造铸型必须先加工模样, 无论是普通加工还是数控加工, 模样的制造周期都比较长。 对于大中型铸件来说, 铸型的制造周期一般以月为单位计算。 由于采用计算机自动处理, 直接铸型制造工艺的信息处理过程一般花费几小时至几十小时。相对于整个铸造过程而言, 这一段时间可以忽略。
3.一体化造型。 传统造型由于需要将模型从铸型中取出,所以必须沿铸件最大截面处(分型面) 将其分开,也就是采用分型造型。 这样往往限制了铸件设计的自由度,某些型面和内腔复杂的铸型不得不采用多个分型面, 使造型、 合箱过程的难度大大增加,易使铸件产生错箱、 飞边等缺陷,加大了清理工作量和机加工量。直接铸型制造工艺采用堆积成形原理, 没有起模过程,所以分型面的设计并不是主要障碍。分型面的设计甚至可以根据需要不设置在铸件的最大截面处, 而是设在铸件的非关键部位。对于某些铸件, 完全可以采用一体化造型方法,即上、 下型同时成形。一体化造型的最显著的优点是省去合箱,减少设计约束和机加工量,使铸件的尺寸精度更容易控制。
4.型、 芯同时成形。由于采用离散/ 堆积成形原理, 因此直接铸型制造工艺很容易实现型、 芯同时成形。传统工艺出于起模考虑,型腔内部一些的结构设计成型芯,型、 芯分开制造, 然后再下芯将二者装配起来,装配过程需要准确定位,还必须考虑芯子的稳定性。直接铸型制造工艺制造的铸型,型芯可同时堆积而成, 无需下芯装配,位置精度更易保证。
5.无拔模斜度。 由于直接铸型制造工艺是无模样的直接堆积造型,没有拔模问题,所以传统铸型设计必不可少的拔模斜度等约束在此失去意义, 因而可减轻铸件重量。
6.可制造含自由曲面( 曲线)的铸型。传统工艺中,采用普通加工方法制造模样的精度难以保证;数控加工编程复杂,另外刀具干涉等障碍无法克服。 所以传统工艺制造含自由曲面或曲线的铸件精度不易保证。 而基于离散/堆积成形原理的直接铸型制造工艺, 不存在成形的几何约束,因而能够很容易地实现任意复杂形状的造型, 且易保证精度。
7.可制造组合零件( 功能零件)。 由于传统铸造工艺的限制,在零件的设计制造过程中,某功能件需要分成几个零件,分别进行铸造和加工, 然后装配而成。 而基于离散/堆积成形原理的直接铸型制造工艺, 无需模型,不存在起模问题对零件的形状限制, 可以将传统工艺下的几个零件组合成功能零件一次成形,减少了机加工和装配工作量,彻底消除了加工和装配误差带来的精度损失。可见这项新工艺还可以带来设计思想的变革,可大幅度提高生产效率,降低制造成本。
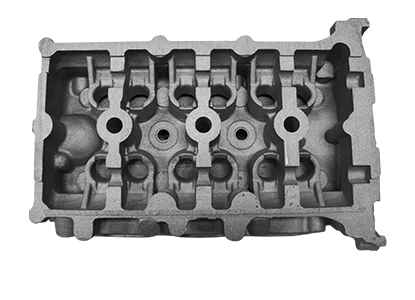
中国3D打印点评认为在当今技术创新、技术融合的大背景下,将快速成型方法引入传统铸造生产中,会产生出更加适应现代经济社会发展的新型铸造工艺,也将对传统铸造工艺的升级提高起到良好的助力作用,从而使得铸造行业获得科学发展、可持续发展。
(责任编辑:admin)
最新内容
热点内容